AAON RK Series User Manual
Page 12
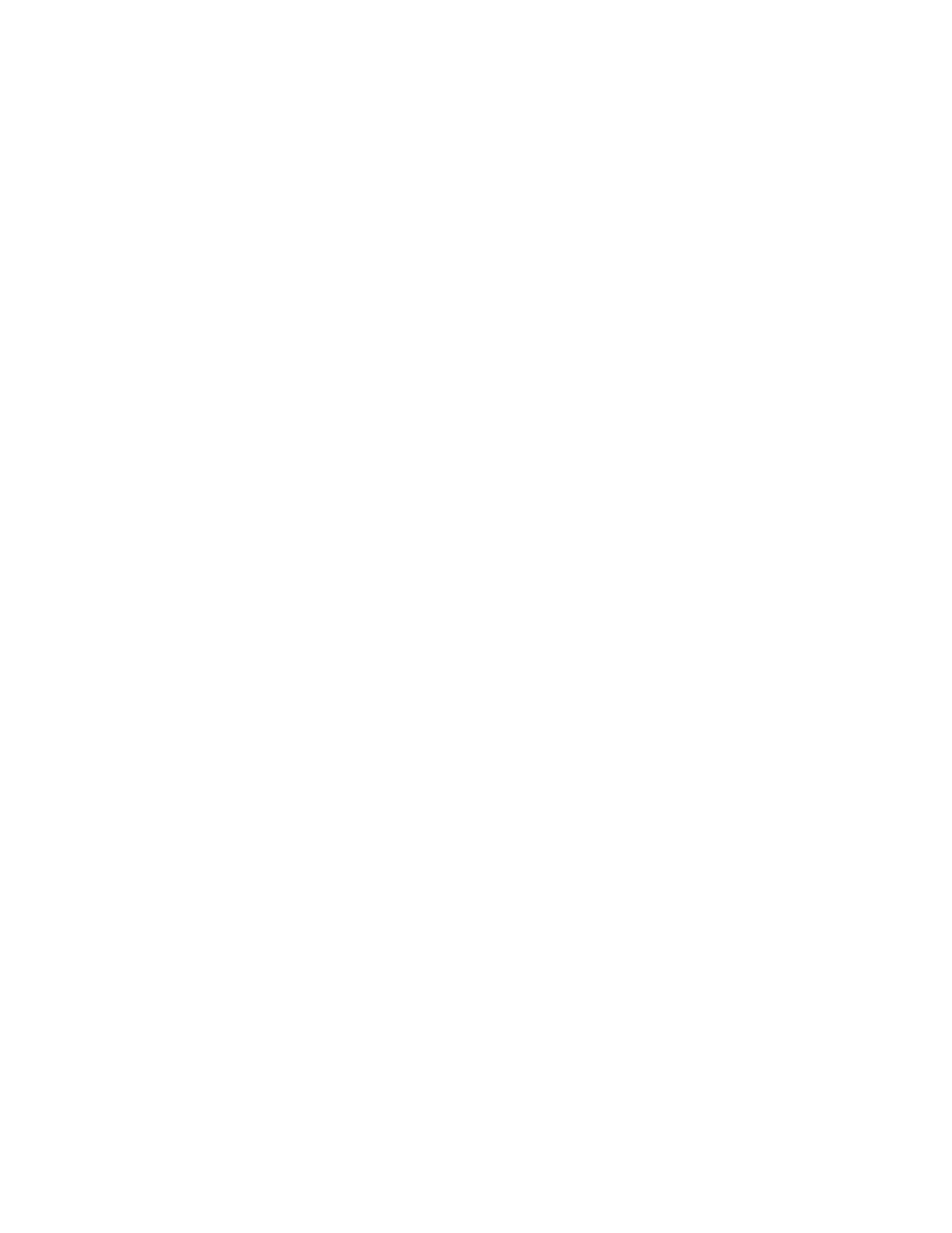
12
2. Take “return” air (air to be exhausted after
recovering energy from it) from the occupied zone,
not from areas containing a high concentration of
dusts or aerosols such as the hood.
