Troubleshooting – Longevity TIGWELD 200 SX User Manual
Page 15
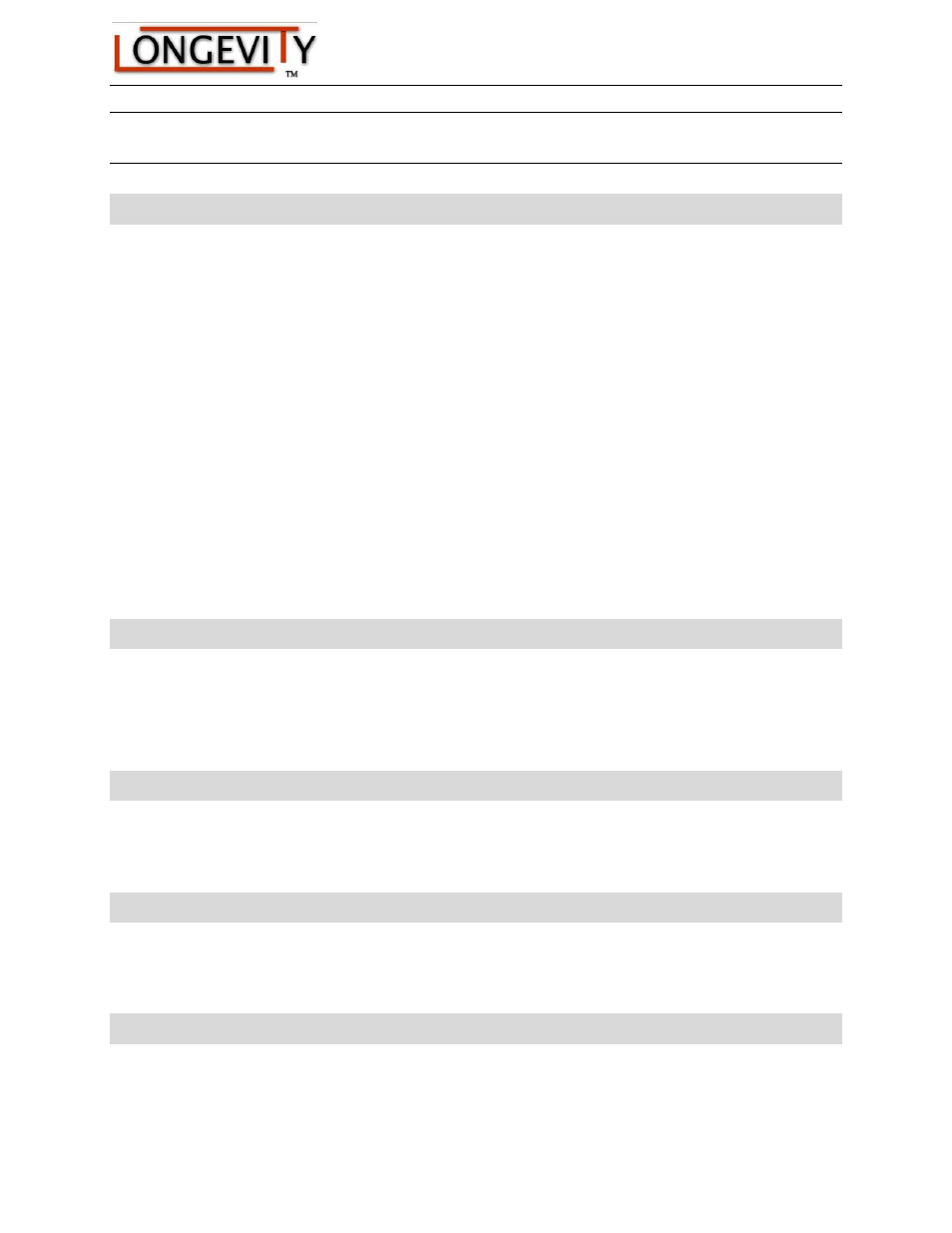
160 SX/200SX AC/DC TIG STICK WELDER
- 14 -
Troubleshooting
.
A、 Black welding spot
——This shows the welding spot is oxidized without being protected effectively and you can
make the following inspection :
1. Make sure that the valve of argon cylinder has been opened with sufficient pressure. As a rule,
if the pressure within the cylinder is lower than 0.5MPa, then it is necessary to refill the
cylinder.
2. Check if the argon flow-meter is turned on with sufficient flow. You can select different flow
rates in light of varying welding current, but too small flow may lead to inadequate gas
stiffness and thus failure to cover all the welded spots. We suggest argon flow should never be
lower than 3l/min no matter how weak the current will be.
3. The easiest way to check gas delivery is to touch the nozzle of welding torch to see whether
the gas passage of the welding torch is blocked.
4. Poor sealing of gas passage or lower gas purity will also give rise to welding quality trouble.
5. Strong air flow in the environment may also lead to deterioration of welding quality.
B、Difficulty in arc starting with easy arc breaking:
1. Make sure that the tungsten electrode in use is of good quality as discharge ability of inferior
tungsten electrode may fail the requirement;
2. Tungsten electrode without sharpening treatment is also unable to start arc and leads to
unstable arc.
C、Output current can’t reach the rated value:
Deviation of power voltage from the rated value will lead to unconformity of output current
value with the set value. When power voltage is lower than the rated value, maximum output
current of the welder may also be lower than the rated value.
D、Unstable current in the operation of the welder:
This may be attributed to the following factors:
1. Change in grid voltage;
2. Interference from the power grid or other power equipments.
E、
:Severely burn of the tungsten needle
The duty cycle is adjusted too large, causing emission from the workpiece to the tungsten
electron for too long, resulting in severe heat of the tungsten needles.