Gorman-Rupp Pumps PAH6A60C-B 1514055 and up User Manual
Page 41
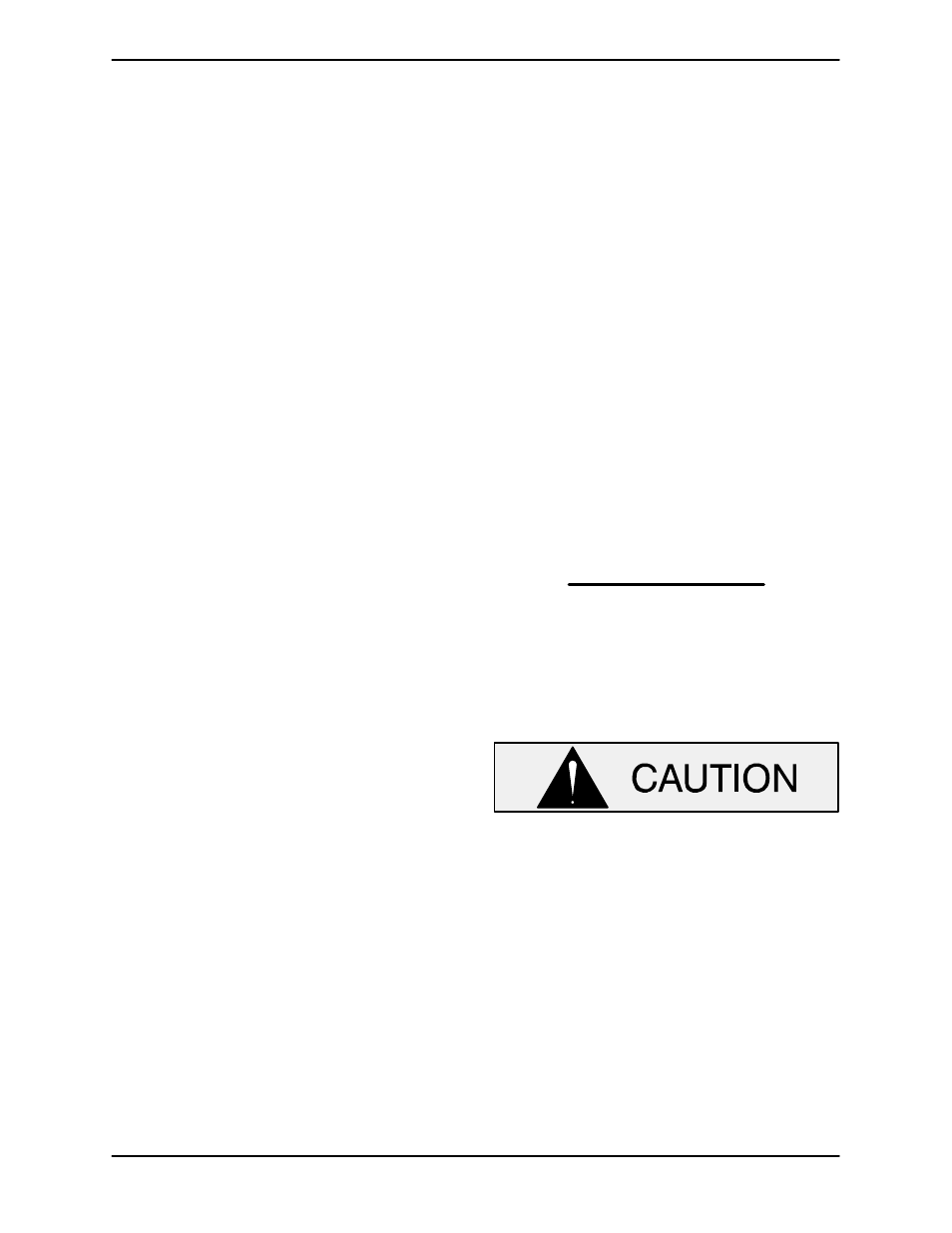
OM-06449
PAH SERIES
MAINTENANCE & REPAIR
PAGE E - 19
discharge check valve assembly using a sling and
a suitable lifting device. Using the previously re
moved hardware, secure the discharge check
valve assembly and flange gasket to the pump as
sembly (1).
Priming Chamber Assembly And Installation
(Figure 5)
Clean and inspect the components of the priming
valve (1). Inspect the linkage and ensure the orifice
button (not shown) squarely engages the valve
seat. Replace the orifice button if required (see
Priming Chamber Removal and Disassembly
for orifice button removal).
If the orifice button was removed, screw the new
orifice button into the linkage bar until fully seated.
Align the hole in the linkage bar with the holes in the
bracket and reinstall the pivot pin. Secure the pivot
pin with the previously removed “e‐clip”.
Adjust the orifice button seating as necessary by
screwing the orifice button into or out of the linkage
bar. Proper adjustment is achieved when the ori
fice button fully seats against the orifice before the
linkage bar on the float bottoms against the
threads on the orifice button. When adjustment is
complete, install and tighten the lock washer and
hex nut securing the orifice button.
Install the strainer (6) and priming valve gasket (4).
Lower the float into the priming chamber (5) and
secure the priming valve with the previously re
moved hardware (2 and 3).
(Figure 4)
Install the baffle (9) and gasket (8) on the suction
spool (7, Figure 1) and use a sling and suitable lift
ing device to position the priming chamber assem
bly on the suction spool. Secure the priming cham
ber assembly with the hardware (6 and 7).
Reconnect the suction piping to the hopper spool
and the air discharge tubing to the priming cham
ber assembly.
LUBRICATION
Seal Assembly
(Figure 3)
Before starting the pump, remove the air vent (13)
and fill the seal cavity with approximately 170
ounces (5 liters) of SAE No. 30 non‐detergent oil to
the center of the sight gauge (10A). Clean and rein
stall the vented plug. Check the oil level regularly
and maintain it at the middle of the sight gauge.
Bearings
(Figure 3)
The bearing housing was fully lubricated when
shipped from the factory. Check the oil level regu
larly through the sight gauge (10)
and maintain it at
the midpoint of the gauge. When lubrication is re
quired, remove the air vent (13A) and add SAE No.
30 non‐detergent oil through the opening. When
lubricating a dry (overhauled) intermediate, fill the
bearing cavity with approximately 50 ounces (1,5
liters). Clean and reinstall the air vent. Do not over‐
lubricate. Over‐lubrication can cause the bearings
to over‐heat, resulting in premature bearing failure.
NOTE
The white reflector in the sight gauge must be posi
tioned horizontally to provide proper drainage.
Under normal conditions, drain the bearing hous
ing once each year and refill with clean oil. Change
the oil more frequently if the pump is operated con
tinuously or installed in an environment with rapid
temperature change.
Monitor the condition of the bearing lubri
cant regularly for evidence of rust or mois
ture condensation. This is especially im
portant in areas where variable hot and
cold temperatures are common.
For cold weather operation, consult the factory or a
lubricant supplier for the recommended grade of
oil.
Power Source
Consult the literature supplied with the power
source, or contact your local power source repre
sentative.