4 seal installation – Flowserve Circpac HP User Manual
Page 4
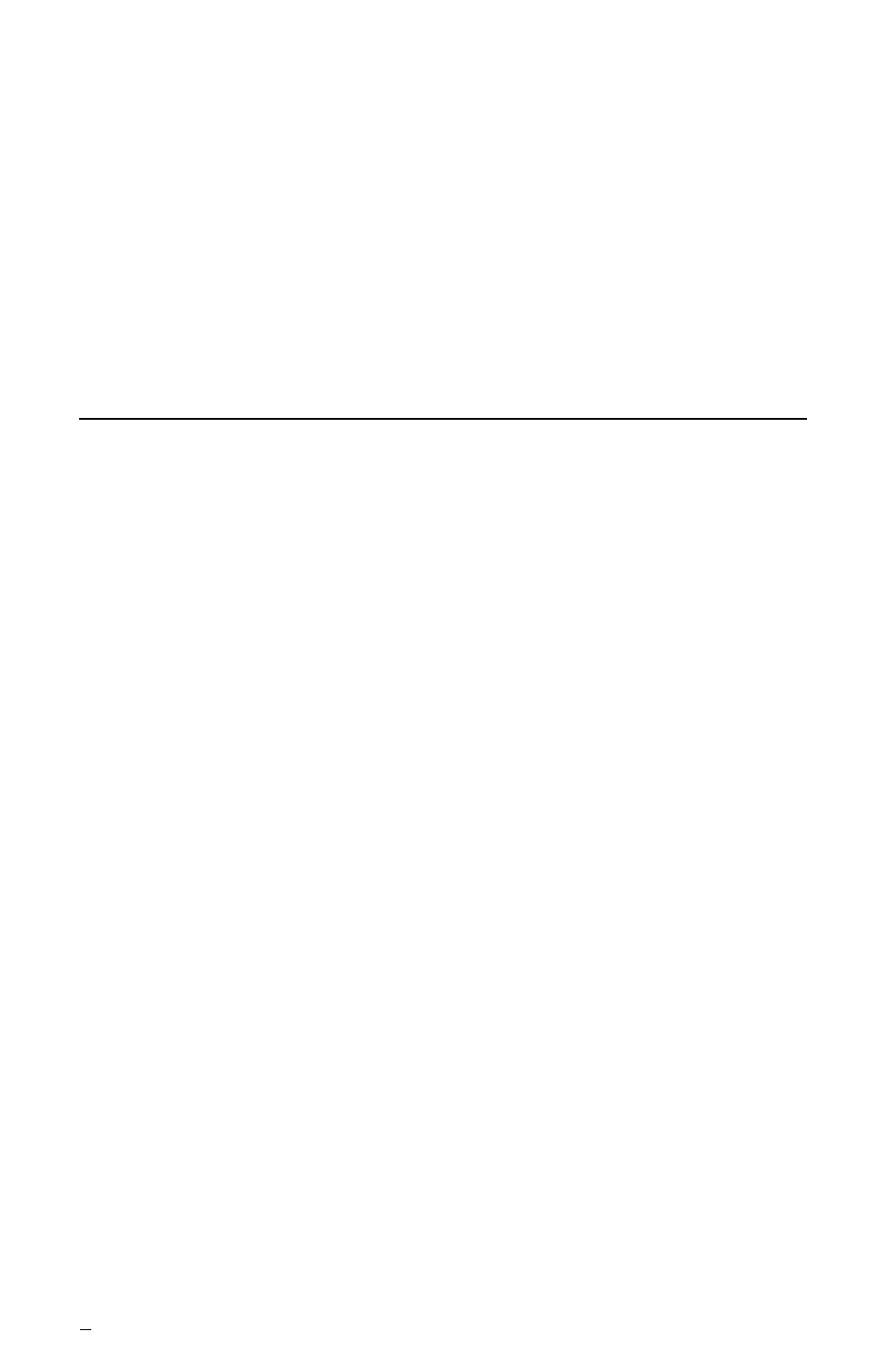
3.11 Seal chamber squareness to the shaft center line should be within
0.013 mm per 25.4 mm (0.0005 inch per 1 inch) shaft diameter.
Note: Make sure that shaft end play does not affect the reading.
3.12 Concentricity of the shaft to the seal chamber bore should be within
0.025 mm per 25.4 mm (0.001 inch per 1 inch) shaft diameter to a
maximum of 0.13 mm (0.005 inch) TIR.
3.13 Break all sharp corners on shaft steps, threads, reliefs, shoulders, key
ways, port holes, etc. across which gasket(s) must pass and /or seal
against.
4 Seal Installation
4.1 Review Circpac HP assembly drawing and seal assembly instructions
prior to installation. Particularly follow special instructions listed on the
assembly drawing.
4.2 Apply a thin coat of lubricant to all gaskets. The lubricant must be
compatible with both the product and gasket materials. Generally,
silicon grease is suitable.
4.3 If the Circpac HP does not have a cartridge sleeve, verify that the
segmented rings are centered in the seal housing. Some sleeveless
assemblies provide a guide plug that centers the rings and aligns with
the shaft. Pay extra attention to cleaning the shaft.
4.4 Orient the ports on the seal housing(s) as indicated by the seal
assembly drawing and connection piping. Line up the seal housing(s)
bolt holes with those on the machine.
4.5 Slowly and carefully slide the seal along the shaft while maintaining
tight parallelism between the shaft and seal bore until located against
the face of the seal chamber. If a guide plug is used, allow the plug
to be displaced by the shaft. If the equipment manufacturer provides
installation tools, use these per the instructions.
4.6 Evenly torque gland bolts/nuts to prevent cocking of the gland or
uneven gland pressure against the seal chamber. For sleeved
designs, do not fasten drive arrangement.
4.7 Complete the remaining equipment assembly including bearings,
if applicable.
4.8 Ensure the setting plates are correctly located and engaged.
4.9 For sleeved designs, fasten drive arrangement to the setting values
shown on the seal assembly drawing, making sure the shaft is in the
same position as when the equipment is operating.
4