Gorman-Rupp Pumps 82H52-B 252751 thru 1325647 User Manual
Page 25
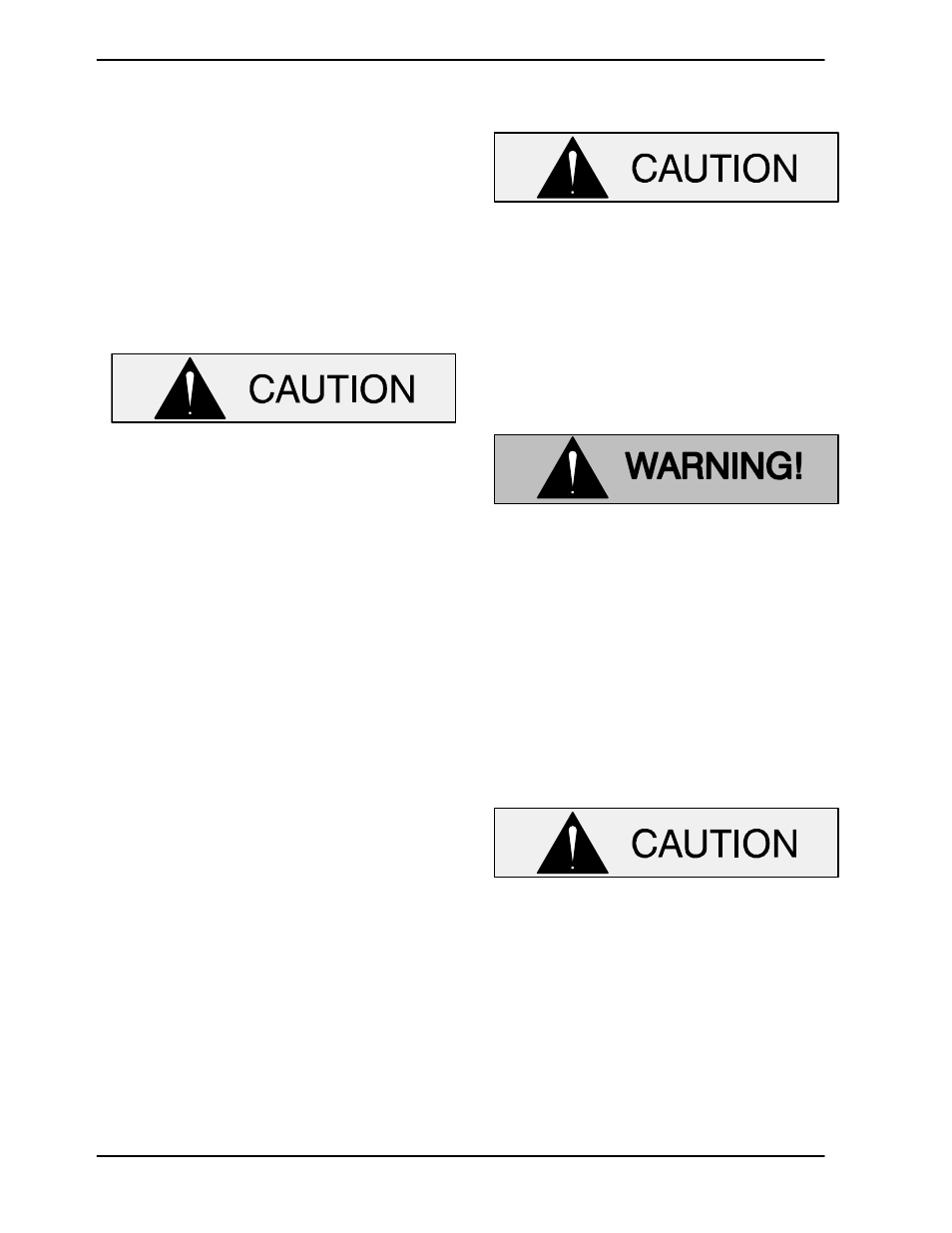
OM−00836
80 SERIES
MAINTENANCE & REPAIR
PAGE E − 6
press the stationary seat and O-ring out of the seal
plate from the back side.
If no further disassembly is required, see Seal
Reassembly and Installation.
Shaft And Bearing Removal And Disassembly
When the pump is properly operated and main-
tained, the pedestal should not require disassem-
bly. Disassemble the shaft and bearings only
when there is evidence of wear or damage.
Shaft and bearing disassembly in the field
is not recommended. these operations
should be performed only in a properly-
equipped shop by qualified personnel.
Remove the pedestal drain plug (23) and drain the
pedestal. Clean and reinstall the plug.
Remove the slinger ring (7) from the shaft. Remove
the pedestal mounting hardware from the base.
Tie and tag any shims used under the mounting
feet for leveling.
Use snap ring pliers to remove the bearing retain-
ing ring (14) from the pedestal bore. Remove the
bearing shim set (20); tie and tag the shims, or
measure and record their thickness for ease of
reassembly.
Remove the setscrews (17) from the bearing re-
tainer (18) and install two machine screws
(#10−32 x 1−inch long, not supplied). Pry the re-
tainer from the pedestal bore using a pair of screw-
drivers against the heads of the machine screws.
Do not use the machine screws to jack against the
ball bearing. Remove the machine screws and re-
install the setscrews.
Press the oil seal (19) from the bearing retainer,
and remove the O-ring (13) from the pedestal bore.
Place a block of wood against the impeller end of
the shaft and tap the shaft and assembled bear-
ings (8 and 12) out of the pedestal.
Press the oil seal (24) from the pedestal bore.
After removing the shaft and bearings, clean and
inspect the bearings in place as follows.
To prevent damage during removal from
the shaft, it is recommended that bearings
be cleaned and inspected in place. It is
strongly recommended that the bearings
be replaced any time the shaft and bear-
ings are removed.
Clean the pedestal, shaft and all component parts
(except the bearings) with a soft cloth soaked in
cleaning solvent. Inspect the parts for wear or dam-
age and replace as necessary.
Most cleaning solvents are toxic and
flammable. Use them only in a well-ven-
tilated area free from excessive heat,
sparks, and flame. Read and follow all
precautions printed on solvent contain-
ers.
Inspect the shaft for distortion, nicks or scratches,
or thread damage on the impeller end. Dress small
nicks and burrs with a fine file or emery cloth. Re-
place the shaft if defective.
Clean the bearings thoroughly in fresh cleaning
solvent. Dry the bearings with filtered compressed
air and coat with light oil.
Bearings must be kept free of all dirt and
foreign material. Failure to do so will great-
ly shorten bearing life. Do not spin dry
bearings. This may scratch the balls or
races and cause premature bearing fail-
ure.
Rotate the bearings by hand to check for rough-
ness or binding and inspect the bearing balls. If ro-
tation is rough or the bearing balls are discolored,
replace the bearings.
The bearing tolerances provide a tight press fit
onto the shaft and a snug slip fit into the pedestal.