0 installation instructions, 0 maintenance requirements – Flowserve 1878 Swing Check Valve User Manual
Page 5
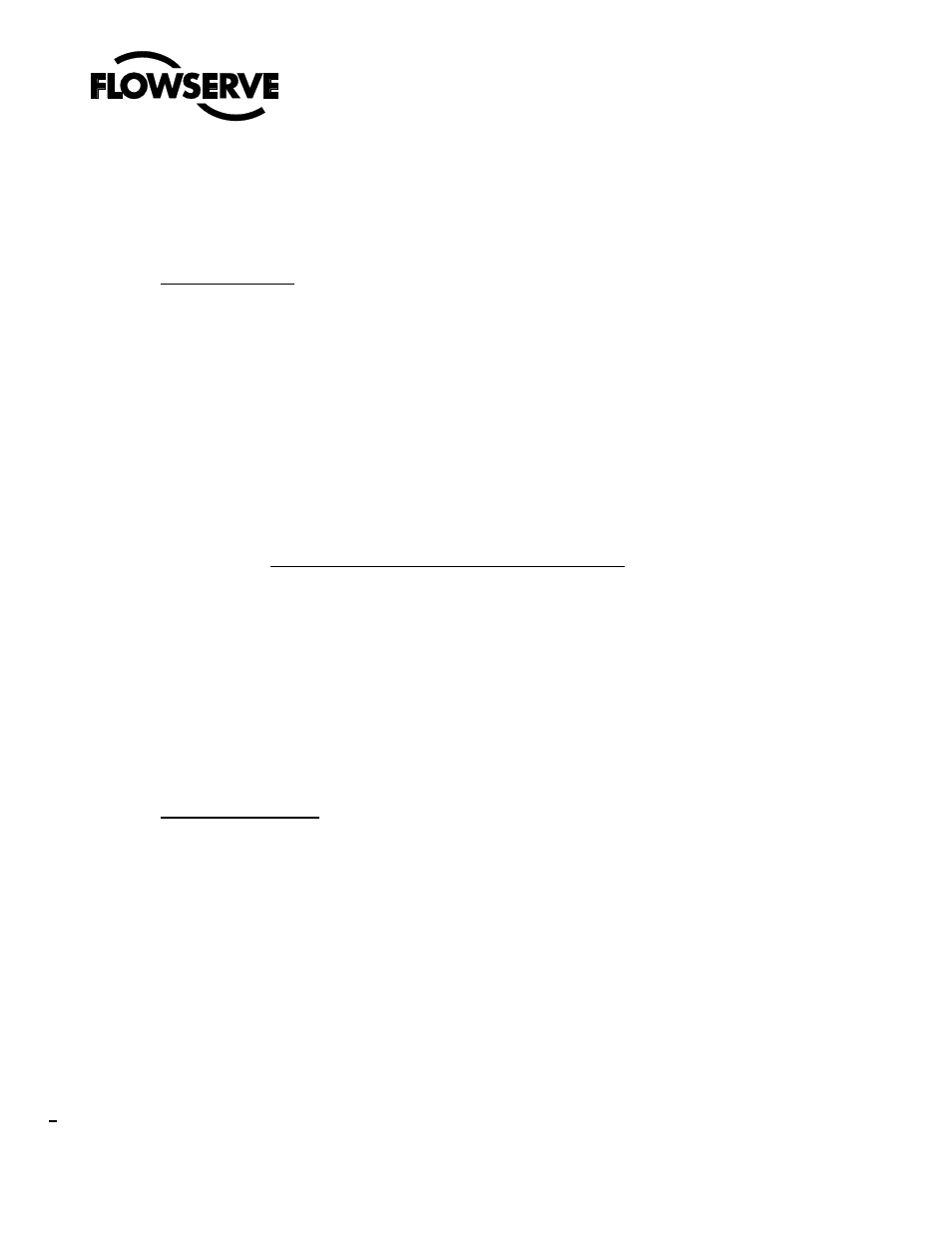
1878 Swing Check Valves FCD ADENIM0006-00
5
6.0 Installation Instructions
(Continued)
6.1.2
Remove the end covers.
6.1.3
Remove blocks or heavy paper used to hold check valve discs open during shipping.
6.2
Assembly Instructions
6.2.1
Although the valves have been shipped in a clean condition, prior to installing the valves, examine the lines
and the valve ports for foreign matter and clean them thoroughly if they have been exposed to the elements.
(BEFORE CLEANING IN THIS FASHION, CHECK AT THE SITE TO SEE IF A SPECIFIC CLEANING
PROCEDURE SHOULD BE FOLLOWED.) Open the valves fully and flush them out with water if possible;
otherwise blow them out with air or steam.
6.2.2
Ensure that there is no line sag at the point of installation. Eliminate any pipeline deviation by the proper use of
pipeline hangers or similar device.
6.2.3
Extreme caution should be taken when installing check valves. The arrow on the valve body indicates flow
direction. Note that the disc swing is upward and away from the inlet end of the valve. Therefore, when
installing a check valve, place it so that the flow of the incoming fluid will open the valve and return flow will
close it. Check valves installed in reverse position will stop the flow in the normal flow direction. Check valves
installed in horizontal piping shall have the hinge pin in a horizontal plane with the bonnet on top. Check
valves installed in vertical piping shall have the hinge pin in a horizontal plane with flow upward.
6.2.4
The valves should then be blocked or slung into position with apparatus that is sufficient to hold the valve
assembly weight while the valve is being welded into the line. Care should be taken during welding that
foreign material or dirt does not enter the valve and cause interference with subsequent operation. For valves
with resilient seats - caution should be exercised so that the resilient seat material is not subjected to
temperatures greater than 400
°
F.
7.0 Maintenance Requirements
7.1
Preventative Maintenance
7.1.1
Check all nuts and bolts periodically to ensure tightness and to forestall possible leaks. Refer to section 11.0
for bolting torque valves.