Operation, Assembly, Maintenance – Steele Products SP-PB214 User Manual
Page 6
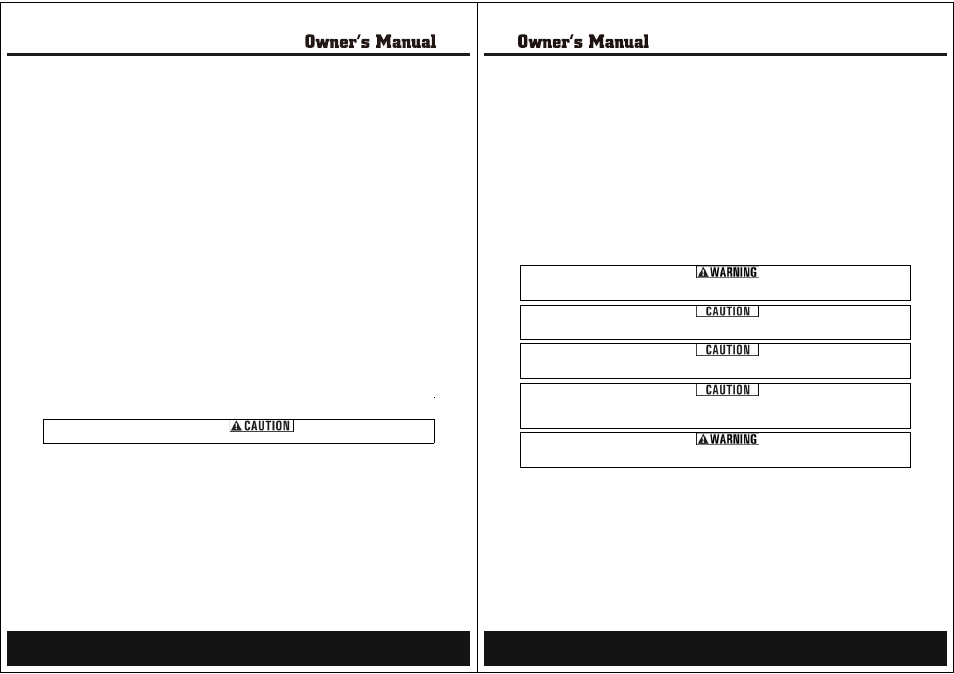
SETTINGS AND ADJUSTMENTS
Table
The table may be raised, lowered or swivelled about the column, by loosening the table support locking
handle (Fig.8). Adjust accordingly using the table crank, and re-tighten the locking handle. If the table
assembly moves stiffly when being swivelled about the column, loosen the upper collar allen screw
(at the rack) to allow the collar to move very slightly, thereby providing a little more clearance between
rack and collar. Tighten the allen screw when satisfied. The table may also be turned on its axis by
loosening the pinch bolt at its' mounting shaft.
Spindle Depth
Located around the spindle feed shaft is a Depth Stop Collar, printed with a graduated scale. The collar
is capable of turning about the shaft and may be locked in place by the locking screw. The scale is
printed in both inches and metric. To set a drilling depth: 1. With the power OFF, lower the drill bit so
that it contacts the work, and hold in that position. 2. Loosen the locking screw and turn the collar so
that the measurement for the depth of hole required is in line with the pointer (C). Lock the collar in
this position using the locking screw. The drill is now set to drill holes to your predetermined depth,
from that particular start point.
Changing Drill Speed
Before changing the speed, make sure the machine is switched OFF, and unplugged. Undo the Belt
Tension Locking Screws on either side of the head and turn lever clockwise to relieve any tension on
the belts. Refer to the chart inside the belt cover install the belts in the positions corresponding to the
spindle speed required. Level the motor, on its bracket, away from the head, by turning lever counter
clockwise so that tension is applied to the belts.
NOTE: The idler pulley will 'float' so that tension is equally applied to both belts. Tension is correct when
the belts deflect by approx. 1/2" at their center when using reasonable thumb pressure. Lock the motor in
this position using the two locking screws. If the belt should slip while drilling, adjust the belt tension.
