Cashco 1049 User Manual
Page 4
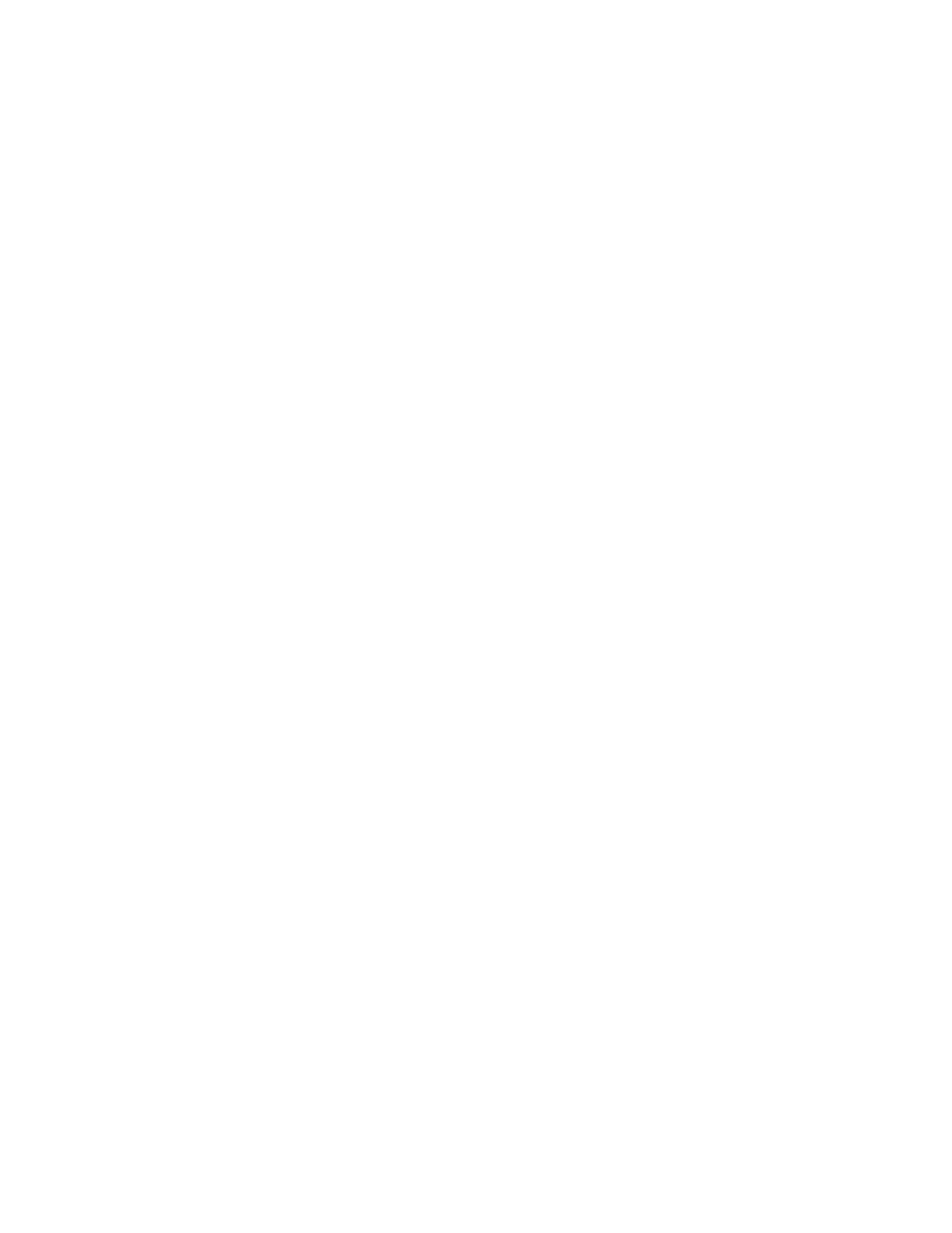
4
IOM-1049
sectIon IV
IV. START-UP
Operation of the Model 1049 is automatic once the set
pressure has been set. (The set pressure is bench-set
per the customer’s specified setting at the factory prior
to shipment.) note: The set pressure is defined as
the pressure at which the valve should start to open on
increasing tank pressure.
