Dukane – Dukane Ducane INtelligent Assembly Solutions AN200 User Manual
Page 2
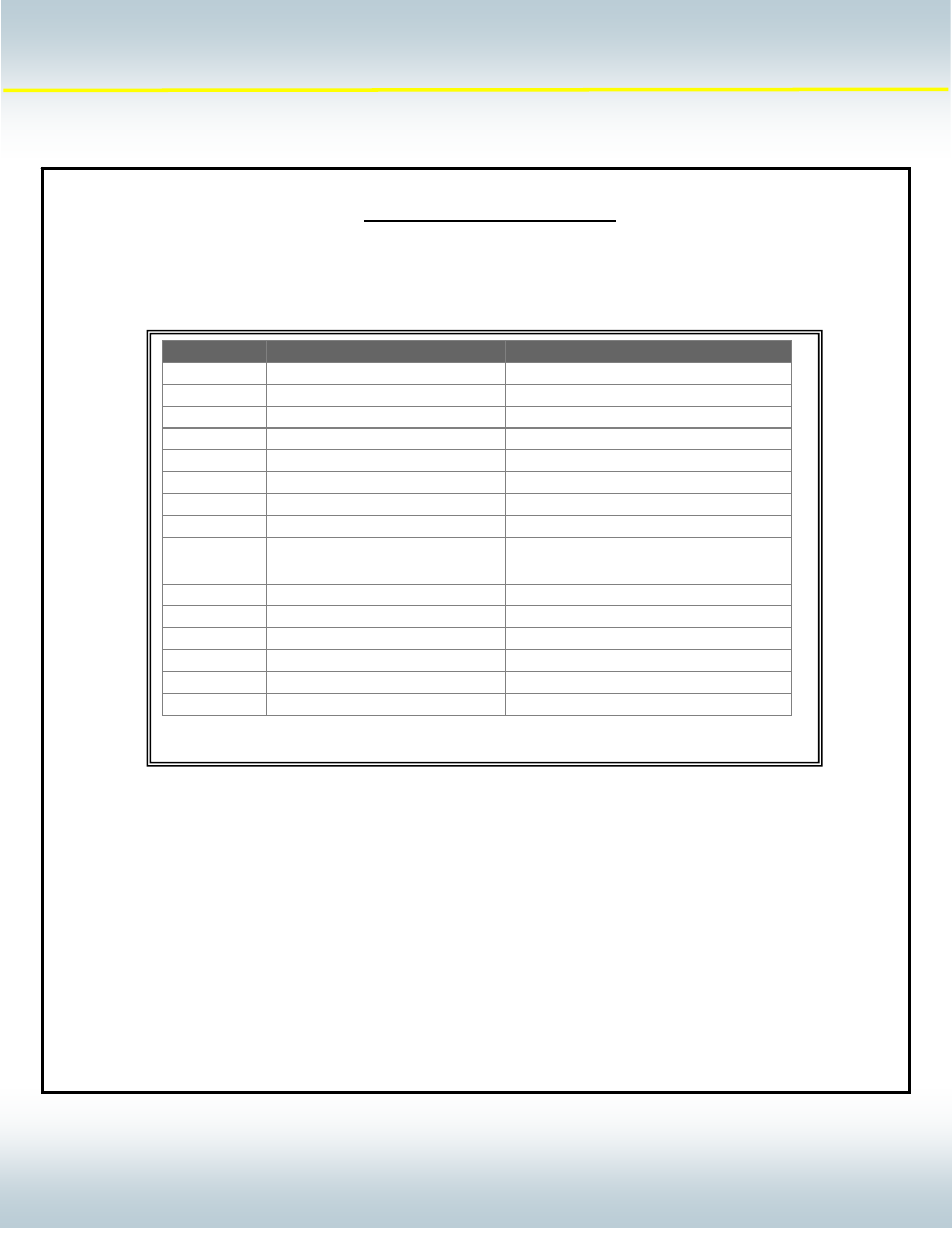
-
2
-
22102
DUKANE
A
A
p
p
p
p
l
l
i
i
c
c
a
a
t
t
i
i
o
o
n
n
N
N
o
o
t
t
e
e
AN200
Rev 01
© Dukane Corporation 2003. All rights reserved.
Dukane Corporation
2900 Dukane Drive Saint Charles, IL 60174 USA
Phone (630) 797-4900 FAX (630) 797-4949
http://www.dukane.com/us
Intelligent Assembly Solutions
2
1
System Input Connector
The System In interface connector is one of the primary communications links between the DPC II / II+ input port and
the user automation equipment. This connector provides the automation with dedicated communication lines that
allow the automation to control the beginning and the end of a welding sequence.
Pin Number
DPC Signal Name
DPC Signal Type
1 Power
Supply
+22 VDC (250 mA max)
2
Ground
22VDC Return
3 Isolated
Operate Input
Input
4 Isolated
Input Common
1
Common for pin 3, 5, 9
5
Isolated Press Control
2
Input
6
Not Used
Not Used
7 Ground
+22VDC
Return
8
Non Isolated Operate Input
9
Isolated Automation Stop /
Automation End of Weld
3
Input
10
Not Used
Not Used
11
Hand Probe Press Inhibit
Input
12 MPC
Probe/Setup Bit 0
4
Input
13 MPC
Probe/Setup Bit 1
4
Input
14 MPC
Probe/Setup Bit 2
4
Input
15
Front Panel Control Lock
Input
Notes:
1. SH707 on the 110-3606 system I/O PCB must be configured to the JU728 position when this
common is used.
2. This input requires the optional 110-3938 press control module. Configuration of the SH901
Jumper on the 110-3938 press control module may also be required.
3. This input is configured for use as Automation End of Weld at the factory. Jumper SH704 must
be reconfigured on the 110-3606 System I/O board to permit use of the Isolated Automation
Stop feature.
4. The MPC probe bit functionality requires the optional MPC feature. The Setup bit functionality
is available on all DPC II+ systems. Please refer to the DPC manual for further details on this
feature.