Site preparation, Installation, Operation – Graymills Tempest Tl2 OMI User Manual
Page 3
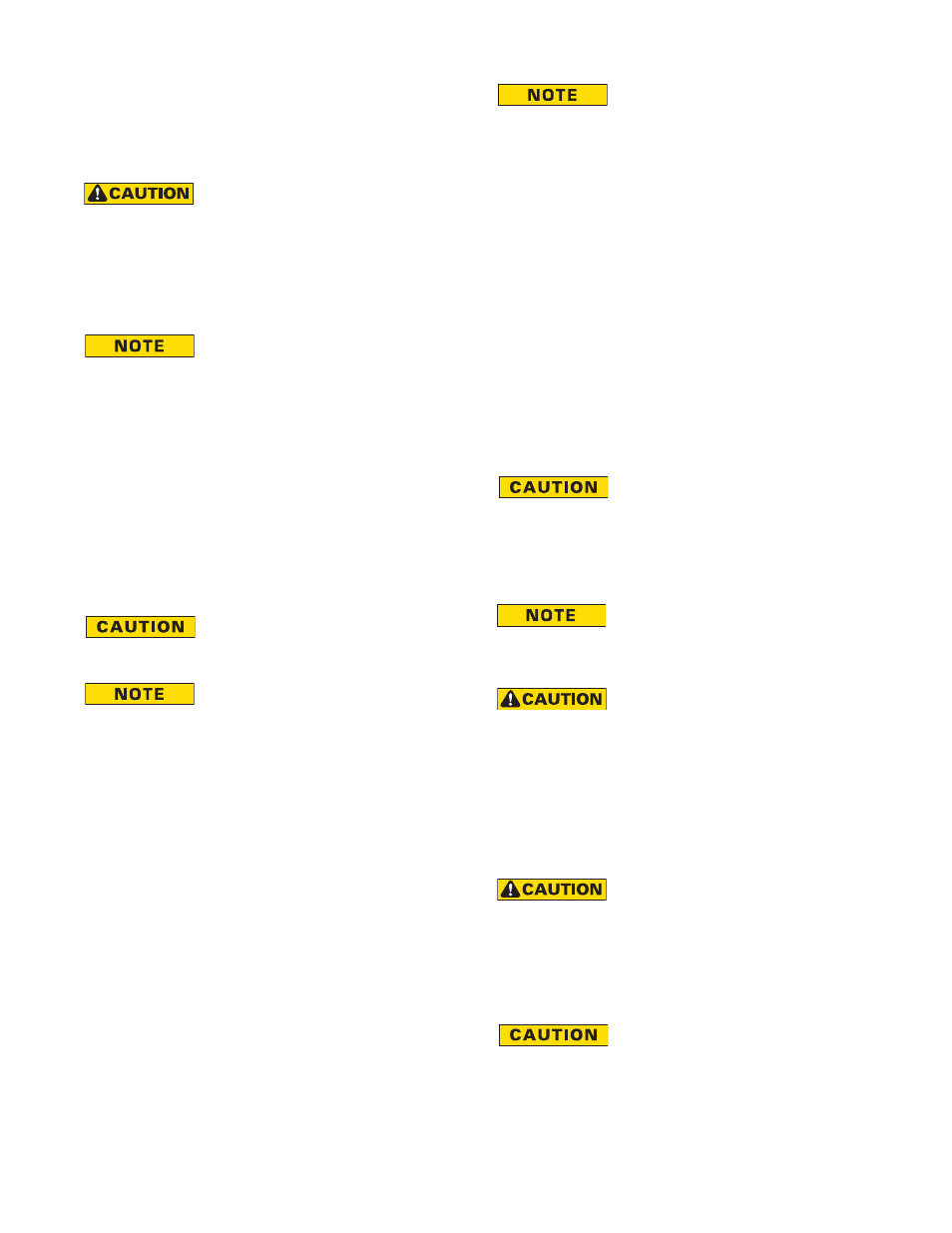
3
SITE PREPARATION
Before installing, careful consideration should be given to the place of
operation. Place unit on a smooth, level surface. Use leveling feet to
correct for minor variations in floor.
Place Tempest near a 115V, 60Hz, 1-ph grounded electrical outlet.
You will also need compressed air, maximum of 100PSI.
the work area should be well ventilated and lit.
Provide adequate lighting in the work area to permit viewing of the
cleaning process and of the floor area around the machine. Be sure
to allow adequate room to bring work to and from the machine. Use
flooring or floor covering that does not become slippery when wet.
Provide sufficient clearance around the machine for fluid changeovers
and servicing.
A drain coupling has been provided in the reservoir. It is recommended
to plumb a drain valve to this coupling to facilitate cleaning.
we recommend our low foaming aquatene
™
. Contact graymills for
specific details on the formula best suited for your application.
