Gorman-Rupp Pumps SF6C All serial numbers User Manual
Page 34
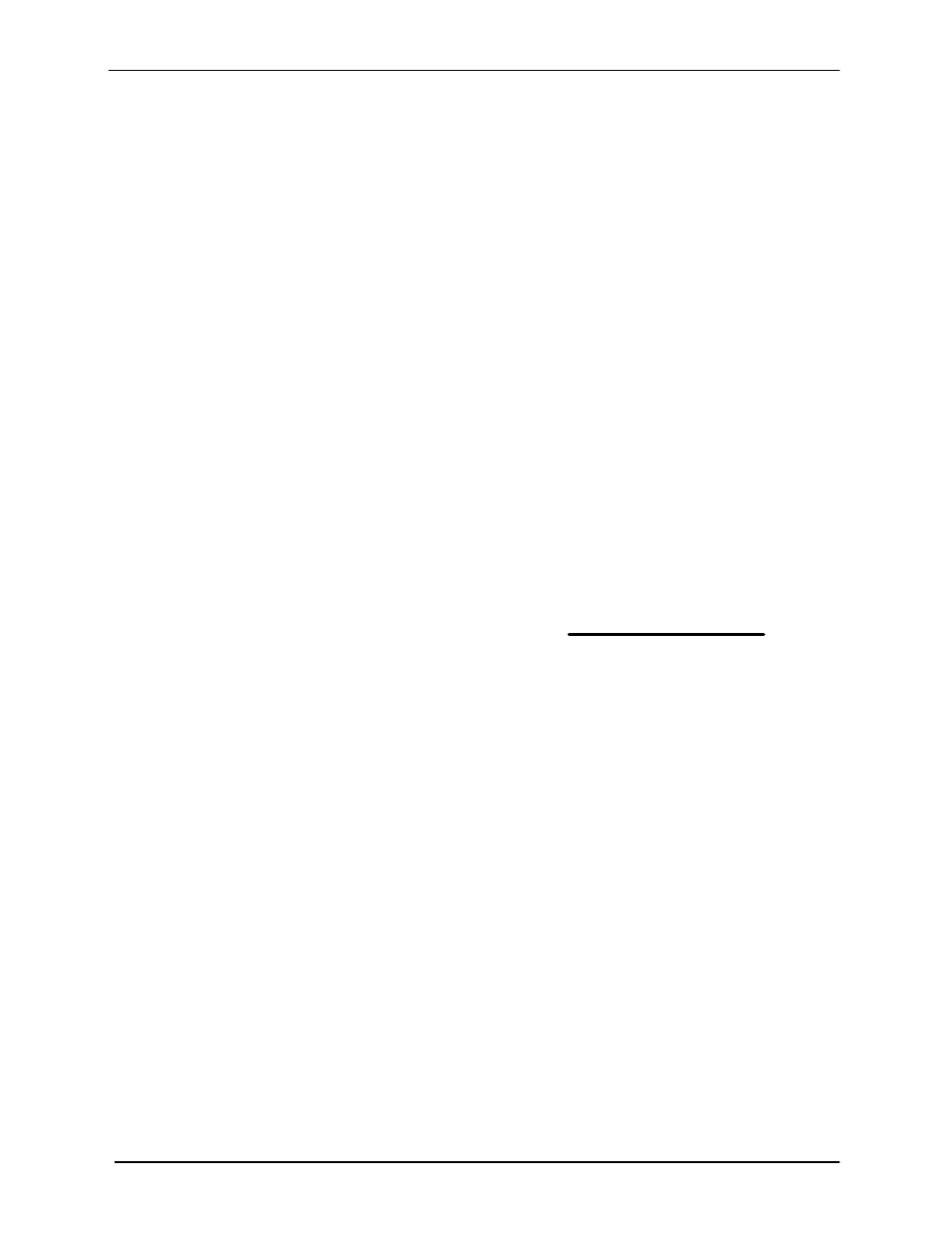
OM-06604
SF SERIES
PAGE E - 11
MAINTENANCE AND REPAIR
Position the intermediate so the holes for the
mounting hardware in the intermediate align with
those in the motor housing and press the inter
mediate into the motor housing until fully seated.
