Troubleshooting, Accessories – Silverline 200A Inverter Arc Welder User Manual
Page 8
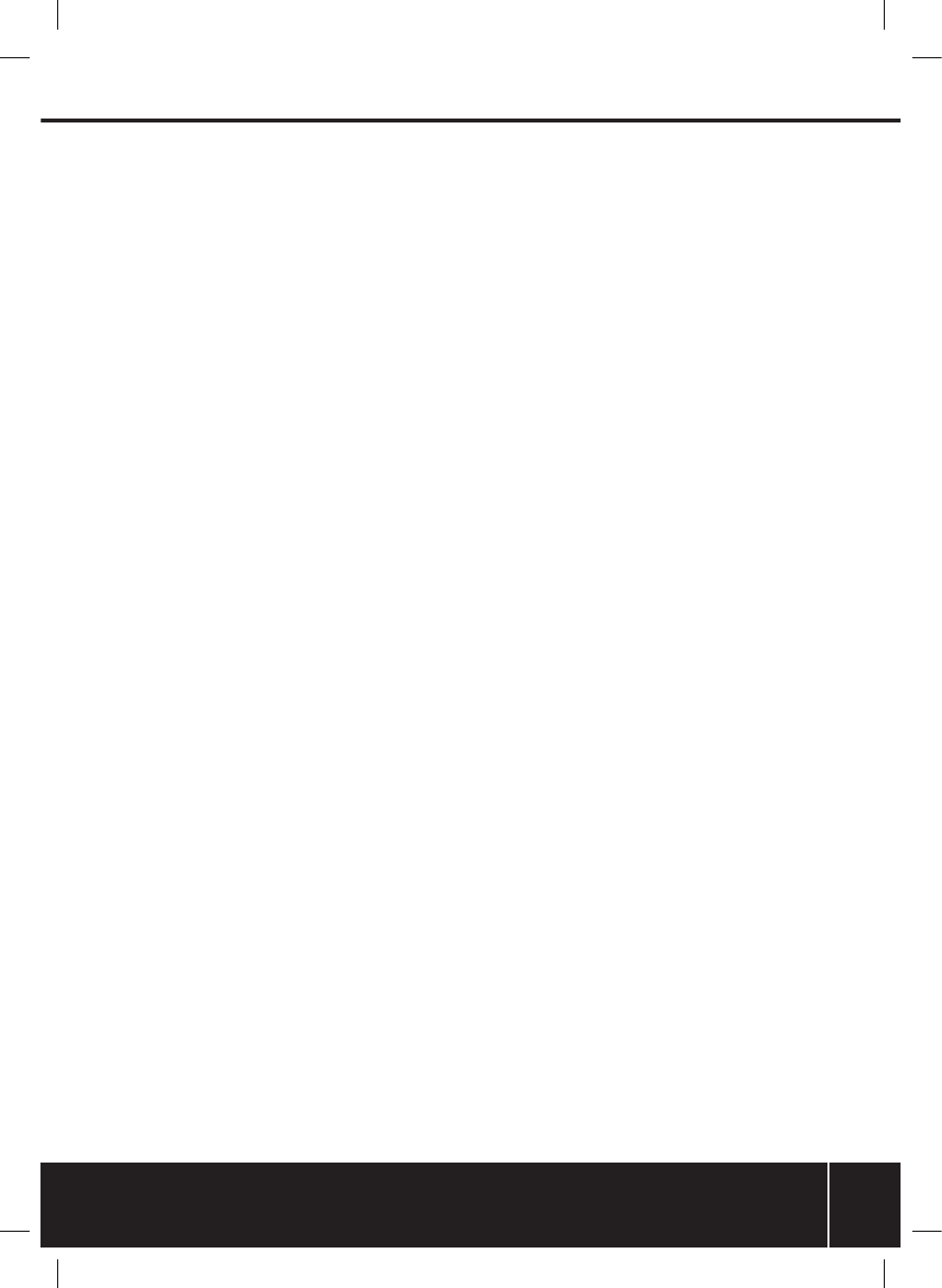
www.silverlinetools.com
7
200A Inverter Arc Welder
103597
Operating Instructions
Warning
• Always unplug the welding machine from the mains supply and allow to
cool completely before attempting to fit or replace any part
Setting the welder
• Use the On/Off Switch (10) to switch on the welder
• The Current Adjuster (12) controls the welding current
• To achieve a good quality weld, the current adjuster must be set correctly
(see Duty Cycle for guidance)
• Turning the current adjuster clockwise will increase the welding current;
turning the adjuster anti-clockwise will reduce the welding current
Welding rod selection
• In order to produce a good quality weld, the correct type of welding rod
must be used. Welding rods are available in a variety of thicknesses and
materials, and with a range of coatings
• Refer to rod manufacturers guidelines to select the correct rod for your
requirements
Duty cycle / thermal cut out
• This machine is designed to weld constantly at 100A or below. For
welding at greater currents, refer to the duty cycle
• The duty cycle defines a percentage of time in relation to overall time that
the welder can be used for each current setting.