INSTALLATION
For Tempest 10 Unit:
1. Disconnect Drain Pipe
(Fig. 1, p.5) and lower pipe into pail reservoir
2. Remove entire pail assembly from shelf and set on floor.
3. Loosen snap ring securing ring to pail and remove lids (Fig. 2 and
3, p.5)
4. Graymills recommends use of pail liners as a means of simplifying
liquid changes and insuring reservoir’s long life
be careful to prevent liner from coming into contact with heater element
as the plastic will melt on element and cause heater failure
5. Fill pail with low foam detergent and water, following mixing
directions on recommended detergent package.
Excessive foaming caused by improper mixing ratios or use of
improper detergents, can result in loss of pump prime and can
damage heater and/or pump. Should foaming occur, skim off
excessive foam and add water to proper level or add defoaming
agents. If foaming continues, dispose of liquid and review detergent
ratios and/or formulation
6. Replace lid and secure with snap ring. Put assembly back within
cabinet.
7. Prime pump by filling intake hose completely with water, then
connecting filter hose to pump.
8. Plug heater cord into lower socket in outlet box above pump shelf.
Plug pump cord into upper socket (Fig. 4, p.5).
9. Connect drain hose (Fig. 1, p.5) and close lower cabinet door.
10.Plug unit’s power cord into 115V, 60 Hz, 1-ph grounded outlet.
11.Check GFI Switch on rear of contorl box to make sure it is ON.
For Tempest 20S Unit:
1. Fill 20-gallon cleaning solution reservoir
to at least a 12” depth with
appropriate cleaning solution. To protect equipment and personnel,
the fluid level should never fall below 4” from the top of the tank
and must cover the coiled portion of the heating element and the
thermostat’s thermal bulb.
2. With door closed and latched, activate main power switch on the
control panel.
OPERATION
The spray chamber and reservoir of the Tempest 10S and 20S units
are stainless steel. The base is carbon steel.
If you have purchased a heated Tempest 10 unit with a carbon steel
cabinet, some uses of water-based cleaning materials will generate
steam and water vapor. Surfaces inside the cabinet will be subject
to rusting. this is surface rust and does not appreciably affect the
service and use of the unit.
We recommend that the door be left open
when the unit is not in use. Leaving the door open when not in use
may lessen condensation and rust inside the unit. If your cleaning
requirements cannot tolerate any rust or contamination, please contact
Graymills about stainless steel cabinets. Also, check with your cleaning
fluid supplier to make sure your cleaning materials contain a rust
inhibitor.
the graymills warranty does not cover rusting of carbon steel parts.
Check fluid level in cleaning solution reservoir daily. Assure level is at
or above minimum level at all times. Heavy, constant use may warrant
daily fluid changes.
Inspect filter bag on end of drain pipe daily. Filter bag is secured to
drain pipe with a reusable plastic tie – there is a small plastic release
lever on locking cube.(Fig. 7, p.5) Properly dispose of any solid waste
accumulation, rinse bag in water, and re-attach to drain pipe.
failure to keep cleaning solution reservoir full can result in heater
failure, loss of pump prime, or over heating of the fluid.
do Not operate unit without a filter bag.
Inspect heating element daily. Any foreign material should be removed
by gently scrubbing.
Do NOT neglect cleaning of the heating element. Failure to do so will
cause premature failure. Do NOT allow oil or sludge to bake onto the
heater element as premature heater burnout will result.
at this time the pump is fully operational. do Not depress the foot
pedal switch unless the spray hose is being gripped. under pressure,
without gripping, it will fly around potentially causing damage.
• Using the adjustable thermostat, set heat to desired temperature up
to 120°F maximum. Allow approximately one to two hours for the
heater to warm the solution to operating temperature.
• Open spray chamber door and secure with door retaining latch
(Fig. 5, p.5). Carefully load parts into the cabinet, distributing
weight as evenly as possible.
tempest is equipped with a pressure relief valve in the spray cabinet
that is intended as a safety device (figure 6). when pressure is
relieved, the valve automatically resets. Should pressure inside spray
delivery system reach an unsafe level, relief valve will vent excess
pressure back into cabinet. this valve must be kept clean and free of all
contaminants to insure its proper functioning. activation of the pressure
relief valve is not expected during normal operation.
adjustable nozzle should never be adjusted to a no-flow position as it may
activate the pressure relief valve and cause possible mechanical failure of
the pump. if no flow is desired, remove foot from foot pedal switch.
always completely lift parts into and out of cabinet. Never allow parts
to rest on door opening as they will damage gasket material. keep
gaskets clean and free of contaminants. failure to do so reduces gasket
life and water sealing effectiveness.
(Continued on next page)