4 fluid dynamics of shutoff valve operation, 5 noise, Nordstrom valves – Flowserve Nordstrom Dynamic Balance Plug Valve and Double DB Plug Valve User Manual
Page 10
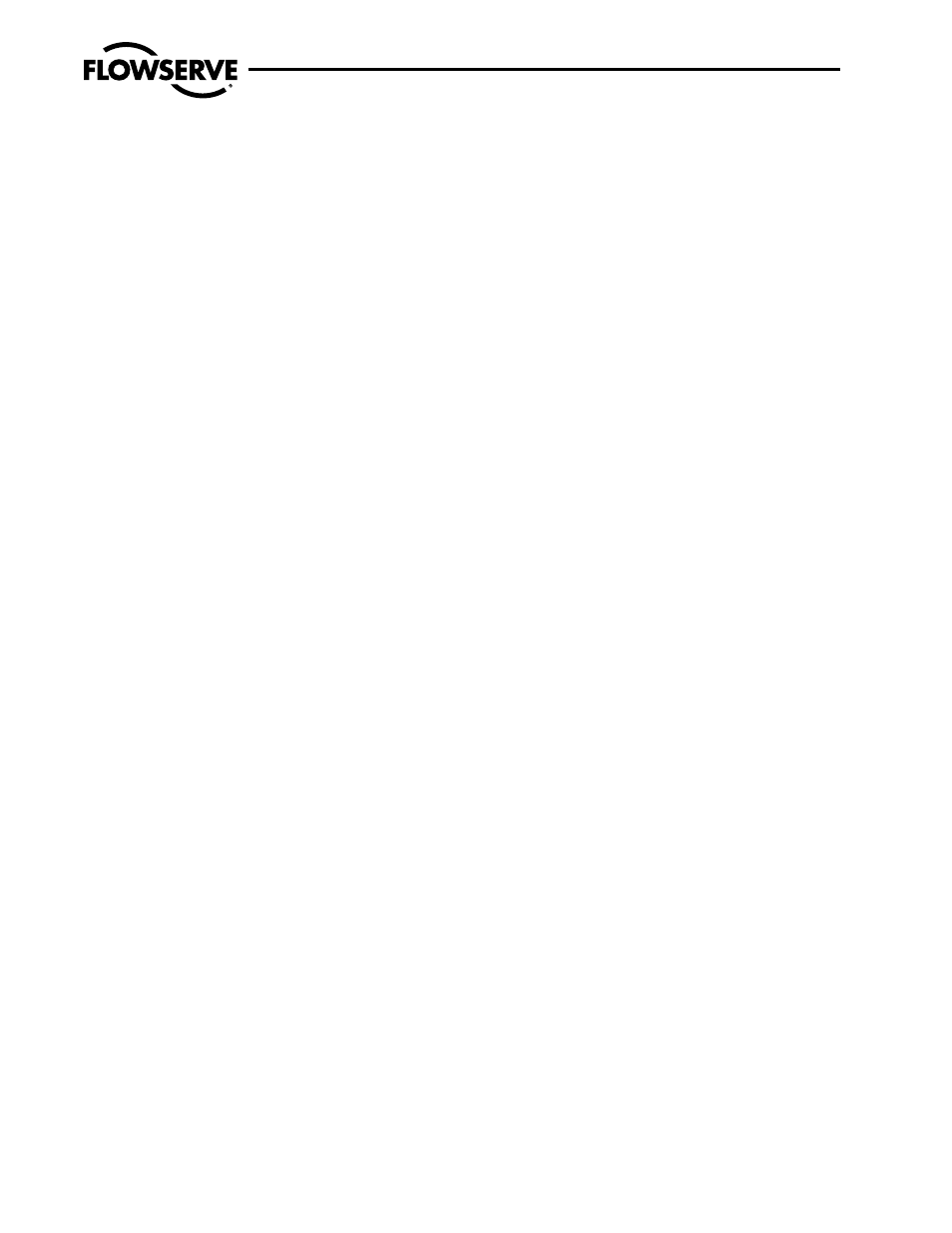
Flow Control
Nordstrom Valves
10
Dynamic Balance
®
Plug Valve and Double DB
®
Double Isolation Plug Valve
FCD NVENIM2005-01
of actuator manufacturer. Flowserve should be consulted when a
manually operated valve must be retrofitted with a power actuator.
a
CAUTION: Some valve actuators, when sized to provide
specified loading, may have much higher output at maxi-
mum switch or control settings and therefore may damage
valves if misadjusted. Valve and actuator manufacturer’s
instructions should be followed closely to prevent over-
loading valve stems and other structural parts. Successful
operation of power-operated valves requires a diligent
coordination of the skills and efforts of the valve specifier,
Flowserve, and the actuator manufacturer. Most applications
are problem-free, but miscommunication can lead to wide-
ranging problems, from unreliable operation to possible
valve or actuator damage.
