Chemical compatibility chart – Scilogex Unoverse Peristaltic Pump Dispense 9100 User Manual
Page 2
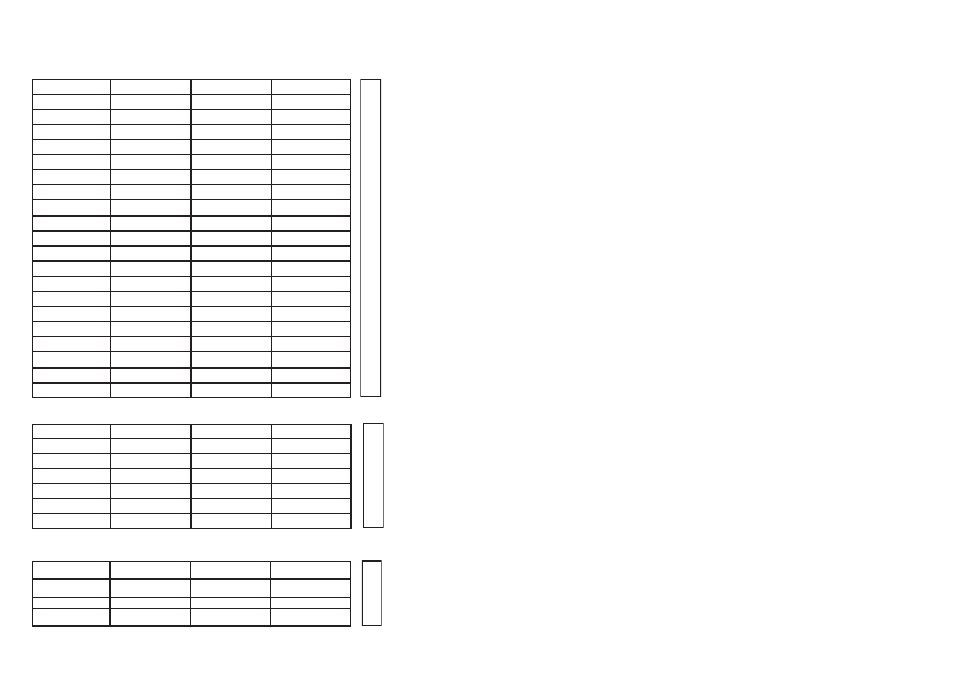
Page 9
13. FAQ
1.
Q. Why does the pump stalls or runs slower than expected when new
tubing is installed?
A. A new Santoprene tube is stiff when new so has to be shaped for some time
before it gains it’s elasticity. Run the pump in continuous mode for a total of
approx 5 minutes with the clamp lever half open to start with, gradually moving
the clamp lever to fully closed position.
2.
Q. What is the life of the tube?
A. The life of a peristaltic tube depends on many variants such as
speed, the reagent it is pumping and temperature. In general you should
expect approximately 800 hours operation from one tube.
3.
Q. Why does the displayed value sometime ‘jump’ in double
figures?
A. This happens when dispensing small volumes with the ID2.0mm
tubing. Following the calibration procedure the instrument’s
mathematical calculation divides the volume to be dispensed by the
number of pulses received from the motor’s encoder and stores this
value. If the volume per rotor rotation is relatively large, the ratio of
pulses to volume is coarse. In these circumstances the required volume
input does not divide into stored values, and therefore the calculator will
round up or down to the nearest whole figure. Whenever you use the
ID1.0mm tube, the dispensed volume per rotor rotation is small enough
to allow single μl per displayed digit.
4.
Q. Can I leave the unit switched ‘ON’ throughout the day?
A. Yes, you can. The dispenser requires very little energy when the
pump is not running so continuous power into the unit will not harm it.
5.
Q. Why can’t I set slower dispense speed ?
A. The motor’s speed is controlled via the voltage supply to the motor.
Too low voltage and the pump’s motor will stall, in particular when the
tubing is new and the resulting load on the motor is higher.
6.
Q. Can I dispense hot reagents using the dispenser?
A. Yes, the dispenser to works safely with media temperatures of up to
100°C. Be aware that the internal electronics could be damaged by any
ingress of fluids or steam vapours.
Acetaldehyde
Chloroacetic acid
Linseed Oil
Potassium salts
Acetic acid
Chronic acid
Magnesium salt
Silver salts
Acetic Anhydride
Chromium salts
Maleic acid
Soap solutions
Acrylonitrile
Copper salts
Manganese salts
Sodium salts
Aluminum Chloride
Ethylene glycol
Mercury salts
Sodium hydroxide
Aluminum sulfate
Ferric salts
Methanol
Sodium hypochlorite
Ammonia
Fluoborate salts
Natural gas
Stearic acid
Ammonium salts
Fluoboric acid
Nickel salts
Sulfur dioxide
Ammonium hydrox-
ide
Fluosilicic acid
Nitric acid-10%
Sulfuric acid, dil.
Amyl acetate
Formaldehyde
Nitroethane
Sulfurous acid
Antimony salts
Formamide
Nitrogen oxides
Tannic acid
Arsenic salts
Formic acid
Nitrous acid
Tanning extracts
Barium salts
Glucose
Oils, animal
Trisodium phosphate
Benzoic acid
Glycerins
Oils. mineral
Urea
Bleaching liquor
Hydrochloric acid
Oils. vegetable
Uric acid
Boric acid
Hydrocyanic acid
Oxalic acid
Water
Bromine
Hydrogen peroxide
Oxygen
Water (brine)
Butyric acid
Hydrogen sulfide
Phosphoric acid
Water (stoam)
Calcium salts
Iodine and solutions
Phthalic acid
Zinc salts
Carbon Dioxide
Lactic acid
Phosphoric acid
Chlorine (wet/dry)
Lead salts
Plating solutions
Acetates
Butane
Me Et Ketone
Skydrol 500-B4
Acetone
Butanol
Nitric acid-30%
Sulfuric acid-90%
Alcohols
Essential Oils
Nitrobenzene
Tetrahydrofuran
Amyl alcohol
Ethers
Oleic acid
Turpentine
Aniline
Ethanol
Phenol
Benzaldehyde
Furfural
Propanol
Benzyl alcohol
Lithium grease
Pyridine
Benzene
Cyclohexane
Kerosene
Nitric acid- 70%
Carbon tetrachloride
Ethyl chloride
Trichloroethylene
Perchloroethylene
Chlorobenzene
Freon
Lacquer
Toluene
Chloroform
Gasoline, unleaded
Naphtha
Xylene
Little
or n
o
effe
ct on S
a
topre
n
e
Sev
e
re
Moderat
e effe
ct
Chemical compatibility chart