If necessary, provide supplemental filtration of the
return air at the inlets to the duct system. The goal of
the dilution ventilation is to preserve a healthful and
comfortable environment in the breathing zone. Supply
and return diffusers and grilles should be located to
achieve this end. Ceiling returns located directly above
machinery can provide additional benefits by directing
contaminants away from operators. In the industrial
application this air may contain high levels of aerosols,
which, once deposited and dried, would be difficult or
impossible to clean from ductwork, fans, dampers and
wheels. Therefore a filter of appropriate efficiency is
recommended to be installed at the inlet or “return
grille”.
Experience in industrial applications from small
facilities to large factories has shown that when these
two recommendations are observed, successful
application of energy recovery and its attendant
benefits is the result. On the other hand, ignoring
these common sense rules can result in reduced
satisfaction and/or equipment damage and a
maintenance challenge.
Cross Leakage in Energy
Recovery Ventilation Systems
The issue of cross leakage in rotary wheel based
Energy Recovery used in space conditioning
applications is often misunderstood. As a result, many
systems are installed with purge sectors and the
additional fan capacity required to allow these sectors
to function when in fact they are unnecessary.
Understanding the rationale for the purge sector, its
history, its added first cost, and the associated
continuing cost of operation, the designer will rarely
specify purge.
A purge sector minimizes the carry over cross leakage
from exhaust into the supply airstream by shunting a
portion of the supply air back into the exhaust
airstream across the seal separating the exhaust and
supply. This is required for industrial process
applications where the exhaust contains contaminants
which would be detrimental to the process.
(Historically, heat wheels have been used primarily for
dehumidification and process heat recovery.) The
volume of air required for effective purge is listed at
10% to 20% of rated flow by manufacturers of
industrial process wheels. In addition to the cost of
providing the sector, the system must move 10 to 20%
more air than is required by the application in order to
purge.
By contrast, in space conditioning applications, where
the ventilation system is operating to maintain
acceptable indoor air quality, there should be no
contaminants in concentrations of concern. Cross
leakage in the energy recovery system results in a
small amount of the exhaust air, typically less than 5%
for wheels operating in balanced flow, returning to the
space from which it came. This is not “contamination”
as it is often labeled. It is air that effectively never left
the space. The operating cost of moving this air is far
less than that required to operate purge sector.
This amount of cross leakage is appropriate to
handling bathroom exhaust in an environment where
continuous exhaust of the restroom achieves an air
quality on a par with the adjacent space. It is not
appropriate for recovering energy from toxic
environments, laboratory fume hoods, operating
rooms, etc. These are not recommended applications
for rotary based technology without a purge sector.
In fact, many of these environments should not
tolerate any cross leakage and as such should not
utilize rotary technology as even well designed purge
sectors do not achieve zero cross leak.
If energy recovery is required in these environments, a
“run around loop” approach is suggested.
The adjustable mechanical purge is capable of
reducing cross leakage to a fraction of one percent.
Nevertheless, purge should only be specified based on
an engineering evaluation of the cost to provide, the
cost to operate and the specific needs of the
application.
Moisture Transfer and Fungal Growth in Desiccant
Based Enthalpy Wheels
There is evidence that fungi germinate when water
condenses onto surfaces of air handling systems
where nutrients are present. Surfaces which remain
wet for a period of 12 to 24 hours allow fungi and mold
spores already present to “bloom”, resulting in a
potential IAQ problem.
This knowledge has led to questions of whether
desiccant energy recovery ventilation wheels, which in
fact transfer water from one airstream to another,
could provide a medium for growth of mold and fungi.
Such is not the case for AAONAIRE® technology, nor
has it been reported in the literature for other enthalpy
wheels.
In silica gel based desiccant wheels, the water
molecules are transferred by sorption, individually,
onto and off of the silica gel surface. Water is present
on the wheel in a molecular layer only. Condensation
does not occur. AAONAIRE® desiccant wheels
experience “dry” moisture transfer in that there is no