Seametrics TX800-Series User Manual
Page 9
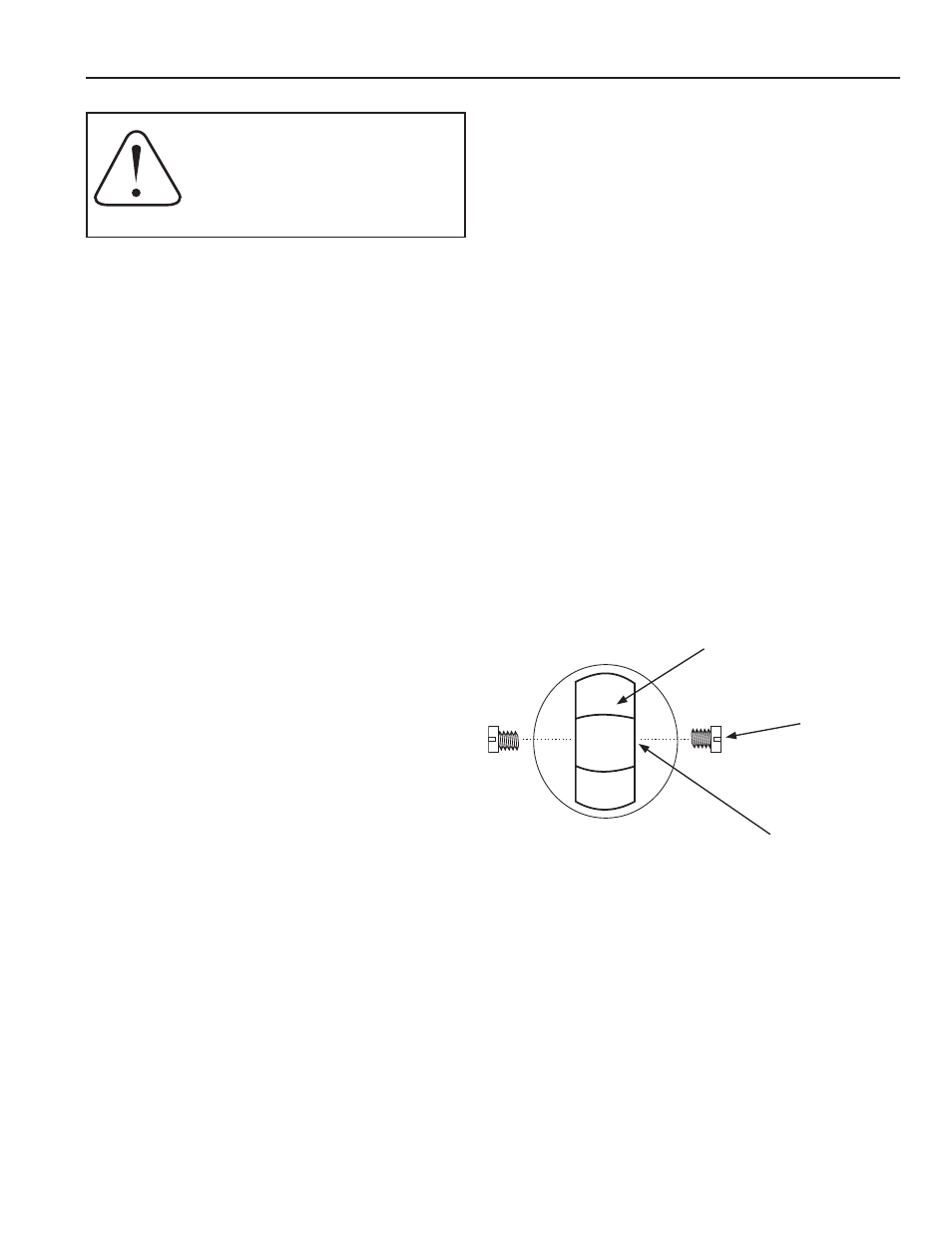
Sensor Replacement.
It is very unusual for a sensor to re-
quire replacement in normal use. The primary cause of sensor
failure is overvoltage (inadvertent connection of line voltage,
for example) or incorrect polarity on hookup. The sensor is
replaced by removing the strain relief, then threading out
the sensor retainer plug. Remove the entire sensor capsule
by pulling on the cable. The new sensor capsule can then be
installed, orientation is not critical. Replace the retainer plug,
and then replace and tighten the strain relief.
Rotor Replacement.
It is unusual for a rotor to require
replacement due to damage sustained in normal service.
More commonly, the meter is dropped while it is out of the
pipe. Another reason for rotor replacement is shaft wear
after long service. Rotors are easily field-replaced.
To install a rotor, follow these steps:
1. Unscrew the threaded bearing housings to expose
the shaft ends. If bearings are being replaced,
back them completely out.
2. Remove the rotor. Put the new rotor in its place.
3. Thread in one bearing housing part way, then the
other. Take care to start the end of the shaft into
the bearing hole before tightening further.
4. Screw in bearing housings until they bottom.
Note: Do not use excessive force.
5. Check for free spin. Blowing lightly on the rotor
should result in it spinning rapidly and coasting to a
smooth stop.
Caution:
Never remove the u-clip retainer
when the pipe is under pressure. Always
remove pressure from the pipe before at-
tempting to remove the meter. Removal
under pressure may result in damage or
serious injury.
MAINTENANCE
Page 7
Signal Troubleshooting.
The flow sensor has only one moving
part, the rotor. If this is turning properly and there is no signal,
the magnetic sensor is not operating properly. To check the
signal, apply 12 Vdc regulated* power to the red (+) and black
(-) leads. Set a multimeter to voltage reading. Put the positive
multimeter lead on the red wire and the negative lead on the
white wire. Slowly turn the rotor. Voltage reading should swing
between +12 Volts and 0 Volts as the rotor turns. If it does
not, the solid-state magnetic sensor is not working properly.
Checking for continuity is not a useful test of these sensors.
*NOTE: An unregulated power supply can exceed max voltage of
micro powered sensor (gray cable) and damage sensor.
Rotor Replacement
Shaft
Turbine Rotor
Bearing
Housing