3 improper operation, 1 intended use, Improper operation – Richter KKP/FU Series Ball Valves (ISO/DIN) User Manual
Page 6: The directive 94/9/ ec (atex 95), Intended use, Series kk/f, kkp/f, kk/fu, kkp/fu
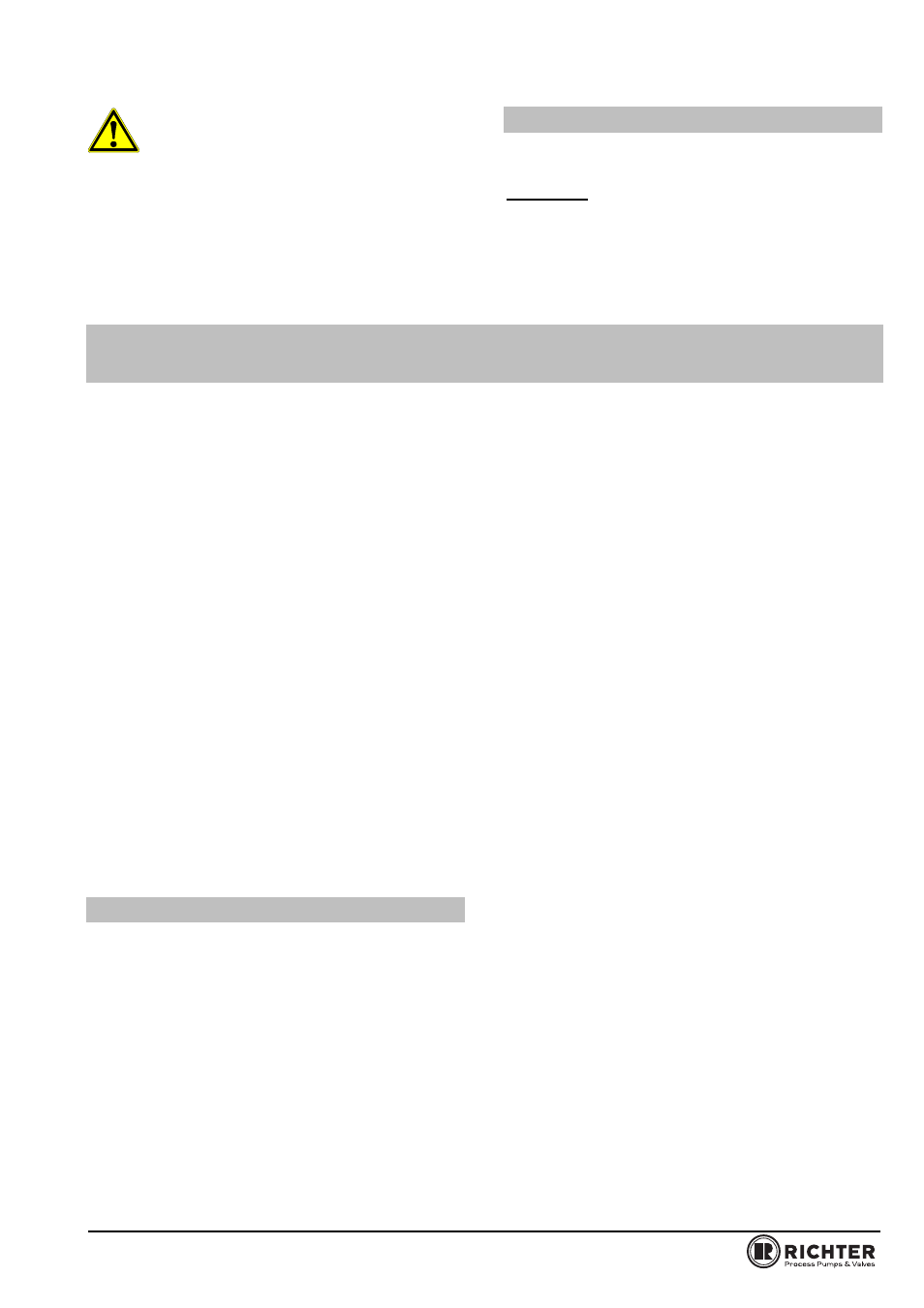
Series KK/F, KKP/F, KK/FU, KKP/FU
Page 6
9520-060-en
Revision 02
TM 7692
Edition 11/2009
Ball valves which are used as end valves
must be sealed with a blind flange at the free
connection end or appropriately secured
against unauthorised activation.
Fire protection to DIN EN ISO 10497 is not possible
(plastic lining and plastic components).
2.3 Improper operation
The operational reliability of the valve supplied is only
guaranteed if it is used properly in accordance with
Section 2.1 of this operating manual.
The operation limits specified on the identification
plate and in the pressure-temperature diagram must
under no circumstances be exceeded.
3
Safety notes for applications in potentially explosive areas
based on the Directive 94/9/ EC (Atex 95)
The valves are intended for use in a potentially
explosive area and are therefore subject to the
conformity assessment procedure of the directive
94/9/EC (ATEX).
As part of this conformity assessment, an ignition
hazard analysis to EN 13463-1 to satisfy the
fundamental safety and health requirements was
conducted with the following result:
The valves do not have any ignition source of
their own and can be operated both manually
as well as mechanically/electrically.
The valves are not covered by the scope of
application of the ATEX directive and therefore
do not need to be identified accordingly.
The valves may be used in a potentially
explosive area.
Supplementary notes:
Electric/mechanical
actuators
must
be
subjected to their own conformity assessment
to ATEX.
It is imperative to observe the individual points of
intended use for application in a potentially explosive
area.
3.1 Intended use
Improper operation, even for brief periods, may result
in serious damage to the unit.
In connection with explosion protection, potential
sources of ignition (overheating, electrostatic and
induced charges, mechanical and electric sparks) may
result from these improper operation; their occurrence
can only be prevented by adhering to the intended
use.
Furthermore, reference is made in this connection to
the Directive 95/C332/06 (ATEX 118a) which contains
the minimum regulations for improving the occupa-
tional health and safety of the workers who may be at
risk from an explosive atmosphere.
A difference is made between two cases for the use of
chargeable liquids (conductivity <10
-8
S/m):
1. Chargeable liquid and non-conductive
lining
Charges can occur on the lining surface. As a
result, this can produce discharges inside the
valve. However, these discharges cannot cause
ignitions if the valve is completely filled with me-
dium.
If the valve is not completely filled with medium,
e.g. during evacuation and filling, the formation of
an explosive atmosphere must be prevented, e.g.
by superimposing a layer of nitrogen.
It is recommended to wait 1 hour before removing
the valve from the plant in order to permit the
elimination of static peak charges.
This means that, to safely prevent ignitions, the
valve must be completely filled with medium at all
times or else a potentially explosive atmosphere
must be excluded by superimposing a layer of inert
gas.
2. Chargeable liquid and conductive lining
No hazardous charges can occur as charges are
discharged direct via the lining and shell (surface
resistance
<10
9
Ohm, leakage resistance
<10
6
Ohm).
Static discharges of non-conductive linings are
only produced through the interaction with a
non-conductive medium and are therefore the
responsibility of the plant operator.
Static discharges are not sources of ignition
which stem from the valves themselves!
The temperature of the medium must not exceed
the temperature of the corresponding temperature
class or the maximum admissible medium
temperature as per the operating manual.
If the valve is heated (e.g. heating jacket), it must
be ensured that the temperature classes pre-
scribed in the Annex are observed.
To achieve safe and reliable operation, it must be
ensured in inspections at regular intervals that the
unit is properly serviced and kept in technically
perfect order.