Bjm pumps, llc – BJM Pumps TIGF32-9NL User Manual
Page 4
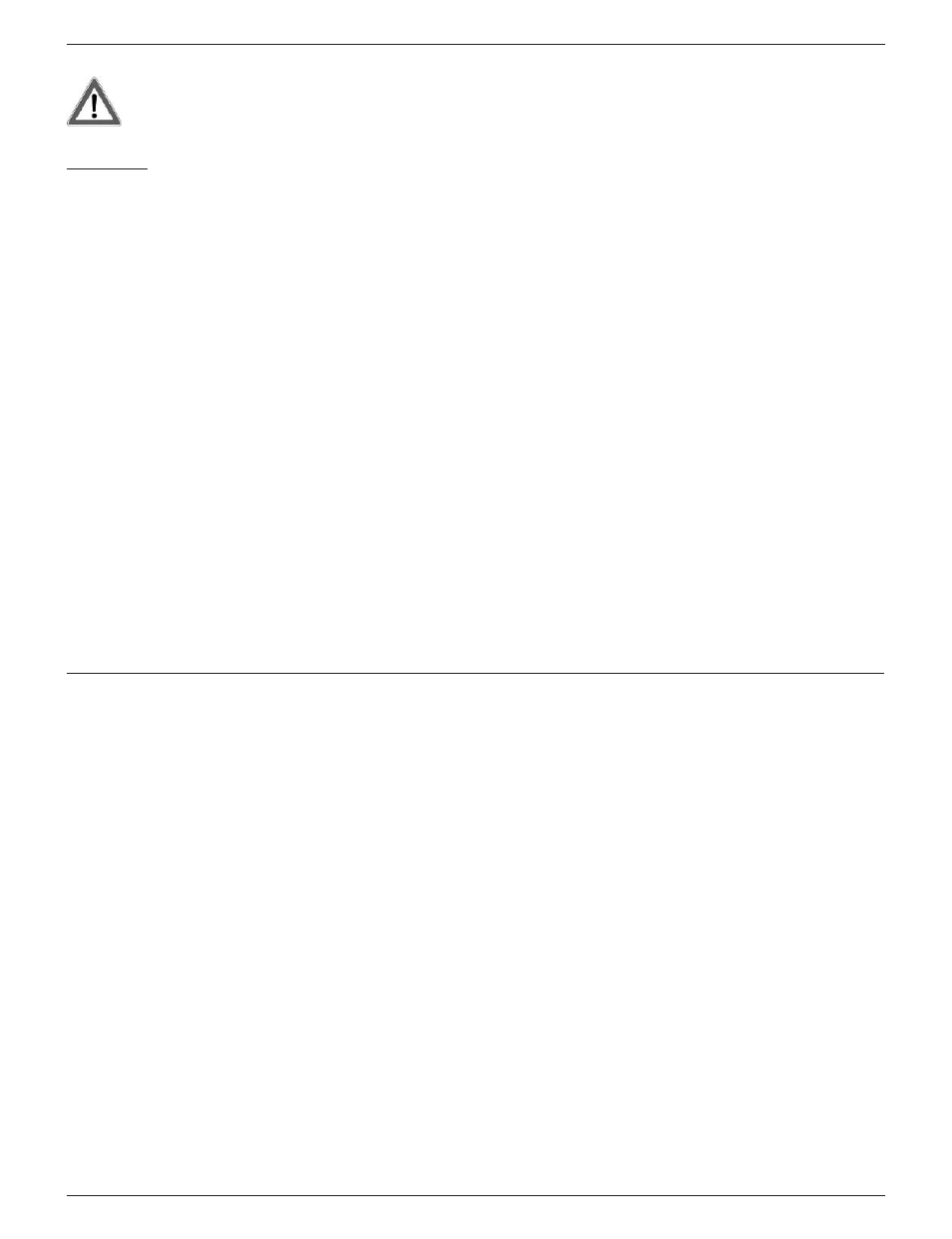
BJM Pumps, LLC warrants each new pump against defects in workmanship and material for the period of 90 DAyS. It will replace or repair
for the original purchaser, any genuine parts found to be defective upon return to its factory at CT (or other place as designated by it), trans-
portation prepaid by purchaser. The labor involved in replacing defective parts is not warrantable. Other equipment and accessories are war-
ranted only to the extent of the original manufacturer’s warranty. This warranty does not cover any pump which has been damaged due to ca-
reless handling, improper use or application, improper power supply, use in unsuitable liquids, or faulty installa tion. Alteration or repair by other
than BJM Pumps, LLC (or designated service facility) voids this warranty.
