Flowserve 1878 Y-Pattern Globe Valves User Manual
Page 12
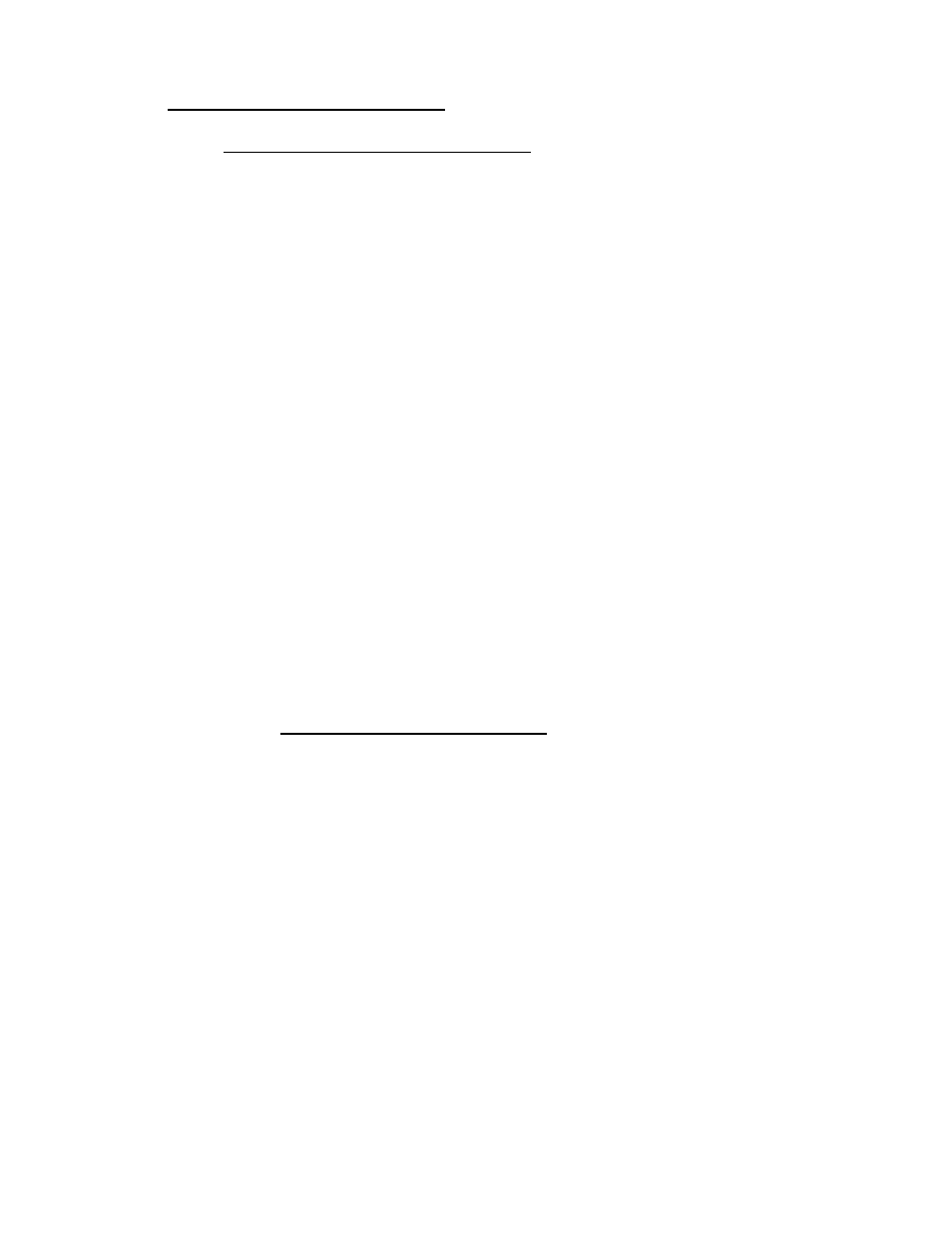
9.0
MAINTENANCE INSTRUCTIONS (Continued)
9.3
REFINISHING SEALING SURFACES
Minor discontinuities in the seat sealing surface, which may cause leakage,
can, in many cases, be removed by lapping. Major defects such as cracks
or deep gouges will generally require replacement of the part.
Minor
discontinuities
on
the
valve
disc sealing surface may be removed by
re-machining the surface to remove a few thousandths of material. Major
defects will generally require replacement of the disc.
NOTE: Lapping is a polishing process where a sealing surface is
ground with an abrasive held in place by a special fixture. The
abrasive is commonly found in paste form or bonded to a
paper backing. Detailed instructions on the use of lapping
abrasives and fixtures, normally supplied with such
equipment, should be adhered to.
In order to maintain seat tightness in globe valves, the sealing surface
angles on both the disc and seat ring must be kept within close tolerance
(30
° [+1/2°] for the seat and 29° [-1/2°] for the disc). It is important when
lapping to use fixtures that will maintain these angles. Flowserve does not
recommend lapping the disc directly to the seat. A good seal is dependent
on line contact. Direct contact lapping will result in excessive seat widths.
9.3.1 Globe Valve Seat Lapping Tool
Lapping tools and tool drivers for the Series 1878 globe valve seats
are available thru Flowserve Corporation. Contact your nearest
Flowserve Representative for information.
To lap the seat ring, simply apply two (2) to five (5) lbs of force to the
tool as it grinds. Three (3) or four (4) two (2) second cycles should be
sufficient. Visually check the seat ring surface for a fine line blue dye
check with the disc should assure tight sealing. Flowserve
recommends that the disc be turned in a lathe with 16 rms finish at
29º [-1/2
°]
12