Flowserve 520si Digital Positioner User Manual
Page 9
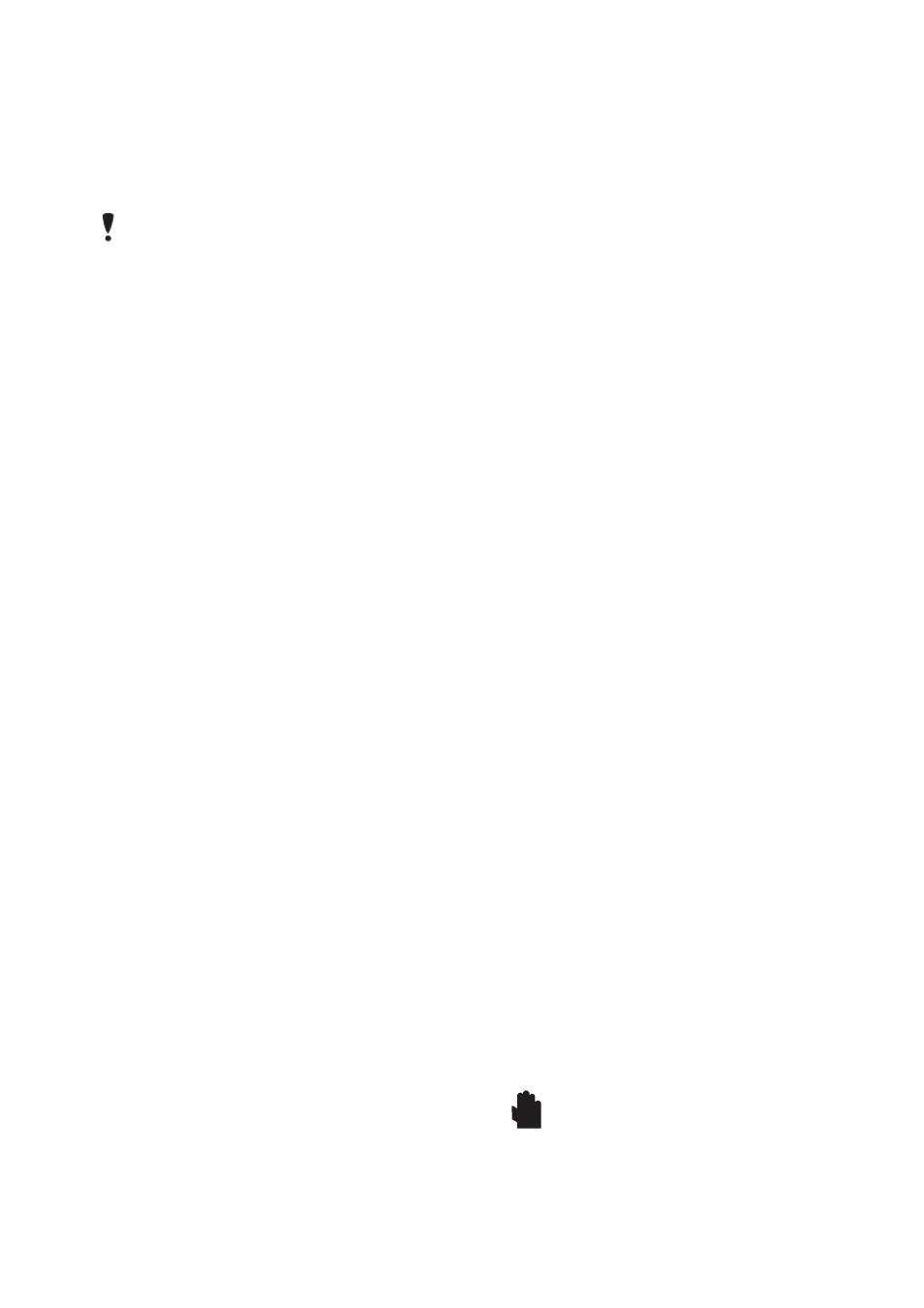
9
settings. For indication of operational status or alarm condi-
tions there are three LEDs on the local user interface.
Initial DIP Switch Setting
Before placing the unit in service, set the DIP switches in the
“Configuration” and “Cal” boxes to the desired control op-
tions.
