Duff-Norton SK6905-100-1 User Manual
Page 8
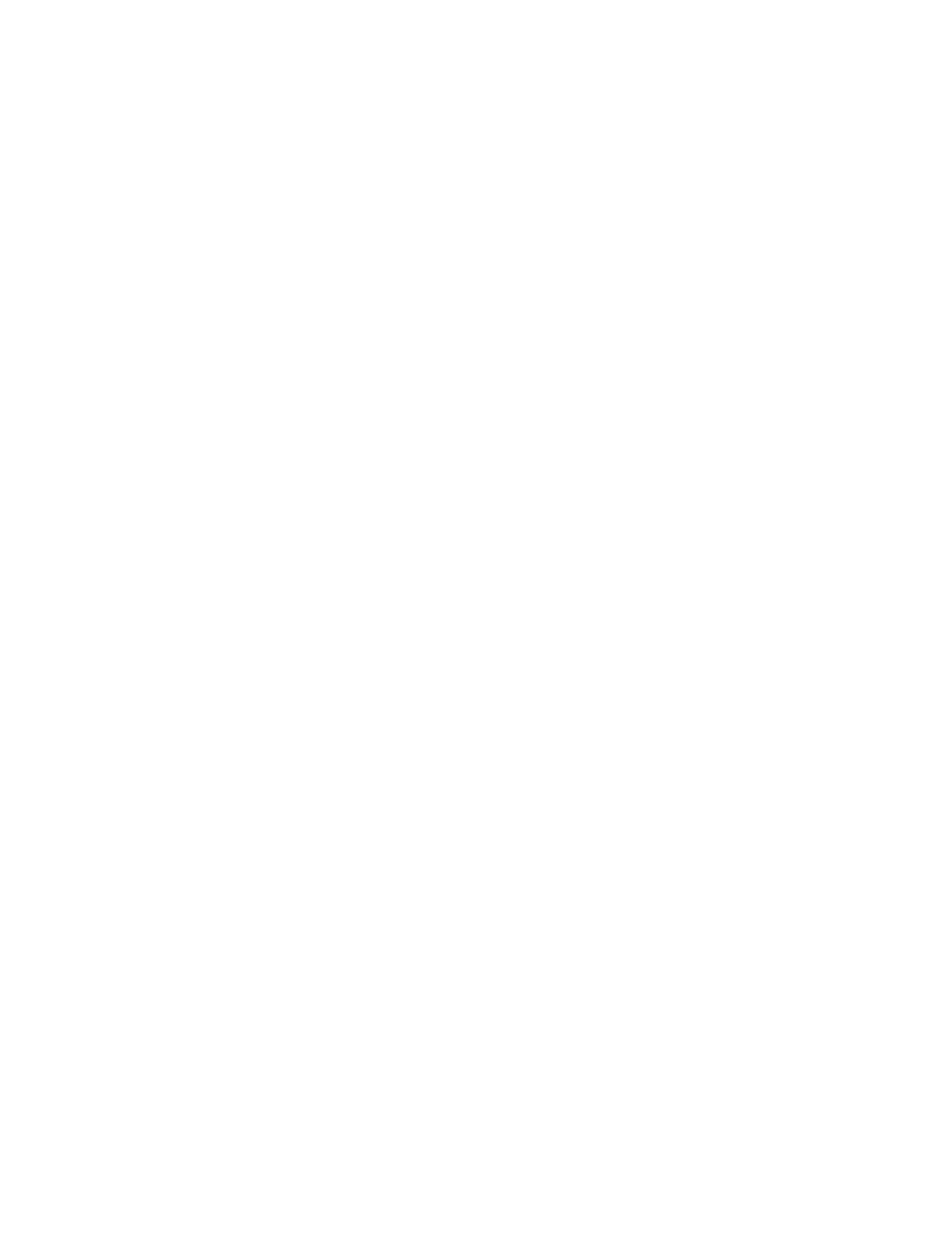
4-1. Lubrication
Duff-Norton recommends the use of the following
lubricant in conjunction with proper maintenance
procedures of this unit: Shell Oil Co. Darina EP2.
4-2. Required Tools
A bearing puller and press, soft jaw table clamp and
common hand tools are required for proper disassembly
and assembly.
4-3. General Procedures
Duff-Norton recommends following these procedures
during disassembly and assembly:
1. Tag critical parts to facilitate reassembly.
2. Mark mating surfaces to ensure proper meshing.
3. Clean and lubricate parts as required.
4. All seals must be replaced at time of rebuild.
5. All screws, washers and other small common parts
must be replaced if mutilated in any way.
4-4. Disassembly
Disassemble the actuator as follows while referring to
Figure 5.1. Read the instructions thoroughly before
disassembling.
NOTE
Disassembly should be accomplished on a clean cloth.
1. Clamp actuator housing (22) in vice (use soft jaws).
Unit should be in horizontal position with switch cover
(2) up.
2. Remove screws (1) from cover (2) housing (22), limit
switch box and remove switch cover (2) and gasket (3).
3. If unit has potentiometer, loosen nut (7a) and remove
potentiometer (7) from potentiometer bracket (6).
4. Remove socket head cap screws (33) and lock-
washers (32) from motor (23) and remove motor (23)
from motor adaptor (31).
5. Remove screws (30) from housing (22) and remove
motor adaptor (31).
6. Remove pinion (36) and bearing (35) from housing
(22).
7. Remove retaining ring (34) from pinion (36) and
remove bearing (35) from pinion (36).
8. Clamp housing (22) clevis end in vice (use soft jaws),
remove set screw (39) from housing (22).
9. Unscrew outer tube (45) from housing (22) and remove
translating tube (54) screw (50), gear (41) and outer tube (45)
from housing (22).
10 Remove translating tube (54) from outer tube (45) by
slipping outer tube (45) over translating tube (54) towards
clevis end.
11. Remove seal (47) from outer tube (45) and press guide
bushing (46) from outer tube (45). Seal and guide bushing
need not be removed unless damaged.
12. Support screw (50) end taking care not to damage gear
(41) teeth. With a
3
/
16
” diameter punch, drive pin (42) from
screw (50) and remove gear (41), bearing (43) and washer
(44) from screw.
13. Thread screw (50) part way out of nut (52) and check
screw (50) and nut (52) for wear. There should not be
excessive play between screw and nut thread. If screw or nut
are not excessively worn, the disassembly of screw (50), nut
(52) and translating tube (54) will not be necessary.
14. Pins (53) should be approximately
1
/
32
” above translating
tube (54) OD. Grind pins (53) flush with OD of translating
tube (54).
15. Using
3
/
16
” diameter punch, drive pins (53) far enough
into the lifting nut (52) to just clear the translating tube (54)
wall. Do not drive pins against OD of screw (50). Remove
nut (52) with screw (50) from translating tube (54).
16. Remove screw (50) from nut (52).
17. Remove pins (53) from nut (52) by driving pins (53)
remaining distance into ID of nut (52).
18. Remove stop pin (51) from screws (50).
19. If worm (48) or pin (49) must be replaced, remove worm
(48) from pin (49) by closing pliers loosely around pin (49)
behind worm and lightly tap up with a plastic or wood
hammer. To remove pin (49) from screw (50) clamp pin (49)
in vise and rotate and pull on screw (50). Pin will come out.
20. Ball break disassembly. Remove set screws (29) from
ball housing (26) and remove springs (28) and balls (27).
Remove ball housing (26) from coupling (24).
21. Drive pin (25) from motor (23) shaft and remove
coupling (24). Remove damper (55) from I.D. of coupling
(24).
SECTION IV
MAINTENANCE
8