BJM Pumps, LLC assumes no liability for damages, losses, inconveniences, direct, or consequential, any kind in respect to the use or ope-
ration of the pumps or any equipment or accessory used in connection herewith.
This warranty encompasses the entire understanding between the purchaser and BJM Pumps, LLC and no other person is authorized to ex-
tend or alter the terms of the warranty. This warranty is effective only when the warranty certificate card is properly completed and returned
to BJM Pumps, LLC at the time of purchase.
BJM Pumps, LLC
KeeP FOR yOUR ReCORDS
Date Purchased:_________________________________________________________________
Model: _____________________Serial No.: __________________________________________
Dealer Name: ___________________________________________________________________
BJM PUMPS, LLC
123 Spencer Plain Rd., P. O. BOX 1138
Old Saybrook, CT 06475
TeL. (860) 399-5937, FAX (860) 399-7784
http://www.bjmpumps.com
O
rd
er
-N
r.
09
9-
15
6
07
/2
01
3
Perfecta Pump is a registered trademark of BJM Pumps, LLC
ALWAYS DISCONNECT PUMP FROM
ELECTRICAL SOURCE BEFORE SERVICING!
NOT FOR USE IN FLAMMABLE LIQUIDS!
IMPORTANT: IN ANY CORROSIVE ENVIRONMENT, CONSULT
FACTORY OR YOUR DISTRIBUTOR BEFORE INSTALLATION OR
USE.
TROUBLE SHOOTING
Pump shuts off:
Adjust float switch
Check impeller for free rotation and clogging
Check pump passage, hose or pipe for kink or clog.
Pump is heating up:
Check impeller for free rotation
Check voltage
Pump performance low:
Check for blockage
Check impeller for excessive wear
SERVICE:
Tools needed
Phillips screwdrivers (#1 and #2), locking pliers, 10 mm and 17
mm wrench, ball bearing puller.
A. Disassembly of pump top.
(Check wires, rotor, stator, ball bearings and oil). Remove (pos 39)
handle screws (pos 4). Remove handle. Remove (pos 37) top
cover screws (pos 2) and open top cover. Disconnect wires,
remove motor housing cover (pos 3). Inspect the quality of the oil.
If milky or whitish in color, check seals and replace (both seals and
oil) if necessary. To remove rotor, ball bearings and seals, follow
steps described in B. Disassemble pump bottom before
proceeding. Once impeller is off, pull out rotor. Inspect bearings,
replace if necessary. Press out lip seals. Inspect and replace as
necessary.
B. Disassembly of pump bottom
(strainer, suction cover, impeller) Remove strainer screws (pos
36), remove strainer (pos 6) and suction cover (pos 7). Hold
impeller with vise grip and remove impeller screw (pos 40).
Remove impeller (pos 5). Impeller vanes should have sharp
edges to maximize performance. Replace impeller if vanes are
rounded or dull.
Inspection of pump bottom parts.
Look at lower lip seal parts (pos 27) for visible wear. If damaged
or worn replace both lip seals. To replace lip seals, disassemble
top portion of pump first and remove the oil (see A., disassembly
of pump top).
Note: Both seal openings should face down.
C. Important notes on re-assembly of pump
All O-rings should be lubricated with a silicone based grease, or
lubricated with same oil as in motor, before assembly. Replace
ball bearings to shaft. To re-install inner cover, lubricate bearing
holder. Use a plastic or rubber mallet to lightly tap until cover is in
place. It is important that the bearing is in the absolute center of
the bearing holder when closing the top cover. If not centered, the
shaft will not turn freely.