Operation – Hot Max Torches 125WFG User Manual
Page 15
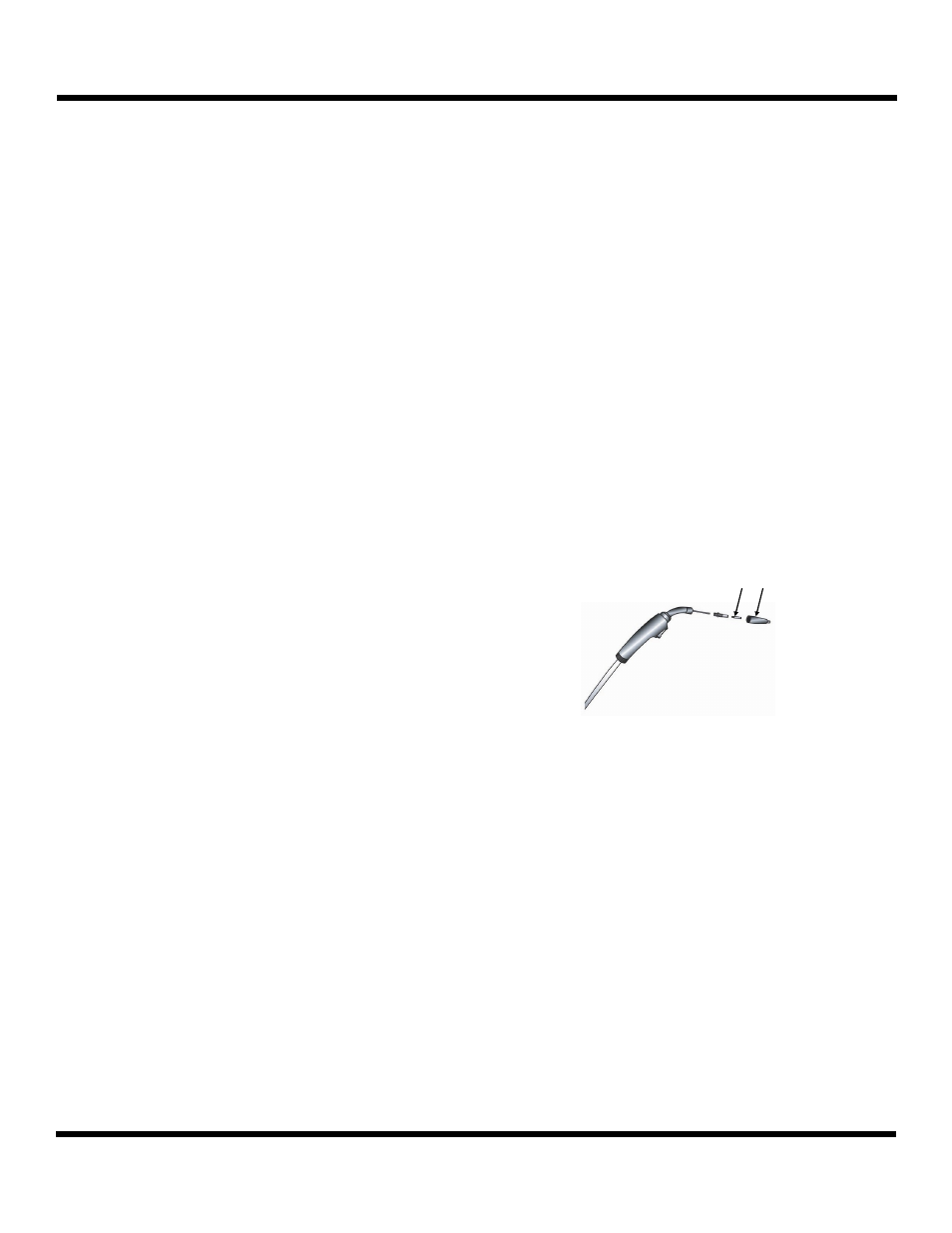
KDAR Company
14
Operation
Welding
1. See Suggested Settings at the back of this manual
or on the inside of the wire feed compartment door
for welding wire and shielding gas recommenda-
tions.
2 See Suggested Settings for information on setting
the controls on the Hot Max 125WFG for specific
welding wire and metal thickness.
3. Set the voltage and wire speed.
4. Insure the unit is set up for the correct polarity for
the welding wire and process being used. The Hot
Max 125WFG is shipped set up for FCAW (Flux
Cored Arc Welding)
5. Insure the proper nozzle and tip are installed on the
gun for the welding wire and process being used.
6. If required, turn on gas supply.
7. Connect the ground clamp to the metal being
welded. The clamp must make a good connection.
8. Position the gun of the joint to be welded. The
wire can touch the metal lightly.
9. Lower the welding helmet, pull the trigger on the
gun and start welding. The contact tip should be
about 3/8” from the work surface.
10. Release the trigger to stop welding and pull the
gun away from the work after the arc has stopped.
11. If there is no more welding to be done, close the
valve on the gas cylinder (if gas was used) and pull
the trigger on the gun to release the gas pressure
and then turn off the Hot Max 125WFG.
Changing the Welder for Feeding
Different Wire Sizes
The Hot Max 125WFG is shipped ready to
run .030” gasless flux cored wire. To run other siz-
es of wire the contact tip must be changed and the
drive feed roll may need to be changed.
Changing the Contact Tip
1. To change the contact tip (1) you must first
remove the nozzle (2). This is done by un-
screwing it counter clockwise.
2. Unscrew the contact tip counter clockwise.
3. Screw in selected contact tip clockwise. Hand
tighten only.
4. Replace nozzle by screwing on clockwise.
2
1
Figure 14