Gorman-Rupp Pumps 04A52-B 1326393 and up User Manual
Page 24
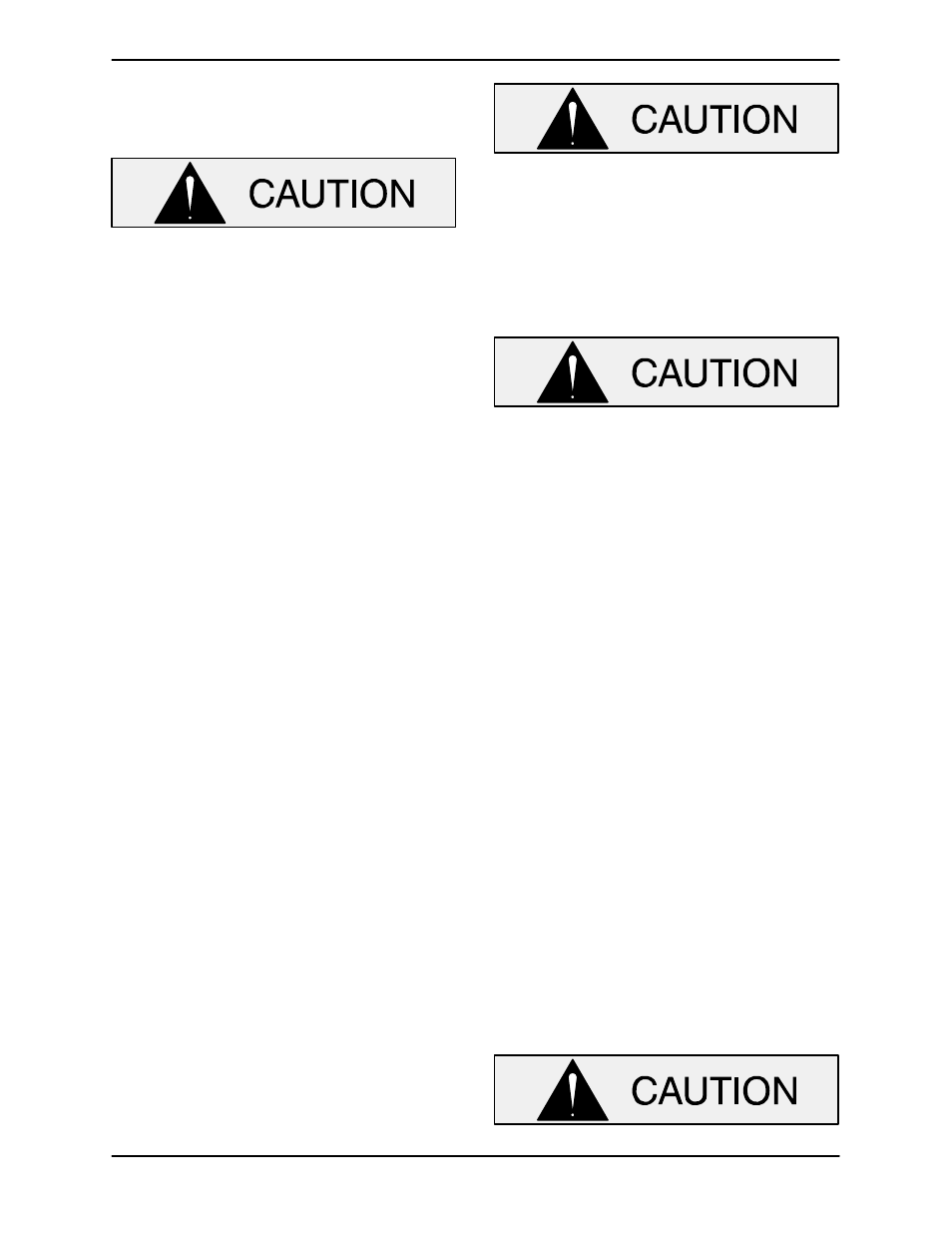
OM-01231
0 SERIES
MAINTENANCE & REPAIR
PAGE E - 5
the cuts through the ring, and remove it from the
pump casing. Use caution not to damage the
pump casing bore when removing the wear ring.
Use caution not to damage the pump cas
ing bore when removing the wear ring.
Impeller Removal
Immobilize the impeller by inserting a bar between
the impeller vanes, being careful not to damage
the vanes. Disengage the hardware (45, 46 and
47). Remove the bar from the impeller.
Install 3/8-16 UNC by 4‐inch long capscrews in
the tapped holes in the impeller. Use the caps
crews and a suitable puller to remove the impeller
from the shaft. Use caution when removing the im
peller; tension on the seal spring will be released as
the impeller is removed. Retain the impeller key (9).
Remove the impeller adjusting shims (53). Tie and
tag the shims or measure and record their thick
ness for ease of reassembly.
Seal Removal and Disassembly
(Figures 1 and 2)
Remove the seal spring. Slide the shaft sleeve (10)
and rotating portion of the seal off the shaft as a
unit.
Apply oil to the sleeve and work it up under the rub
ber bellows. Slide the rotating portion of the seal off
the shaft sleeve.
Remove the machine screws (48) and slide the
seal plate and stationary element off the impeller
shaft as a unit. Press the stationary seal element
and O‐ring out of the seal plate from the back side.
Inspect the wear ring (51) for excessive wear or
damage. The wear ring is secured in the seal plate
by a press fit. If replacement is required, use a
small bit to drill two holes through the ring horizon
tally, 180
_ apart. Use a saw or chisel to complete
the cuts through the ring, and remove it from the
seal plate. Use caution not to damage the seal
plate bore when removing the wear ring.
Use caution not to damage the seal plate
bore when removing the wear ring.
Shaft And Bearing Removal And Disassembly
When the pump is properly operated and main
tained, the pedestal should not require disassem
bly. Disassemble the shaft and bearings only
when there is evidence of wear or damage.
Shaft and bearing disassembly in the field
is not recommended. These operations
should be performed only in a properly
equipped shop by qualified personnel.
Remove the pedestal drain plug (29) and drain the
lubricant. Clean and reinstall the drain plug.
Remove the slinger ring (33). Disengage the hard
ware (12 and 13) and slide the assembled bearing
cap (32) and oil seal (14) off the shaft. Press the oil
seal from the bearing cap.
Use snap ring pliers to remove the bearing retain
ing ring (24) from the pedestal bore.
Loosen, but do not remove, the machine screws
(21). Pry the retainer (26) from the pedestal bore
using a pair of screwdrivers against the heads of
the machine screws. After removing the retainer,
tighten the machines screws in the retainer.
Remove the bearing shim set (23); tie and tag the
shims, or measure and record their thickness for
ease of reassembly.
Press the oil seal (18) from the bearing retainer,
and remove the O‐ring (25) from the pedestal bore.
Place a block of wood against the impeller end of
the shaft and tap the shaft (20) and assembled
bearings (15 and 17) out of the pedestal.
After removing the shaft and bearings, clean and
inspect the bearings in place as follows.
To prevent damage during removal from