Section 3 - operation & maintenance, Initial start up procedure, Maintenance information – Summers 2510 DT User Manual
Page 57: Start-up -1 hydraulic operation and maintenance -1, Start-up and hydraulic operation, Maintenance
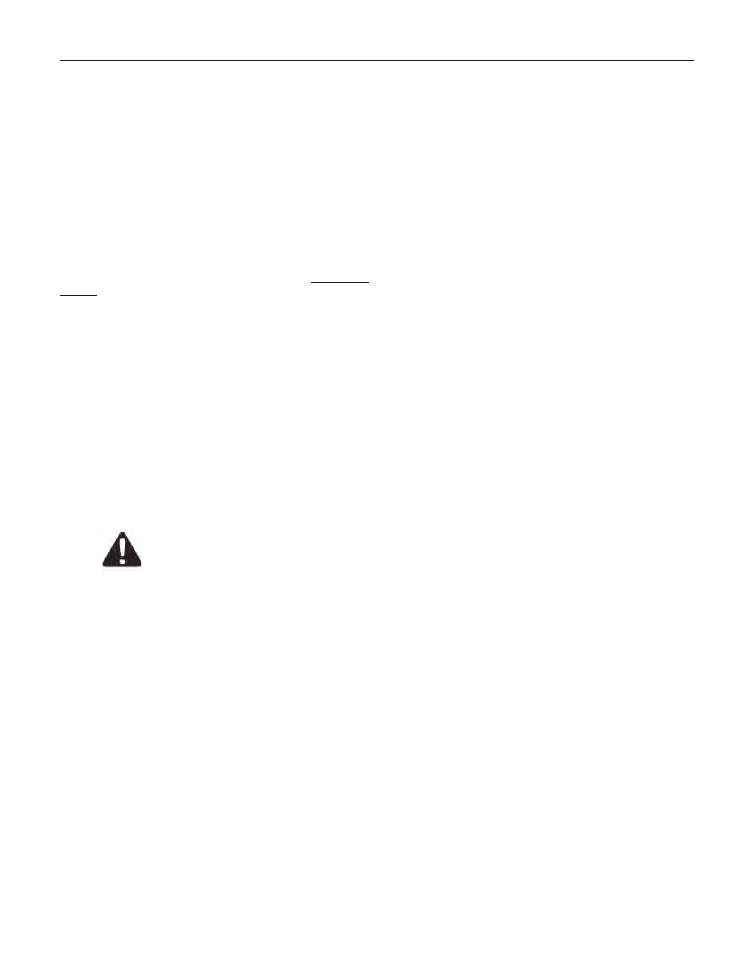
SECTION 3 - OPERATION & MAINTENANCE
3-1
INITIAL START UP PROCEDURE FOR DISK LIFT
HYDRAULIC CYLINDERS
This disk has a Master-Slave Hydraulic Lift System. Fully extend
hydraulic cylinders and maintain hydraulic pressure for 30 seconds
to insure all air is purged from system. See diagram on previous
page.
NOTE: As oil is pumped into the base end of master cylinder,
oil is forced out of the rod end into the base end of each slave
cylinder. To compensate for the smaller volume of oil in the rod
end of the master cylinder, each slave cylinder is 1/2” smaller
in diameter. When cylinders are fully extended, oil will bypass
through a rephasing slot on each cylinder in order to equalize the
system. The tractor SCV lever must be held for a few seconds to
accomplish this passage of oil through the system.
INITIAL START-UP PROCEDURE FOR WING LIFT
HYDRAULIC CYLINDERS
The wing lift hydraulic cylinders on this disk must be charged with
oil before attempting to raise the wings.
The best method of performing this is to disconnect the rod end
of the fold cylinders from the wings and connect the hoses to the
tractor’s couplers. Make sure the tractor reservoir is full of manu-
facturer’s recommended hydraulic oil. Extend and retract the
cylinders until the action is positive and all air is purged from the
system. Due to the amount of oil required to fill the cylinders
and lines, additional hydraulic oil may be required. After cylinders
have been filled with oil, reconnect the rod ends of the cylinders
to the wings.
CAUTION: Stand clear whenever raising
or lowering the wings.
START-UP AND HYDRAULIC OPERATION
Before lowering the wings, remove the safety lock pins and place
them in the storage positions. After wings are lowered, extend
cylinders fully.
BEFORE INITIAL OPERATION
1. After receiving or assembling your disk, it is a good practice
to double check entire machine so that all bolts are securely
tightened.
2. Make sure all grease fittings are in place and greased properly.
3. Inflate all lift tires to the recommended inflation pressure and
check wheel bolts. (See Maintenance for specifications.)
AFTER FIRST TWO HOURS OF OPERATION
1. Recheck wheel bolts for tightness and tighten spindle nuts if any
side-play is evident in the bearings.
2. Check gang shafts for tightness. This procedure should be re-
peated daily through the first twenty hours of operation. Gang
shafts should be tightened to 1200 foot-pounds.
NOTE: A 1/4” spacer (PN 8X0366) is available
and should be installed when the castle nut
has been tightened past lock bolt.
3. Bearing and C-shaped shank mounting bolts should be checked
for tightness. This procedure should also be repeated daily
during the first twenty hours of operation.
4. The scrapers on your disks should be checked and tightened
if needed. Scrapers may have to be adjusted periodically to
account for wear and different field conditions.
MAINTENANCE
GANG BEARINGS:
Note: Zerks are installed on both front and back of gang bearing
cast holders for your convenience. Both zerks lead to the bearing,
only one needs to be greased.
To prevent contamination, insure that coupler and zerk are clean.
To maximize bearing life, grease bearings at mid day or end of day
when bearings are at operating temperature.
Every 20 hours: Add three strokes (approx. .14 oz.) of grease to
gang bearing. Rotate gang 2 to 3 revolutions. Add an additional
three strokes of grease.
GENERAL:
Daily: Grease all pivot points located on wing lift, disk lift arms,
and hitch.
Check all wheel bolts/nuts for tightness. Recommended torque
listed below:
Hub Wheel Bolt/Nut Torque
614 – 6 Bolt
170 ft-lb
812 – 8 Bolt
240 ft-lb
817 - 8 Bolt
240 ft-lb
Tighten spindle nuts if any side-play is evident in the bearings.
Maintain disk gang torque at 1200 ft. lb.
Seasonally: Clean and repack wheel bearings.
TIRE INFLATION:
Recommended tire inflations listed below:
Size
Ply Pressure
11L x 15
LRF
85 psi
12.5L x 15
LRF
90 psi
340/65R18
148A8
78 psi