Troubleshooting – MK Diamond MK-MANTA IV User Manual
Page 9
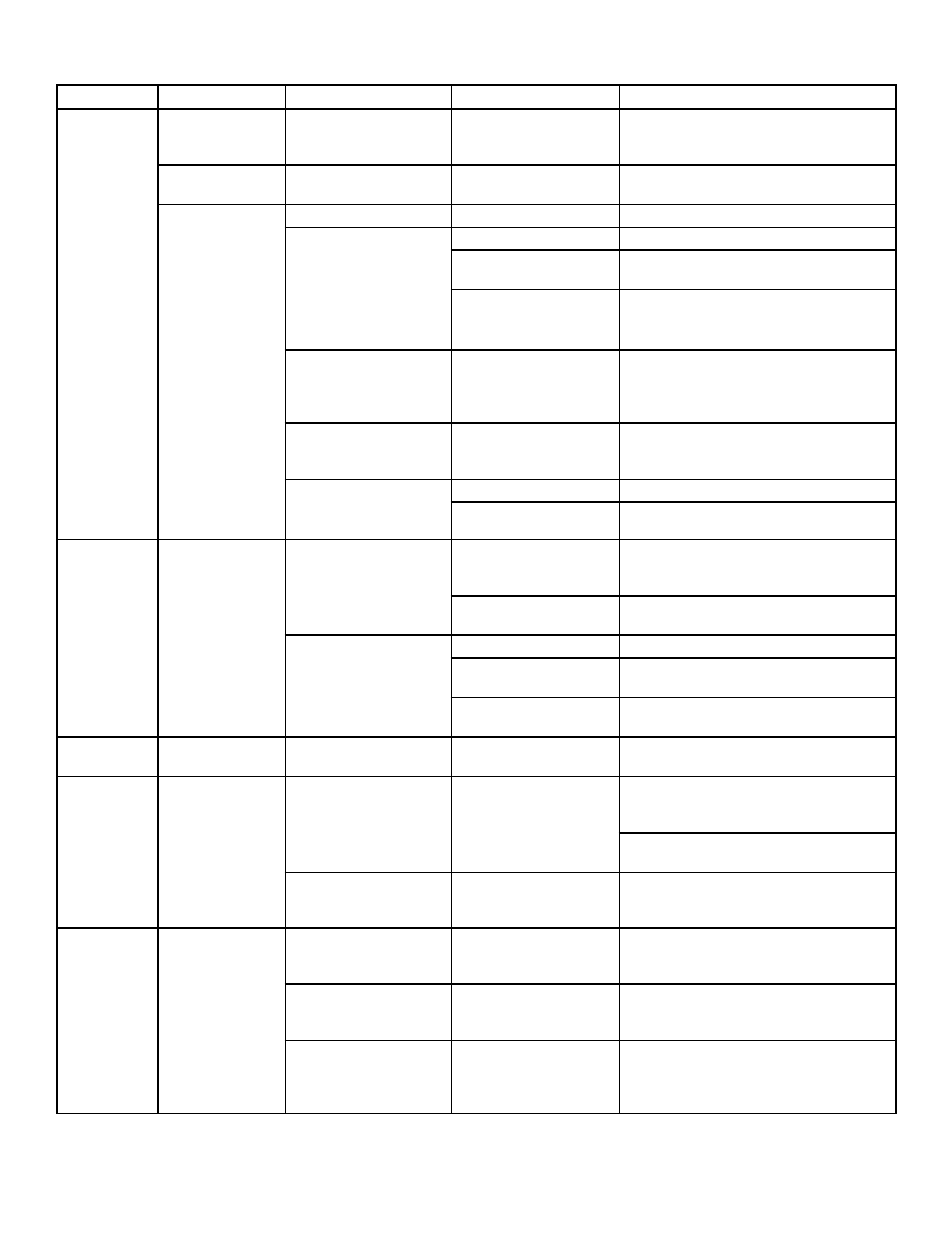
Revision 08/06, Effective Date August 22, 2006
PROBLEM
WHAT TO DO? INDICATION
CAUSE
SOLUTION/RECOMMENDATIONS
Low
penetration
rate under
prevailing
drilling
parameters
1. Check fluid
return.
Fluid not muddy.
Evidence of steel
cuttings
Drilling rebar
Adjust drilling parameters to
recommendations for rebar.
2. Check motor
speed range
Speed not correct for the
bit size used
See recommended speeds
. Check bit wear
Bit worn out.
Replace with new bit
Diamond without
exposure. (flush with
matrix)
Insufficient bit load
Increase bit load
Rotate with high RPM on
rebar
Reduce RPM, or resharpen bit
Loose material at bottom
of hole.
Break core, clean bottom of hole or reduce
RPM and drill with increased bit load
Face of bit plugged with
cuttings.
Not enough fluid
pumped. Cuttings burnt
to matrix. Diamonds
prevented from cutting.
Clean bit face by sharpening methods
such as drilling at low RPM in a
concrete block /8” deep max.
Increase water flow rate.
Face of bit covered with
steel. Steel cuttings
stick to bit face.
Steel cuttings stick to bit
face. Diamonds
prevented from cutting.
Clean bit face by drilling in
concrete block.
Reduce RPM.
Wearing of
diamonds.
Bit load too low
Increase bit load
Bit speed too high
Use lower speed: Increase bit load
Heavy wear
at Steel Tube
Deep grooves.
Worn or open guide
ways on cradle. Bore-
hole is getting undulated
Adjust guidance on carriage.
Protruding steel. pindle
is offset. Bit out of true.
Adjust guidance on carriage
Nicks or dirt on ounting faces
Heavy Wear
Bit is deformed
Replace bit
Poor cleaning of
abrasive cuttings.
Improve flushing.
Crown clearance worn
out.
Replace bit
No return of
fluid
Check where fluid
is leaking.
If leaking can be tolerated, continue
drilling with increaded attention.
Bit Stuck
1. Try to raise bit,
if impossible then,
2. Stop rotation
Loose material (cut steel
or aggregates) is
blocking between core
and bit or between bore-
hole and bit.
Step 1. Apply wrench and rotate bit in
both directions while bit is under tension.
If not successful:
Step 2. Try to over drill a hole slightly
larger than the stuck bit.
Drill moved during
drilling (poor fastening)
Disconnect bit and remove break core.
Start over with improved fastening of
machine.
Shear Pin Fail 1. Stop rotation
2. Raise bit.
Bit deviates, guide ways
on cradle have too much
clearance.
Disconnect machine, adjust guidance.
No clearance between
tube ID or OD and
crown ID or OD
Replace bit.
Drill impacted to stall at
lower speeds
Use recommended speed for the bit diam-
eter used. Raise bit when it begins to load
down. Feed bit slowly when
chattering begins
TABLE 3.
TROUBLESHOOTING