OPERATION
Wear safety eyewear and dust filters or respirators while using this tool.
lnsert the drill bit into the jaws of the chuck by approximately 1". Be certain that the jaws do not touch
the flutes of the drill. Before tightening the chuck, make sure that the drill bit is centered within the jaws.
Make sure the table height and position is set so that drill travel is sufficient for the job in hand.
Make sure the work is securely clamped, or held in a drill vise bolted to the table. Never hold it with
bare hands. Severe personal injury may be caused if the workpiece is forced out of the operator's hand,
and damage to the machine incurred if the work strikes the column. If the piece is of irregular shape
and cannot be laid flat on the table, it should be securely blocked and clamped. Any tilting, twisting or
shifting, results not only in a rough hole, but also increases drill bit breakage.
For small workpieces that cannot be clamped to the table, use a Drill Press Vise. The vise must be
clamped or bolted to the table. When drilling completely through wood, always position a piece of scrap
wood between the workpiece and the table to prevent splintering on the underside of the workpiece as
the drill breaks through. The scrap piece of wood must make contact with the left side of the column.
In addition, set the depth of drill travel so that the drill cannot possibly come into contact with the table,
or, align the table so that the center hole is directly in line with the drill bit. When completely satisfied
that the setup is sound, lower the Chuck Guard into place, and switch the machine ON.
ASSEMBLY
11
lnsert KEY into switch. Key is made of yellow plastic. A light is also provided which is built into the
head. The light switch is located above the ON/OFF switch.
REMOVING THE CHUCK
To remove the chuck, pull the spindle down fully, using the feed handles. The slot in the side of the Quill
will become visible. Note the position of the chuck, perhaps by placing a chalk mark, in line with the
chuck, on the column, then raise the table so that it is only an inch or so below the position marked.
Place a thick cloth, or similar material, on the table to catch the chuck, to prevent damage when it drops.
Pull down the spindle once more, until the slot in the Quill tube is visible. lnsert the drift wedge into
the slot and give it a sharp tap, preferably with a copper hammer. This will break the seal between the
quill tube and the arbor, allowing the chuck to fall free, on to the cloth on the table. To disconnect the
chuck from the arbor, give it a sharp rap with a soft head mallet to break the taper seal.
NOTE: Morse taper drills (MTS), may also be used with this machine, and are inserted into the Quill to
replace the arbor. Removal is the same as that for removing the chuck.
MAINTENANCE
Disconnect the power supply before cleaning.Wear safety eyewear before cleaning.Used compressed
dry air to blow off dust and debris. Use a soft bristle brush if compressed air is not available.
Applying excessive force to the tool can overload the motor, decrease the life and increase the
wear on the tool.
Some chemicals can damage the product. Do not use harsh chemicals such as gasoline, carbon
tetrachloride, paint thinner, etc.
A qualified repair technician must perform any tool service or repair.Service or maintenance performed
by unqualified personnel could result in injury. Use only identical replacement parts. Use of unauthorized
parts or failure to follow maintenance instructions may create a risk of electric shock or injury.
Do not make contact with a grounded surface while using drill press.
Contact with surfaces like pipes, radiators or major appliances increase your risk of electric shock.
The Drill Press must be properly maintained for maximum performance. Always inspect before use.
Any damage should be repaired, and faults rectified. Please refer to the troubleshooting chart. If you
are unable to correct any problems, please contact customer service.
Monthly (When in constant use)
1. Check tightness of mounting bolts, and head and column securing set screws.
2. Check belt for wear and replace if frayed or damaged in any way.
3. Blow out any dust that may have accumulated in the motor fan.
4. Apply a thin coat of wax paste or light oil to the table and column for lubrication and to help prevent
corrosion.
Lubrication
All bearings are packed with grease at the factory and require no further lubrication. After use, remove
all swarf from the machine and thoroughly clean all surfaces. Components should be dry, with machined
surfaces lightly oiled. Always remove drill bits, and store in a safe place.
12