Caution, Warning – EBARA EFQU4 User Manual
Page 17
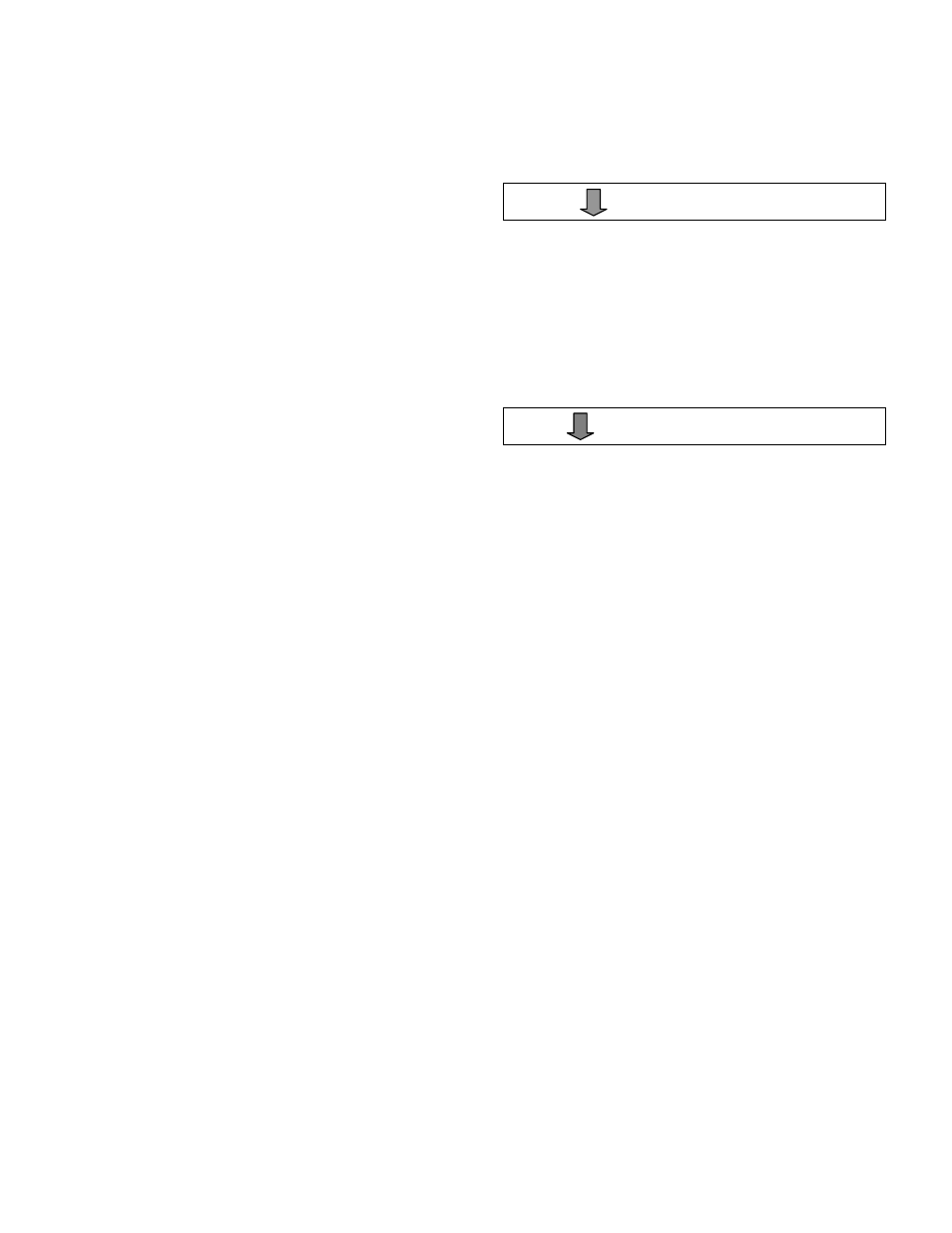
EBARA Fluid Handling
16
Strainer Check
If a suction strainer has been shipped with the
pump or installed by the user, check the strainer
regularly, and clean it as necessary. The strainer
should also be checked if pump flow rate begins
to drop. If a vacuum suction gauge has been
installed, monitor and record the readings
regularly to detect strainer blockage.
Never introduce air or steam pressure into the
pump casing or piping to remove a blockage. This
could result in personal injury or damage to the
equipment. If back flushing is absolutely
necessary, liquid pressure must be limited to 50%
of the maximum permissible operating pressure
show on the pump performance curve.
Pump Vacuum Check
With the pump inoperative, install a vacuum
gauge in the system, using pipe dope on the
threads. Block the suction line and start the pump.
At operating speed the pump should pull a
vacuum of 20 inches (508,0mm) or more of
mercury. If it does not, check for air leaks in the
seal, gasket, or discharge valve.
Open the suction line, and read the vacuum
gauge with the pump primed and at operation
speed. Shut off the pump. The vacuum gauge
reading will immediately drop proportionate to
static suction lift, and should then stabilize. If the
vacuum reading falls off rapidly after stabilization,
an air leak exists. Before checking for the source
of the leak, check the point of installation of the
vacuum gauge.
STOPPING
Never halt the flow of liquid suddenly. If the liquid
being pumped is stopped abruptly, damaging
shock waves can be transmitted to the pump and
piping system. Close all connecting valves slowly.
On engine driven pumps, reduce the throttle
speed slowly and allow the engine to idle briefly
before stopping.
CAUTION!
If the application involves a high discharge head,
gradually close the discharge throttling valve
before stopping the pump.
After stopping the pump, lock out or disconnect the
power source to ensure that the pump will remain
inoperative.
WARNING!
Do not operate the pump against a closed
discharge throttling valve for long periods of
time. If operated against a closed discharge
throttling valve, pump components will
deteriorate, and the liquid could come to a boil,
build pressure, and cause the pump casing to
rupture or explode.
Cold Weather Preservation
In below freezing conditions, drain the pump to
prevent damage from freezing. Also, clean out any
solids by flushing with a hose. Operate the pump
for approximately one minute; this will remove any
remaining liquid that could freeze the pump
rotating parts. If the pump will be idle for more than
a few hours, or if it has been pumping liquids
containing a large amount of solids, drain the
pump, and flush it thoroughly with clean water. To
prevent large solids from clogging the drain port
and preventing the pump from completely draining,
insert a rod or stiff wire in the drain port, and
agitate the liquid during the draining process.
Clean out any remaining solids by flushing with a
hose.
BEARING TEMPERATURE CHECK
Bearings normally run at higher than ambient
temperatures because of heat generated by
friction. Temperatures up to 160º F (71º C) are
considered normal for bearings, and they can
operate safely to at least 180º F (82º C).