4.4 Fluid Dynamics of Shutoff
Valve Operation
A flowing fluid in a piping system has mass and velocity. Anything
that causes a moving mass to change its velocity will experience a
reacting inertia force in proportion to the magnitude of the mass and
the rate of the imposed velocity change.
However, in the flow of gases the reacting inertia forces are inher-
ently moderated by the compressibility of the fluid that permits the
instantaneous velocity change to be effectively limited to the mass
of fluid in the immediate vicinity. This, in addition to the self-cush-
ioning capacity of the fluid column in the upstream pipe, effectively
precludes any significant problem of pressure surge in rapidly closed
valves in gaseous fluid piping.
In contrast, the inertia of the fluid column in a liquid pipeline is not
as easily overcome. Its relative incompressibility provides no such
cushion. The entire upstream fluid mass is decelerated at once by
the closing valve and the resulting pressure surge may be of suf-
ficient magnitude to cause structural damage.
An additional problem can occur downstream from the closing valve.
This may be described as fluid column rupture and involves the
inertia of the fluid column moving it away from the closed valve, with
the proximate space being occupied by a bubble of the fluid vapor
or, simply, a substantial vacuum. If there is sufficient back pressure
in the line, the fluid column reverses its velocity and closes the void
created by the fluid column rupture, causing another pressure surge
when it reaches the valve.
Pressure surge intensity is roughly proportional to the length and
velocity of the fluid column upstream of the closing valve and
inversely proportional to the time taken to close the valve. Fluid
column rupture and return surge intensity are proportional to the
same condition on the other side of the valve in addition to the back
pressure in that section of piping. Therefore, a slow closing is helpful
in limiting the magnitude of the pressure surge phenomena.
a
CAUTION: In large, long-distance liquid pipelines it is criti-
cally important to evaluate pressure surge possibilities and
to establish limits on the speed of closure of the flow shutoff
valves. In operating such valves or in setting the speed of
operation of power-actuated valves, design limits on speed
of closure should be conscientiously observed.
Rapid closure of a valve in any flowing liquid pipeline can cause a
substantial pressure surge that may manifest itself in a sharp bang
sound or possibly in a series of bangs, frequently referred to as
water hammer. This phenomenon can occur in any flowing liquid line
and is not limited to waterlines. Rapid closing of a shutoff valve in a
flowing liquid line should be avoided, especially during the last part
of the stem travel.
4.5 Noise
There are many different valve-operating conditions that can result
in noise. Such noise may be considered normal, given the nature of
the fluid, and the pressure, temperature, and velocity of flow. There
may be a wind noise in a flowing gas line. There may be clear or
hoarse whistling sounds resulting from the shape of the flow pas-
sage, including the flow path through a valve. Cavitating conditions
in a liquid line can cause a white noise, ranging from a whisper to a
sound like falling rocks and gravel, to a deafening roar. There may
also be mechanical noises as a result of movement of internal com-
ponents acted on by the flowing fluid. Some of these noises may be
relatively harmless insofar as system integrity and performance are
concerned. Mechanical damage in lines with compressible fluid is
generally limited to points of sonic or supersonic velocity, or where a
vortex resonance with an internal component causes movement and
wear or breakage.
Vortex resonance with an internal component may also cause
problems in liquid service. In addition, noise may be evidence of
cavitation, which may cause mechanical damage including mas-
sive erosion of the metal walls of a valve or pipe walls and/or other
internal components.
A full technical discussion of all of the sound-generating mecha-
nisms is beyond the scope of this manual. Nevertheless, it is recom-
mended that an evaluation be made of any condition of remarkable
noise in a piping system, at least to the point of understanding its
cause. If a valve is involved, a determination should be made as to
whether the valve is the source or merely the location of the noise.
Usually, if the valve is the source, the noise can be “tuned” by
slightly throttling the valve.
Mechanical or high-intensity fluid noise in the vicinity of a valve may
be a warning of potentially serious trouble. Expert assistance should