BMW 5 User Manual
Page 64
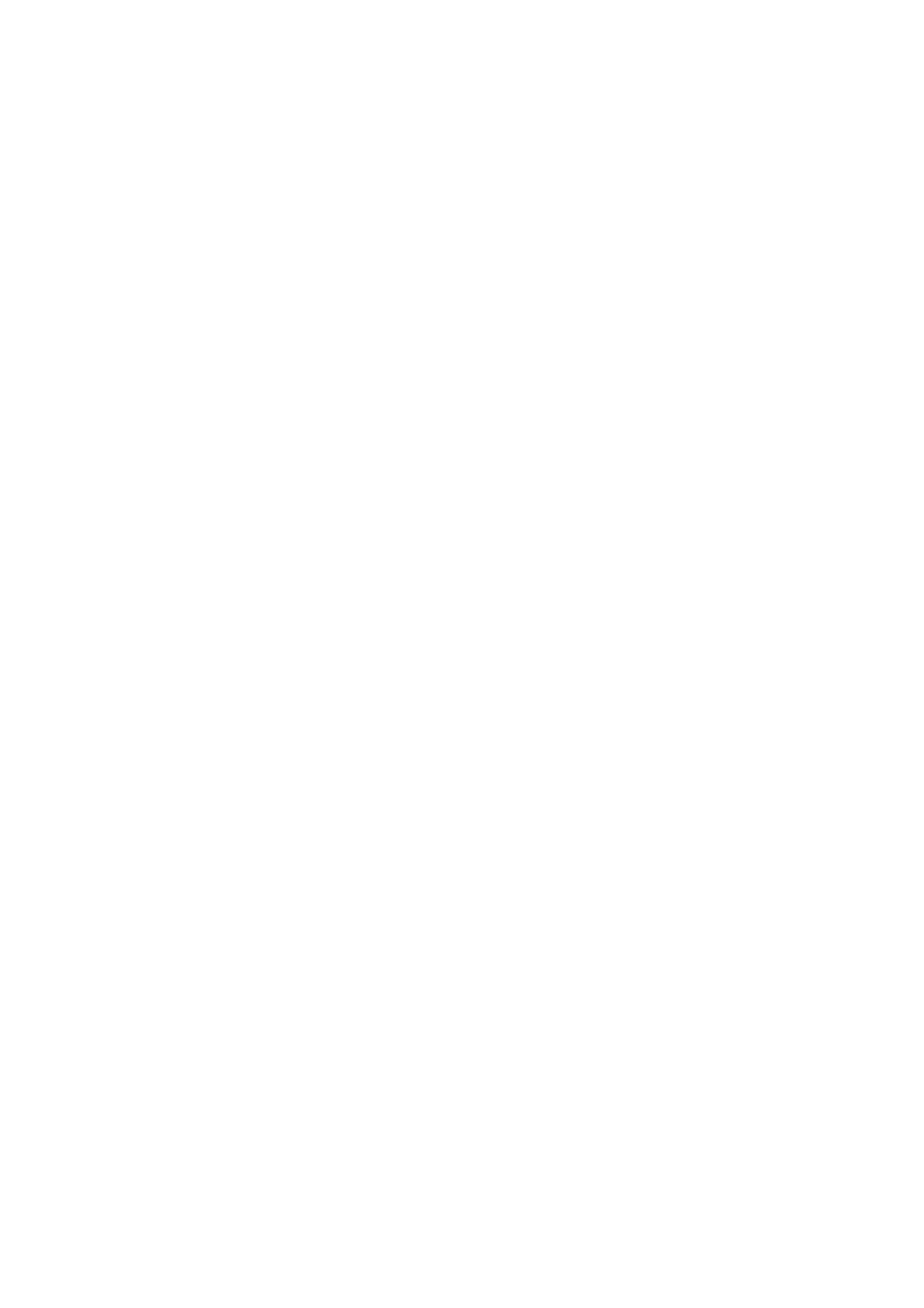
BMW
Media
Information
11/2009
Page 64
the process of fitting the chassis supports, and the actual process of body
production in the Bodyshop.
Further progress in production is ensured in the creation of value along
the production line and in logistics. BMW’s objective in all cases is to ensure
a clear-cut flow of individual parts – the one-piece flow process – all the way
from the supplier to the actual completion of the car itself.
Innovative production processes in the Bodyshop.
Innovative production technologies have been developed for the production
of several models in correspondingly high numbers. One example is the
production of aluminium doors with the support of the BMW’s Aluminium
Competence Centre in Dingolfing. The know-how gained in the research
processes conducted here, as well as the innovative developments made
possible in this way, benefit all of the BMW Group’s brands.
The large share of aluminium in the body components of the new
BMW 5 Series Sedan enables the experts in Dingolfing to contribute
even more of their outstanding competence in this technology. The new
aluminium processing technology developed at BMW Plant Dingolfing,
for example, sets the foundation for the precise modelling of sophisticated
design features such as the character line on the side doors. The large
load-bearing aluminium plate shells within the doors, in turn, ensure a high
standard of all-round stiffness. And to join the individual components with
one another, the Plant uses both laser welding and structural bonding.
BMW Plant Dingolfing also uses innovative processes in the production
of steel panel components. Two new steel panel presses involving an
investment of approximately Euro 50 million will serve in future to give
the body components of the new BMW 5 Series Sedan a unique standard
of quality.
BMW is the world’s first car maker to use hard-pressing technology at
Plant Dingolfing, with hot-galvanised steel plate first being moulded cold
and subsequently heated to a temperature of 900
o
C or 1,650
o
F. Then the
components are cooled down in a pressing tool with integrated water-cooling
to approximately 70
o
C or 160
o
F within a few seconds, being hardened in
the process with maximum efficiency. This gives the components involved
three to four times the stiffness of conventional steel plate.
The ProgDie rapid-action press also new in the production process likewise
offers an exceptionally high standard of efficiency in production and the use
of energy. Among the world’s largest presses of its kind, the ProgDie press