Worcester controls – Flowserve Worcester Controls Miser Ball Valves User Manual
Page 4
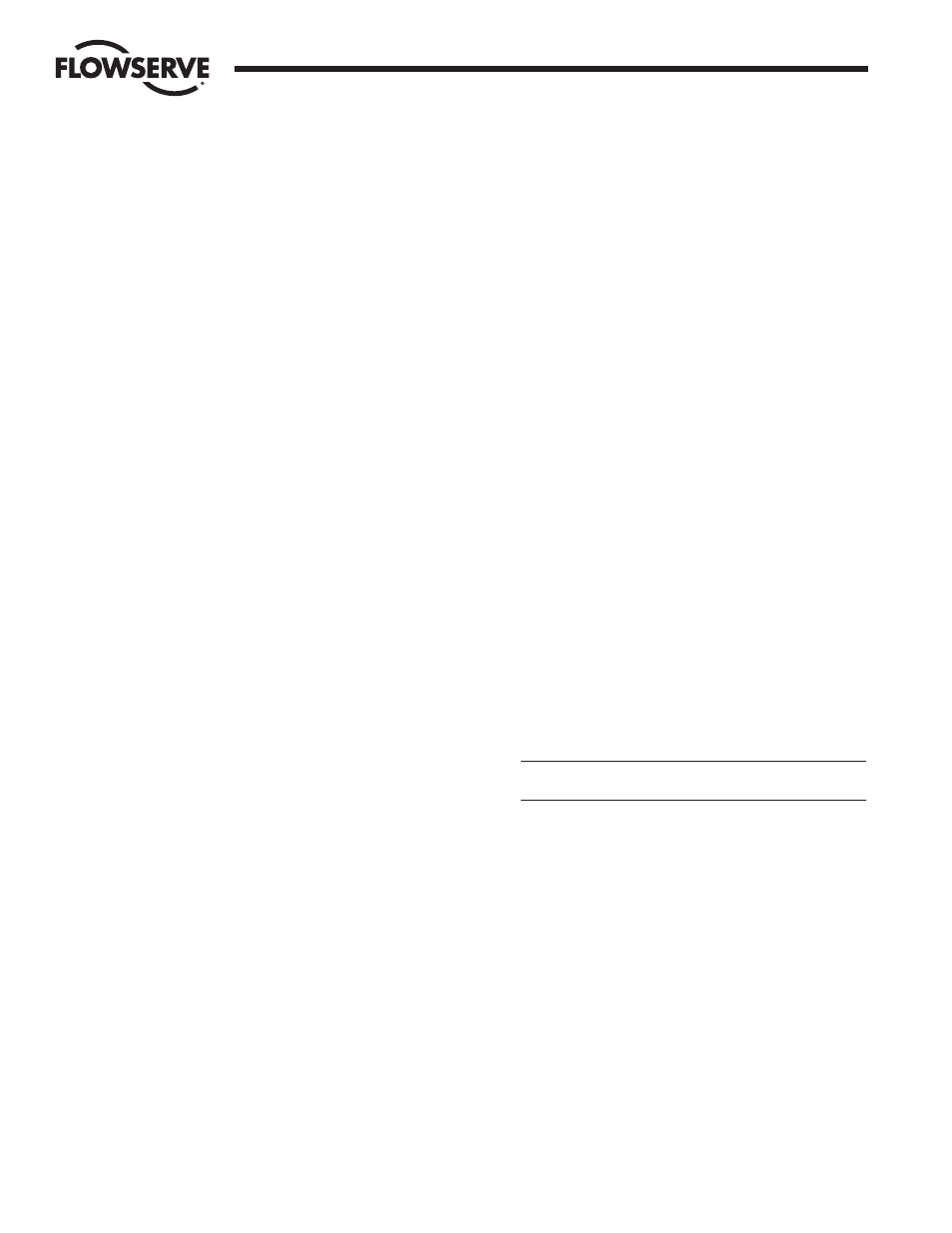
Flow Control Division
Worcester Controls
4
Miser Ball Valves
WCAIM2030
NOTE: The ball and the surfaces against which the seats and
seals are installed should be undamaged, clean and free of pit
marks and scratches. Light marring from the action of the ball
against the seats is normal and will not affect the operation of
the valve. Flaws which can be seen but barely detected with
fingertips are acceptable. The stem and body surfaces that the
thrust bearing(s) and stem seal(s) contact must be
undamaged, clean, and free of pit marks and scratches.
g. Lightly lubricate the ball, seats, body seals, stem seal(s), stem
seal protector and seat back seals (if any), and thrust
bearing(s) with a lubricant compatible with the media being
handled, except for valves with V20, V33 or V38 options,
which are assembled dry. White petroleum jelly is a good
general-purpose lubricant.
