Periodic maintenance and inspection schedule – GEARENCH BDA100 PETOL Tubing Elevator User Manual
Page 8
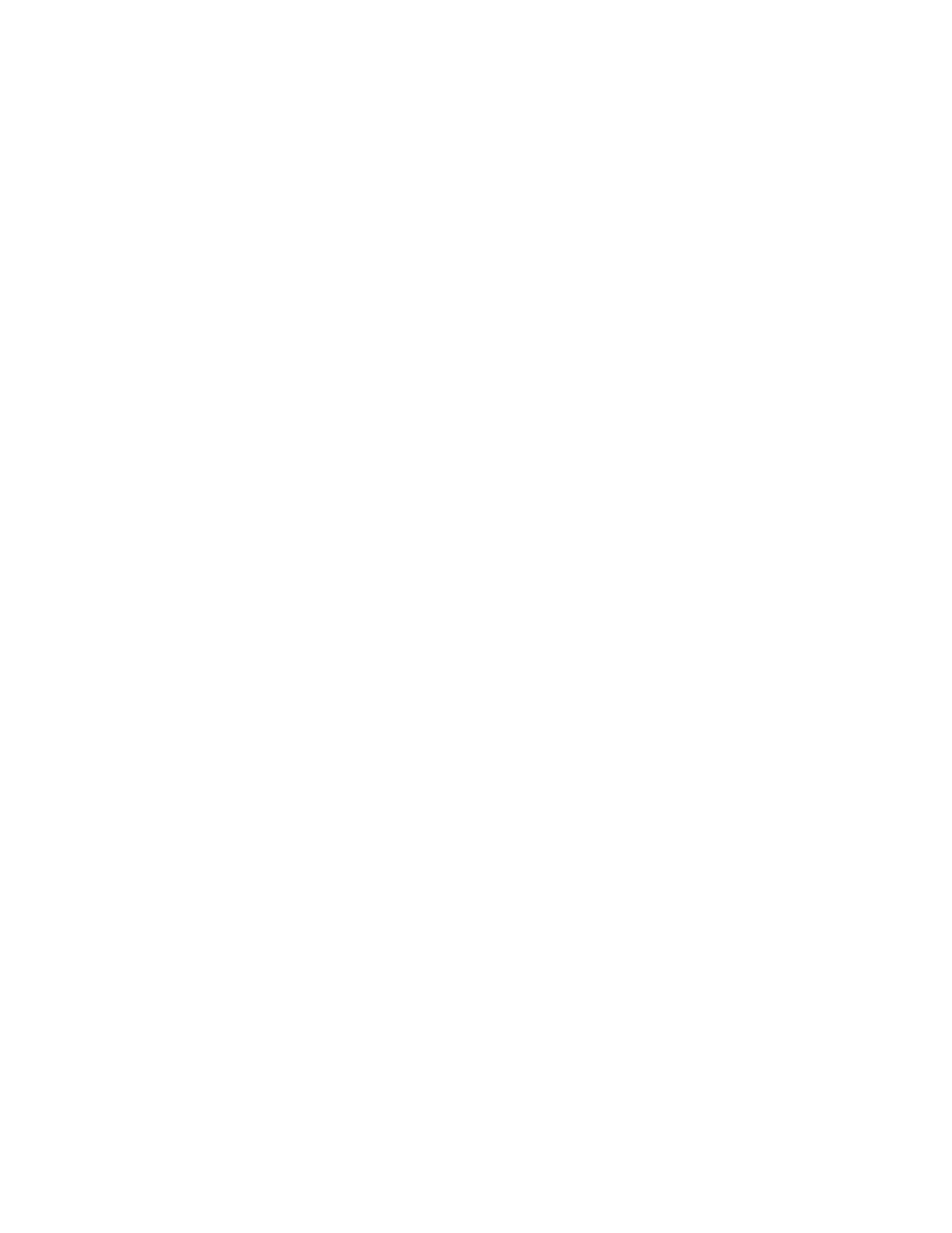
6
Periodic Maintenance and Inspection Schedule
Daily
1. Visually inspect elevator for signs of corrosion or damaged components.
2. Inspect for any visual evidence of external cracks. Visible cracks indicate potential
failure points, and if they are discovered, the elevator should be immediately removed
from service.
3. Examine link support arm surfaces for deformation. If the surfaces are excessively
worn, the elevator needs repair. (See ‘Inspection Wear Limits’ for maximum
allowable wear)
4. Test the operation of the elevator latch mechanism. If the Lock or Retainer appears to
be too loose or too restricted, repair may be required.
5. Do not grind or remove metal from any surface of the elevator. Contact
GEARENCH™ for all suspected damage and repair.
6. Proper lubrication involves greasing the hinge and retainer pins through their grease
fittings. The lock pin should be oiled to maintain smooth operation.
7. After use, clean elevator. Remove all external dirt and grease.
Semi-annually
1. Perform Daily Maintenance as required.
2. Inspect the following areas for wear and/or damage (See ‘Inspection Wear Limits’ for
maximum allowable wear):
a. Bore
b. Hinge Pin and Hinge Pin Hole
c. Retainer Pin and Retainer Pin Hole
d. Lock Pin and Lock Pin Hole
e. Lug
Annually
1. Perform Daily Maintenance as required.
2. Perform Semi-annual Maintenance as required.
3. Conduct NDT inspection (Magnetic Particle Inspection recommended) of all primary-
load-carrying components (Left and Right Bodies, Retainer, Hinge Pin, and Retainer
Pin) for cracks. If any cracks are discovered, contact GEARENCH.
4. Load test at full capacity (200,000 lbs) for five minutes. All tests should be logged
and filed with original purchase order paperwork.
NOTE: The BDA100 is a load bearing tool that is manufactured from alloy steel and
heat treated to strict standards. Only welding to repair a worn bore is allowed provided
that the welding is performed by a qualified welder using a qualified process for AISI
4318 material with a minimum strength of 110 ksi. Welding of the bore constitutes
remanufacture and all testing shall be performed in accordance with API RP8B Any
unauthorized welding repairs on the BDA100 will void both the warranty and the load
rating.