Sym-metric series – screw jacks, 6 disassembly / assembly instructions (d.a.i.) – Power Jacks S-Series User Manual
Page 7
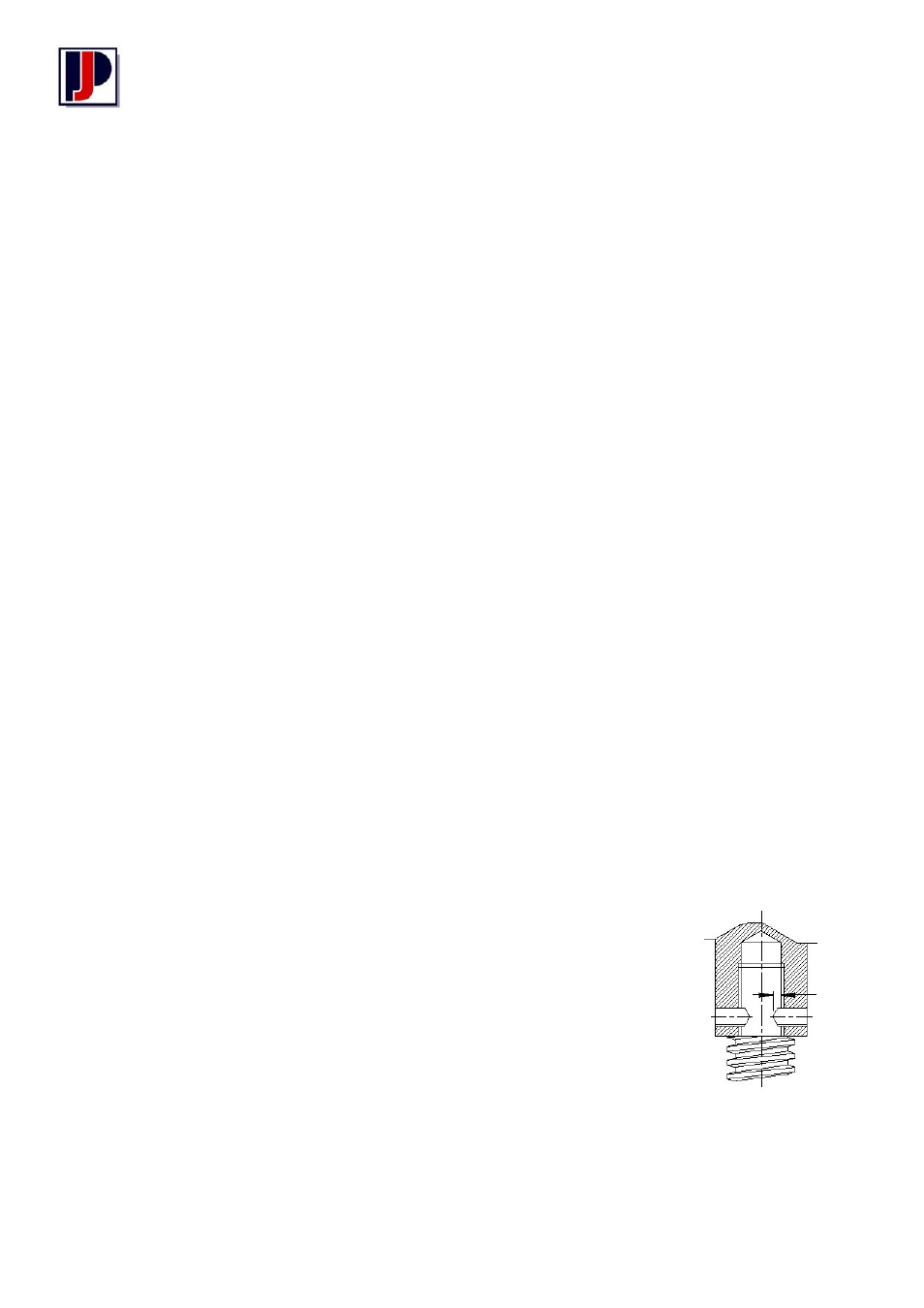
7
Sym-metric Series – Screw Jacks
6 Disassembly / Assembly Instructions (D.A.I.)
6.1 Translating Screw D.A.I
6.1.1 Main
Unit
6.1.1.1 Ensure that shell cap grub screw and plug (18) are slackened back clear of the thread grip (36) in
shell (1) before unscrewing the shell cap (It may be necessary to tap shell cap loose).
6.1.1.2 On some models it will be necessary to remove the worm shaft (4) before the worm gear assembly
can be pulled clear of the shell.
6.1.1.3 Check all parts for damage or excessive wear and replace where necessary paying special
attention to “O” rings (13) & oil seals (8 & 9).
6.1.1.4 After re-assembly of the worm shaft assembly, strike each end of worm sharply with a wooden or
fibre mallet to seat bearings properly. (Bearings must be assembled with the shield facing
outwards).
6.1.1.5 Press oil seals (9) into worm recesses in shell housing (1) with the sealing members pointing
inwards.
6.1.1.6 When re-assembling the worm gear and load bearings ensure that the bearings are fitted so that
the plate with the smallest bore size fits over the worm gear spigot.
6.1.1.7 The shell cap should be fitted after the worm shaft assembly has been securely clamped and with
the worm gear assembly in position. Tighten the shell cap until a slight drag is felt on rotating the
worm shaft by hand.
6.1.1.8 For anti-backlash actuators the shell cap must be screwed up with the lifting screw inserted and
only as tight as to allow the required backlash and lifting screw and worm gear. For normal screw
jack operation the recommended backlash is 0.05mm (0.002”).
6.1.1.9 Tighten shell cap grub screw (18). It may be necessary to fit a new thread grip if it has become
worn due to numerous adjustments.
6.1.1.10 For keyed actuators it is recommended that the lifting screw be threaded into the worm gear as far
as required before fitting the key (28).
6.1.1.11 It is important that the detachable ends are securely fixed to the lifting screws and the following
procedure should be adhered to.
6.1.2 Instructions for fitting detachable ends on lifting screws.
6.1.2.1 Thread the detachable end on to the lifting screw and tighten up as hard as possible without
damaging the components.
6.1.2.2 Select a twist drill, which is a free fit in the tapped holes of the
detachable end. Using these holes as a drill guide, drill dimple only into
the lifting screw. Clean out swarf and remove detachable end. Select
another drill which matches the set screw diameter and, using the drill
dimples as a guide, drill into the lifting screw a full diameter depth of
1mm below the root diameter of the threads. Refit detachable end.
6.1.2.3 Fit the knurled point set screws (supplied with detachable ends) firmly in
place ensuring that point of set screws make contact with bottom of drill
dimples. Secure the set screws with Loctite.
6.1.2.4 If actuators with keyed lifting screws are involved, and it is required to line up the clevis flats or top
plate holes, etc. in a fixed relationship to the worm shaft centreline, it will be necessary to face the
underside of the detachable end to obtain the required relationship. This operation should be done
carefully as only a few hundredths of a mm (thousands of an inch) removed from the attachment is
equivalent to a fair amount of rotational movement.
1mm
deep
drill
holes