Gorman-Rupp Pumps PAH4B60-QSB4.5P 1526774 and up User Manual
Page 44
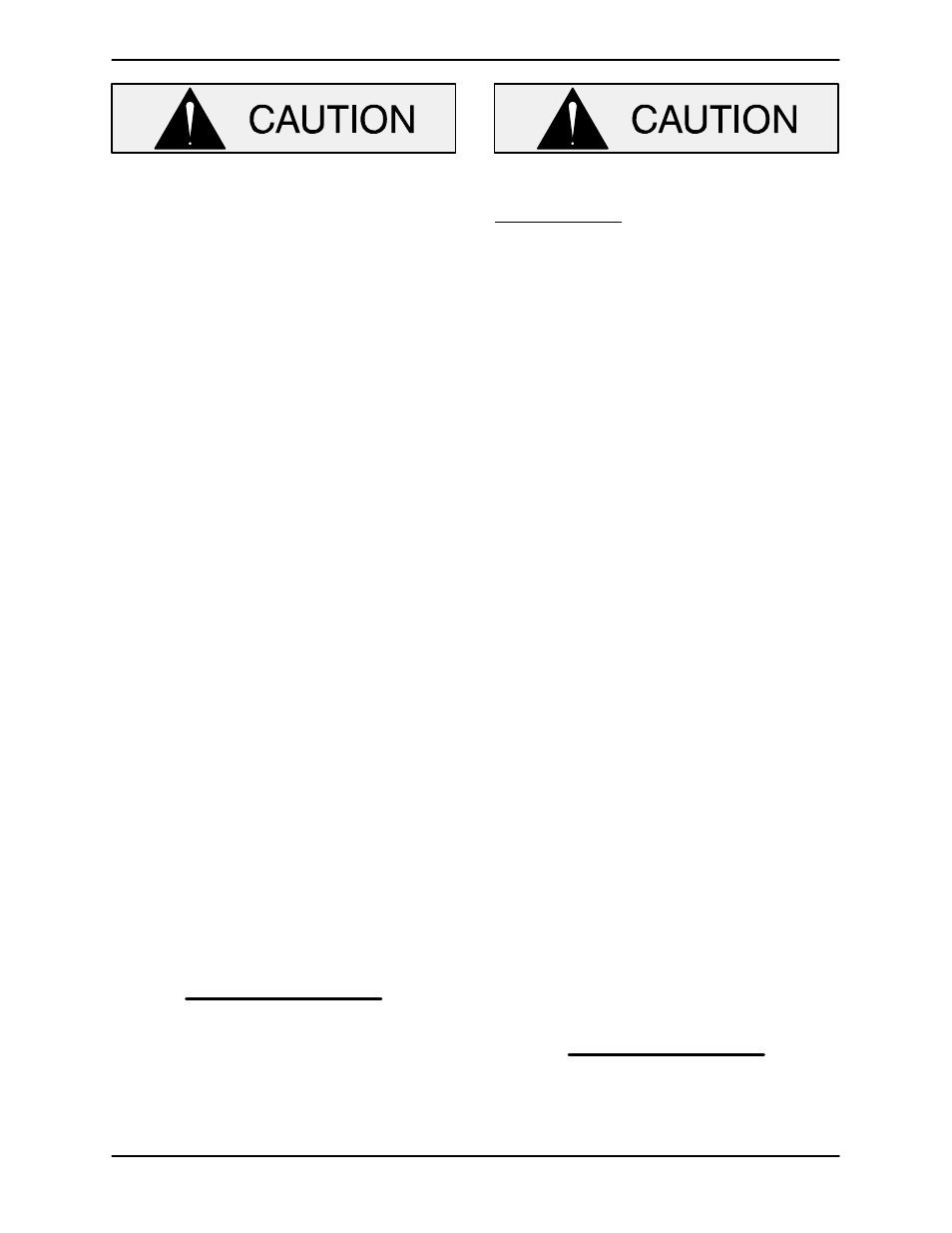
PAH SERIES
OM-06609
MAINTENANCE & REPAIR
PAGE E - 22
When installing the shaft and bearings into
the bearing bore, push against the outer
race. Never hit the balls, rollers or cages.
Apply a light coating of oil to the lip of the outboard
oil seal (12) and press it into the pedestal with the
lip positioned as shown in Figure 6. The face of the
oil seal should be just flush with the outer face of
the bearing cap.
Apply a light coating of oil to the lip of the oil seal
(20) and press it into the drive flange (21) with the
lip positioned as shown in Figure 6. The oil seal
should be centered in the flange bore.
Install the gasket (17) and slide the assembled
drive flange and oil seal over the impeller shaft. Use
caution not to cut or roll the lip of the oil seal (20) on
the shaft keyway. Secure the drive flange to the
pedestal with the hardware (15 and 16). Torque the
capscrews (16) to 41 ft. lbs. (5,7 m. kg.).
Lubricate the bearings as indicated in LUBRICA
TION at the end of this section.
Securing Pedestal And Drive Assembly To
Engine
(Figure 9)
Install the shaft key (28, Figure 6) in the shaft key
way. Position the flexible portion of the coupling as
sembly (3) on the shaft as shown in Figure 9.
NOTE
The flexible portion of the coupling must be proper
ly positioned on the shaft. The heads of the caps
crews in the center of the coupling must be posi
tioned away from the pump.
Align the keyway in the bushing (2) with the shaft
key, and slide it onto the shaft until the face of the
bushing is just flush with the end of the shaft. Ro
tate the flexible portion of the coupling until the
tapped holes for the two setscrews align with those
in the bushing, and install the setscrews.
Make certain that the flexible portion of the
coupling is mounted as shown in Figure 9.
This is critical. If the coupling is not prop
erly positioned on the shaft, the coupling
parts may not fully engage, or a pre‐load
condition can cause premature bearing
failure.
The end of the shaft must be extend 0.44
inch (11 mm) from the face of the bush
ing. This will allow the two portions of the
coupling to fully engage when the engine
bracket is secured to the engine bellhous
ing without pre‐loading the bearings.
With the flexible portion of the coupling and the
bushing properly positioned on the shaft, tighten
the two setscrews in an alternating sequence until
the bushing and coupling are fully secured. Torque
the setscrews to 23.3 ft. lbs. (430 in. lbs. or 0,31 m.
kg.).
If the complete coupling assembly is being re
placed, apply `Loctite Retaining Compound No.
242' or equivalent to the threads of the hardware (4
and 5) and secure the outer ring of the coupling to
the engine flywheel by torquing the hardware to 45
ft. lbs. (6,2 m. kg.).
Using a suitable lifting device, position the as
sembled drive and rotating assembly so the flex
ible portion of the coupling seats inside the outer
ring attached to the engine flywheel.
NOTE
To ease installation, lightly lubricate the rubber por
tion of the coupling with a non‐petroleum based
lubricant such as vegetable oil or glycerin, or a sili
con‐based lubricant such as “WD40” or equivalent.
Do not use petroleum‐based lubricants, or any oth
er substance which may soften or otherwise dam
age the rubber.
Secure the drive flange (21, Figure 6) to the engine
bellhousing with the previously removed hardware
(6, 7 and 9).