For valve repair kits with “A” or “G” seats, the filled metal
seats will be lubricated at the factory. If they are not, they
should be lubricated as noted in Paragraph B.5. and also as
stated above. Do not operate a newly rebuilt valve using filled
metal seats without lubricants. The seat back seals will be
pre-assembled to the seat backs.
For CL44, and oxygen prepared (prefix code “X”) valves only,
lightly lubricate the ball, seats/body seals, stem seal and
thrust bearing with a PTFE-based lubricant as Fluorolube S-30
or equivalent.
h. For stem area rebuilding, refer to exploded view, stem build
illustrations and stem component color chart on the following
pages that pertain to the type valve being rebuilt.
Order of Assembly:
Place new thrust bearing(s) on stem and insert assembly
through body cavity. Place new stem seal(s), stem seal
protector (if any), and the follower in position. PEEK thrust
bearing and stem seal protectors are placed outside of seals
and bearings. The seals/bearings must contact the body.
NOTE: For valves having graphite stem seal(s), care must be
taken when installing the graphite parts because they are
easily damaged by squeezing the O.D. of the seals. Handle
gently by holding seal(s) on flat surfaces rather than on the
O.D. If resistance is encountered when installing seal(s) over
the stem, use follower to gently push the stem seal(s) down.
Stem seals, stem seal protectors and thrust bearings that are
the same size and color are interchangeable.
i
Place two new Belleville washers in position with the larger
diameter sides touching each other.
For those valves with single self-locking stem nut, place four
new Belleville washers in position (two pairs of washers with
larger diameter sides touching each other).
j.
Place retaining or self-locking stem nut on stem and using
handle or a wrench to prevent rotation, tighten nut to make
snug and firm. Follow Section C, Maintenance, for proper
stem adjustment.
k. Replace separate stop and handle or one-piece handle and stop
(if manual valve), lockwasher and handle nut on stem. (This
step is not applicable to valves with self-locking stem nut.)
l.
With valve in closed position (stem flats going across
pipeline), replace ball (see note below), one-piece (three-way)
seat/body seal (if used), or seats and seat back seals (if any).
With valve in open position, carefully insert new body seals
and place center section between pipe ends. For AF44 and
FZ44 fire valves, insert centering rings, if any, into pipe ends
before installing center section of valve. For valves with
coated stainless steel “S”gaskets, install with wide flange
facing body (see view A-A on page 5). For valves with “A” or
“G” seats, before putting the center section back between the
pipe ends make sure that the seat back seal is located on the
seat correctly. If it is not, it could be damaged or cause the
valve to leak.
NOTE: For diverter and three-way valves, install ball as
follows:
V1(90° valves)– with handle and/or stem flats in line with
body main axis, viewed from bolt head side (normally
upstream) one ball port is to the right, one is down, and one
is on opposite end of valve.
V2(180° valves)- Using some convention as V1, one ball port
is down and the other is on opposite end of valve.
Valves with a pressure relief hole in the ball (V3 option and
chlorine valves) must be assembled and installed with the
hole upstream when the valve is closed, to insure that cavity
relief is upstream. Any valve with a relief hole will have an
arrow on the body pointing downstream. This arrow is
tamped on the body or on a metal tag welded to the body.
Replace and tighten body bolts and nuts per torque figures
and method found in Section A.2.e.
CAUTION: Do not scratch body seals when replacing valve
body.
When ordering parts, please provide the part name and the
following information as found on the valve body, stop plate,
handle, valve nameplate, or mounting bracket nameplate:
1. Valve Size, Style and Revision Number – Example:
1
/
2
"
4466T SE RO STEM
2. Valve Size, Style and Five-Character Code, known as a
“P”, “T”, “C”, or similar number, the designation for a
non-standard product. – Example:
3
/
4
" 4446RT SW T0726
BALL
3. Porting (if a diverter or three-way valve) must also be
specified when ordering these parts. Example: 1" D4466 T
SE V1 R8 BALL
The terminology shown in the exploded view Parts Listing
on next page is standard.