NOTE:
The switch settings in the Configuration box
are activated only by pressing the Quick-Cal button or
by utilizing the stroke calibration features provided by
a handheld or by Flowserve PC software.
9.2 Operation of Configuration DIP Switches Setup
The first six DIP switches are for basic configuration
1. Air Action – Must be set to match the configuration of the
valve/actuator mechanical configuration.
ATO (air-to-open) – Select ATO if increasing output pres-
sure from the positioner is tubed so it will cause the valve
to open.
ATC (air-to-close) – Selecting ATC if increasing output
pressure from the positioner is tubed so it will cause the
valve to close.
2. Signal at Closed – Normally this will be set to 4 mA for an
air-to-open actuator, and 20 mA for an air-to-close actua-
tor configuration.
Selecting
4 mA will make the valve fully closed when the
signal is 4 mA and fully open when the signal is 20 mA.
Selecting
20 mA will make the valve fully closed when the
signal is 20 mA and fully open when the signal is 4 mA.
3. Pos. Characterization
Select
Linear if the actuator position should be directly
proportional to the input signal.
Select
Optional if another characteristic is desired, which
is set in conjunction with the next switch, labeled
Op-
tional Pos. Char.
4. Optional Pos. Char. – If the
Pos. Characterization switch
is set to optional, this switch is active with the following
options:
The
=% option will characterize the actuator
response to the input signal based on a standard 30:1
equal percent rangability curve.
If
Custom is selected, the positioner will be characterized
to a custom table that must be set-up using a properly
configured HART 275 handheld or other host software.
5. Auto Tune – This switch controls whether the positioner
will auto tune itself every time the Quick-Cal button is
pressed
On enables an auto tune feature that will automatically
determine the positioner gain settings every time a Quick-
Cal is performed based on the setting of the rotary
Gain
switch.
If the rotary
Gain selector switch is set to E with the
autotune switch
On, a Flowserve nominal
response tuning set will be calculated and used.
If the rotary
Gain selector switch is set to D, C, B, or A with
the
Auto Tune switch On, progressively lower gain set-
tings will be calculated and used.
If the rotary
Gain selector switch is set to F, G, or H with
the
Auto Tune switch On, progressively higher gain set-
tings will be calculated and used.
Off forces the positioner to use one of the factory preset
tuning sets determined by the rotary
Gain selector switch.
Settings
A through H are progressively higher gain
predefined tuning sets. The positioner is preset to Autotune
- On at the factory. This is the recomended setting.
6. Config. Switches — By selecting
Enabled, the Logix 520 si
will read all of the configuration switches each time a
Quick-Cal is performed to determine the configuration.
Selecting
Disabled retains the last configuration in memory
(from the last successful calibration) before the switch
was set to
Disabled. With this setting a Quick-Cal only
zeros and spans the positioner.
9.3
Calibration switches
9.3.1
Stability Switch – This switch adjusts the position
control algorithm of the positioner for use with low
friction control valves or high friction automated
valves.
•
Placing the switch to the left optimizes the response
for low friction, high performance control valves.
This setting provides for optimum response times
when used with most low friction control valves.
•
Placing the switch to the right optimizes the response
for valves and actuators with high friction levels. This
setting slightly slows the response and will normally
stop limit cycling that can occur on high friction
valves.
9.3.2 Setup of the Cal DIP Switch for the Quick
Calibration operating mode
•
Select
Auto if the valve/actuator assembly has an
internal stop in the 100% stroke position. In
Auto
mode the positioner will fully close the valve and
register the 0% position and then open the valve to
the stop to register the 100% position when perform-
ing a self-calibration. See detailed instructions in the
next section on how to perform an auto positioner
calibration.
•
Select
Jog if the valve/actuator assembly has no
calibration stop in the open position. In the
Jog mode
the positioner will fully close the valve for the 0%
position and then wait for the user to set the open
position using the
Jog buttons labeled with the up and
down arrows. See the detailed instructions in the next
section on how to perform a manual calibration using
the
Jog buttons.
WARNING:
During the Quick-Cal operation the valve
may stroke unexpectedly. Notify proper personnel
that the valve will stroke, and make sure the valve is
properly isolated.
Quick-Cal Operation
The
Quick-Cal button is used to locally initiate a calibration of
the positioner. Pressing and holding the
Quick-Cal button for
STOP!