• If the machine is overloaded, or used beyond its duty cycle, it will
automatically cut out and the Overheating Indicator Light (14) will
illuminate
• Allow the machine to cool. The cut-out will automatically reset and the
overheating indicator light extinguish once the machine is ready for use
• Using the machine at reduced current settings and maintaining good
ventilation will maximise the duty cycle
• A duty cycle gives an approximate guide to how long you can use the
welder. As an example if the welder indicates overheat and stops
working at the 100A setting after 1.5 minutes of continuous use its likely
to need a 8.5 minute cooling period approximately before it can be used
again if the duty cycle is 15%. It is for the user to try to adjust the work
pattern so it doesn’t force the welder into over-heat condition which will
maximise the lifespan of the unit. So only operating the unit for 1 minute
in every 5.5 minutes may prevent the welder going into overheat mode
and switching off
• Where possible try to avoid using the maximum amp settings where the
duty cycle is 10 or 15% as this will stress the internal components more
than lower amp settings with higher duty cycles
Preparing to weld
• Ensure that parts to be joined are clean and free from rust, paint, or other
finishes using either the supplied hammer brush or other tools
• All parts should be well supported, with a gap of approximately 1mm
where you intend to form the welded joint
• Check that there are no flammable materials in the vicinity of the work
area
• Attach the Earth Clamp (18) to a cleaned area of one of the parts, as near
as practical to where the joint will be. Never attach the earth clamp to the
casing of the welder
• Squeeze the Electrode Clamp (17), to open the jaws. Place an electrode
into the jaws, and release. The electrode should be firmly gripped, with
the clamp contacting the clean metal part (not the coated part)
• Do a final check of the area you will be working in while reading the
safety information provided in this manual
• Connect the welder to the mains power supply
Welding
WARNING: Using a welder correctly is a technical skill. A welder used
incorrectly can be highly dangerous. The information presented below is
general guidance only. If you are not entirely confident in your ability to use
this tool safely
DO NOT USE.
• Switch on the welder using the On/Off Switch (10). The Power Indicator
(13) will illuminate
• Turn the Current Adjuster (12) clockwise to the required current for the
thickness of electrode you are using, as indicated on the scale.
• Hold the Electrode Clamp (17) in one hand, and the Welding Mask (9)
in the other
• Position the rod at an angle of approximately 60-75˚ angle from the
surface or 15-30 ˚ from vertical, with the tip at approximately 30mm
away from the metal
• Hold the mask over your face, and tap the rod against the metal
• An arc should strike between the metal and the tip. Try to hold the tip
of the rod a distance away from the metal equal to the rod thickness.
Maintain the arc for 1-2 seconds, then move the rod away
• Allow the weld to cool slightly, and move the mask away from your face.
If the settings were correct, a round ‘spot’ weld should have formed
• If the weld has not fully penetrated the metal, increase the current
setting. If a hole has been made in the metal, reduce the current setting
• Practice making ‘spot’ welds until you are confident using the machine,
and selecting settings
• To form a ‘seam’ weld, maintain the arc for longer, and slowly move the
rod forward at the same time. The speed at which the rod is moved is
crucial to achieving a good weld
• If the machine settings are correct, the arc should be steady, and produce
a crackling sound. Be aware that you will have to gradually move the
electrode rod holder closer to the metal as the rod is used up
• Once the weld bead is complete, switch off the welder by turning the
current control knob anticlockwise to the lowest setting and then turn off.
The Power Indicator (13) will be extinguished
• Remove excess and splatters using the chipping hammer and wire brush.
Do not attempt to weld over beads unless properly cleaned
• There are lots of different techniques for using arc welders which
are beyond the scope of this manual. If you are new to welding seek
additional advice for exactly how you plan to use your arc welder. Always
spend time configuring the welder to the correct current, polarity (DCEP
or DCEN) and use the appropriate size and type of electrode/rod
• Creating neat, high quality welds is a skill that takes time to master.
Practice and good preparation will help to make satisfactory welds
Troubleshooting
Should you experience any problem with the welder please make the
following checks:-
• That the welding current is correct for the diameter and type of electrode
in use
• That the power supply is on, and the power indicator light is on. If the
power indicator light is not on there is a power supply problem (for
example a circuit breaker may have blown)
• That the correct voltage is being used as indicated on the rating plate
• That you have not exceeded the duty cycle and the thermal cut-out is
in operation
• That the cables are undamaged and that there is nothing causing a
short circuit
• That all circuit connections are correct. You should pay particular
attention to the work clamp, making sure that it is correctly attached to
the workpiece and that there is no grease, paint or other contaminate
that could cause a bad connection
Accessories
Contact your Silverline stockist for a range of additional accessories to
complement and enhance the use of your welder and also replace worn or
damaged parts.
103597_Z1MANPRO1.indd 7
07/02/2013 11:24