3lubrication instructions, 4repair instructions – Flowserve XLC Series User Manual
Page 7
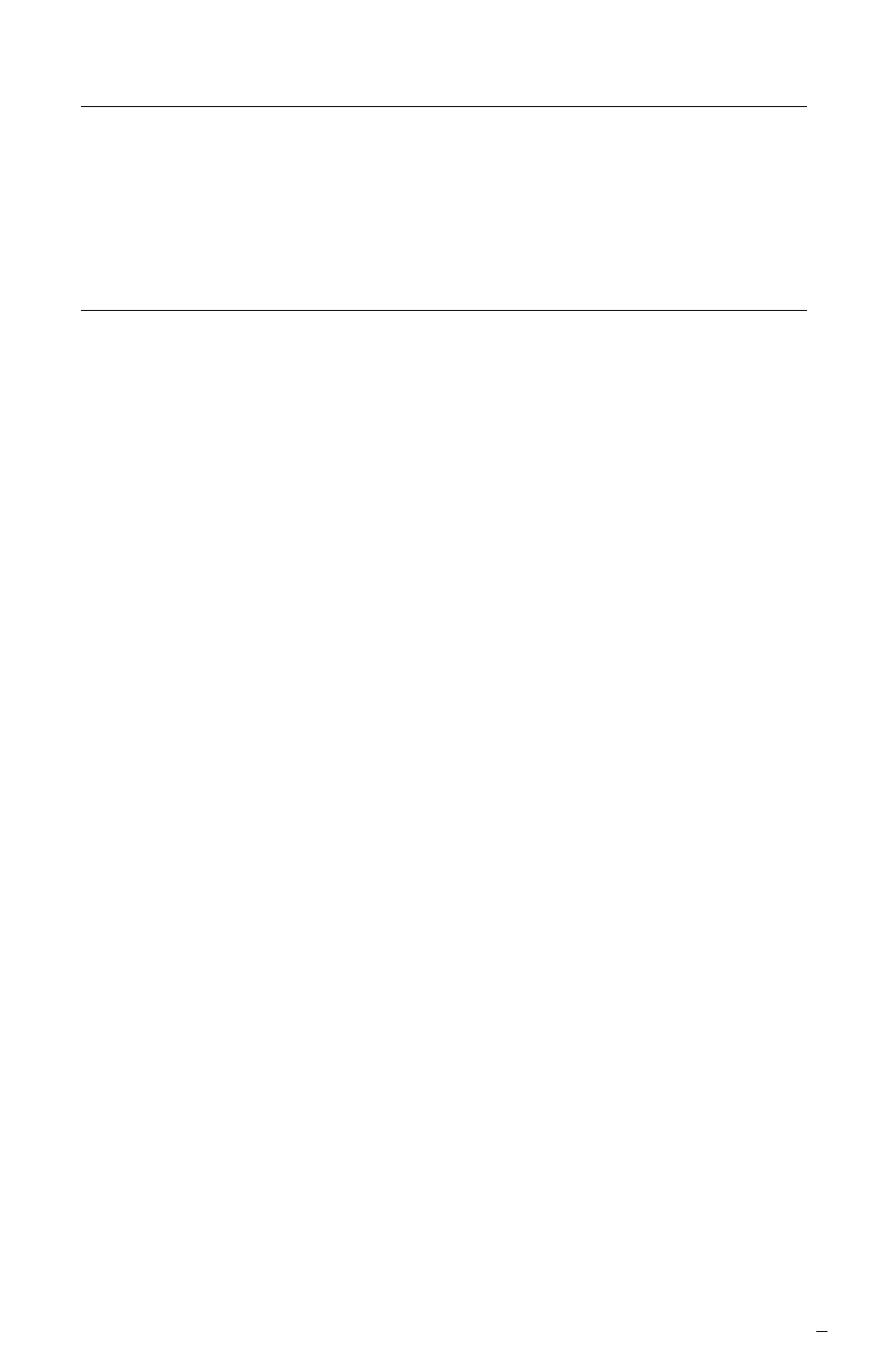
7
3
Lubrication Instructions
3.1 Before initial startup the bearing should be flooded with grease until
grease is observed escaping from the bearing.
3.2 Additional lubrication (five pumps from a standard grease gun) should be
added to the bearing at monthly intervals through the lubrication line.
4
Repair Instructions
This product is a precision radial load support device. The design and dimension
tolerances are critical to performance. Only parts supplied by Flowserve should
be used to repair an XLC bearing. These are available from numerous Flowserve
stocking locations. To order replacement parts, refer to the part code number and
B/M number. A repair kit should be stocked to reduce repair time.
4.1 Five (5) components in the XLC Bearing are to be replaced during
servicing: WR-600 insert, (2) wiper jackets, and (2) ball and socket
O-rings. Other components are reusable but should be inspected for
damage.
4.2 Disassembly of the bearing is the reverse of assembly.
4.3 The WR-600 insert is held in place by eight (8) screws, four (4) in each
half. Remove these screws and separate the bearing insert from the
bearing carrier.
4.4 Identify the half of the new bearing insert with the grease port and place it
in the matching bearing carrier half so the ports in each piece are aligned.
Torque screws to 1.7 N-m (15 in-lbs).
4.5 Repeat 4.4 with the halves that do not contain the grease port.
4.6 Inspect and resurface/replace shaft and/or sleeve before reassembly.
When repairs are not conducted at the customer’s location, decontaminate the
bearing assembly and return it to Flowserve, with an order marked “Repair or
Replace.” A signed certificate of decontamination must be attached. A Mate-
rial Safety Data Sheet (MSDS) must be enclosed for any product that came in
contact with the bearing. The bearing assembly will be inspected and, if repair-
able, it will be rebuilt and returned in its original condition.