Apply “Never‐Seez” or equivalent compound on
the threads of the capscrews (12) and secure the
intermediate to the motor housing with the hard
ware (11 and 12). Torque the capscrews to 47 ft.
lbs. (6,5 m. kg.).
Subassemble the O‐ring onto the stationary seat.
Position this subassembly in the intermediate bore
with the sealing face up and cover the seal face
with a clean tissue. Use your thumbs to press the
assembly into the bore. Apply equal pressure on
opposite sides until the seat contacts the bore
shoulder. Remove the tissue and inspect the seal
face to ensure that it is clean and dry. If cleaning is
necessary, use clean tissue to wipe lightly in a cir
cular pattern.
Unpack the rotating portion of the seal. Be certain
the seal face of the rotating element is free of grit or
surface damage. Because the rotating element
may not stay in the bellows retainer when turned
upside down, place a small amount of grease at
equal spaces on the back of the element and posi
tion it in the bellows retainer. The grease should
hold the element in position until the seal is in
stalled. Assemble the drive grooves of the rotating
element into the drive lugs of the bellows retainer.
Lubricate the I.D. of the bellows with water and
slide the rotating subassembly onto the rotor shaft
until the seal faces contact.
Slide the seal spring over the shaft and bellows re
tainer and install the spring centering washer. In
stall the seal retaining ring (10). See Figure E-3 for
the proper order of seal assembly.
Lower Seal Installation
(Figures E-1 and E-3)
Thoroughly clean the O‐ring surfaces and seal
bore of the seal plate (21). The seal bore must be
free of burrs and nicks which could damage the
seal. Inspect the seal plate for cracks, distortion, or
erosion and replace it if defective.
Lubricate the seal sleeve O‐ring (24) with light oil
and slide it onto the rotor shaft until it is seated
against the shaft shoulder. Use caution not to nick
or damage the O‐ring on the shaft keyway.
Position the seal plate on a clean flat surface with
the impeller side up.
Unpack the seal stationary seat and O‐ring. Apply
a light coating of oil to the seal plate bore and the
O.D. of the stationary seat O‐ring. Keep the sealing
face dry.
Position the stationary seat and O‐ring in the seal
plate bore with the sealing face up and cover the
seal face with a clean tissue. Use your thumbs to
press the assembly into the bore. Apply equal
pressure on opposite sides until the seat contacts
the bore shoulder. Remove the tissue and inspect
the seal face to ensure that it is clean and dry. If
cleaning is necessary, use clean tissue to wipe
lightly in a circular pattern.
NOTE
If the seal plate was not removed during disassem
bly, cover the stationary element with a clean tissue
and use your thumbs to press the seal stationary
seat and O‐ring into the seal plate as described
above. Remove the tissue and inspect the seal face
to ensure that it is clean and dry.
Install a new O‐ring (10) on the shoulder of the in
termediate (8, Figure E-2).
Carefully position the seal plate and stationary seal
components on the rotor shaft. Align the holes in
the seal plate for the capscrews (22) with those in
the intermediate and slide the seal plate onto the
shaft until fully seated against the intermediate. Be
careful not to damage the stationary seat already
installed in the seal plate. Apply “Neverseeze” or
equivalent compound to the threads of the caps
crews (22). Secure the seal plate to the intermedi
ate by torquing the capscrews to 3.3 ft. lbs. (637 in.
lbs. or 0,45 m. kg.).
Unpack the rotating portion of the seal. Be certain
the seal face of the rotating element is free of grit or
surface damage. Because the rotating element
may not stay in the bellows retainer when turned
upside down, place a small amount of grease at
equal spaces on the back of the element and posi
tion it in the bellows retainer. The grease should
hold the element in position until the seal is in
stalled. Assemble the drive grooves of the rotating
element into the drive lugs of the bellows retainer.