To adjust the set pressure, remove the hex cap at the
top of the valve and loosen the jam nut around the
adjusting screw. Clockwise rotation of the adjusting
screw will increase the set pressure. Counter clockwise
rotation will decrease the set pressure. Do not adjust
the set pressure beyond the nameplate range. Tighten
the jam nut after adjustments are made and replace
the hex cap.
For the valve to be in the closed position, tank pressure
must reach the actuator though the pilot.
Upon initial start-up, the vave may be opened for a
few seconds, but will close when the pressure in the
actuator chamber reaches tank pressure.
For valves with air or nitogen assist pilot, the gas source
must be connected to the filter regulator before the
valve will be in the closed position. (The filter regulator
is pre-set at the factory to 5 psig, and the CA-1 back
pressure regulator is pre-set at the factory to 10 psig.)
sectIon V
V. MAINTENANCE
It is strongly recommended that if the valve needs to
be serviced, that it be sent to the factory or a factory
authorized repair facility. Trained mechanics with
specialized test equipment will ensure that the valve is
accurately set.
The Model 1049 should be periodically checked to
ensure proper operation. The frequency required
depends on the severity of the service conditions. At
least once a year is recommended.
To disassemble the valve, refer to the appropriate
drawings.
to replace soft goods of the pilot valve:
The pilot valve body maybe removed by unscrewing
the item 131 nipple from the item 201 upper case
weldment.
To disassemble the diaphragm case, relax the
compressed spring by first unscrewing the item 105 cap,
then loosen the item 114 jam nut and back off the item
113 adjusting screw. The ring of item 109 nuts, item
110 lockwashers, item 121 washer, and item 120 bolts
around the periphery can now be removed. Remove
item 120 bolts and item 110 lockwashers, holding
items 104 spring bonnet and 102 upper diaphragm
case together. Replace item 1 round gasket and
reassemble items 102, 104, 110 and 120.
Remove item 115 set pressure spring, 112 spring button,
and 134 ring gasket and set to the side. Hold the item
18 wrenching washers with a wrench, and loosen and
remove item 109 nut. Remove items 110 lockwasher,
111 lower spring guide washers, 18 wrenching
washers, 106 support plates, 107 diaphragm, 126 bolt
gaskets, and 17 spacer and set to the side. Remove
item 110 lock washer and item 120 bolt from item 101
pilot body and 103 lower diaphragm case. Remove
items 124 seal diaphragm, item 125 body gasket and
108 spindle assembly. Take items 133 o-ring seat and
item 126 bolt gasket off item 108 spindle assembly and
replace with new parts.
Reinstall item 108 spindle assembly with items 133
o-ring and 126 bolt gasket. Set new item 124 seal
diaphragm over the stem of the spindle assembly and
item 125 body gasket on top of the item 124. Then,
reinstall the item 103 lower diaphragm case to the
item 101 pilot body with item 110 lock washer and item
120 bolt. Slide item 127 spacer over the stem of the
spindle assembly and place another new item 126
bold gasket on top of the spacer. Place the first item
106 support plate on the stem, then the new item 107
diaphragm, then item 126 bolt gasket , then the final
item 106 support plate. Place the items 18 wrenching
washers, 111 lower spring guide washers, and 110
lockwasher on the stem. While holding the item 128
wrenching washers with a wrench, (and making sure
the bolt holes of the diaphragm and diaphragm case
align) thread the item 109 nut and tighten. Place items
115 set pressure spring and item 112 spring button on
item 108 spindle assembly. Place new item 134 ring
gasket on top of the item 107 diaphragm. Place the
item 102 upper diaphragm case on top of item 103