Gorman-Rupp Pumps 86A2-B 819132 and up User Manual
Page 29
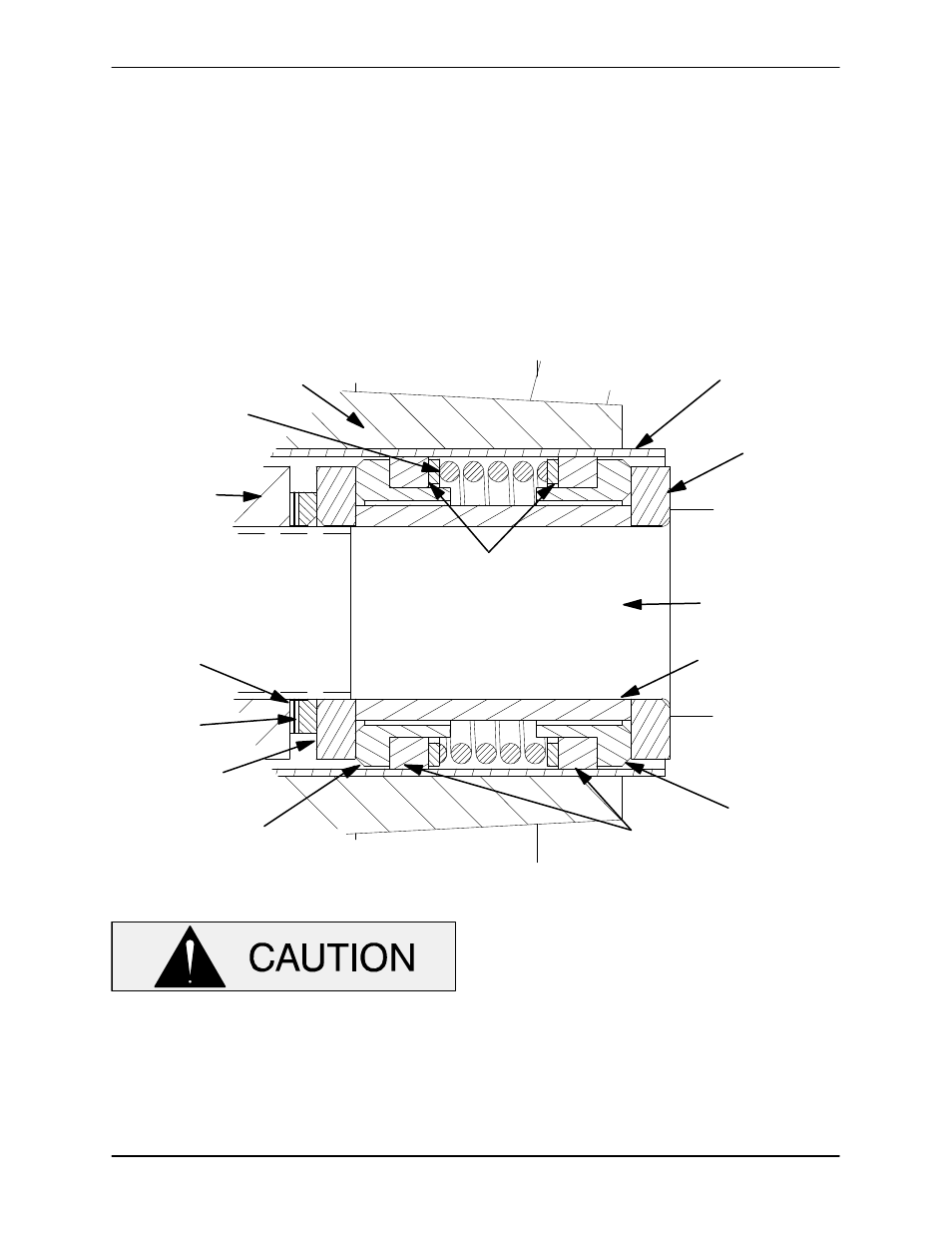
80 SERIES
OM−00950
MAINTENANCE & REPAIR
PAGE E − 8
gency, carefully wash all metallic parts in fresh
cleaning solvent and allow to dry thoroughly.
Handle the seal parts with extreme care to prevent
damage. Be careful not to contaminate precision
finished faces; even fingerprints on the faces can
shorten seal life. If necessary, clean the faces with a
non-oil based solvent and a clean, lint-free tissue.
Wipe lightly in a concentric pattern to avoid
scratching the faces.
Inspect the seal components for wear, scoring,
grooves, and other damage that might cause leak-
age. Clean and polish the shaft sleeve, or replace it
if there are nicks or cuts on either end. If any com-
ponents are worn, replace the complete seal;
never mix old and new seal parts.
If a replacement seal is being used, remove it from
the container and inspect the precision finished
faces to ensure that they are free of any foreign
matter.
To ease installation of the seal, lubricate the seal
liner (64) with water or a very small amount of oil,
and apply a drop of light lubricating oil on the fin-
ished faces. Assemble the seal as follows, (see Fig-
ure 3).
IMPELLER
SHAFT
STATIONARY
SEAT
STATIONARY
WASHERS
ROTATING
ELEMENT
IMPELLER
SHIMS
ROTATING
ELEMENT
SEAL PLATE
SPRING
IMPELLER
SPACER
SLEEVE
PACKING RINGS
SEAL LINER
STATIONARY
SEAT
SPACER
WASHER
Figure 3. Seal Assembly
This seal is not designed for operation at
temperatures above 110
_F (43_C). Do not
use at higher operating temperatures.
Before installing the seal, inspect the bore of the
seal liner (67) for wear or grooves which might
cause leakage or damage to the seal packing
rings. If the seal liner requires replacement, re-
move the seal plate assembly as described in Seal
Removal And Disassembly, and position it on the
bed of an arbor (or hydraulic) press. Use a new
sleeve to force the old one out. After the new liner is
properly installed, a 1/4-inch (6,4 mm) diameter
hole must be drilled through it to permit the flow of
lubricant to the seal assembly. Be careful to center
the drill in the threaded grease piping hole and not
damage the threads. Deburr the hole from the in-
side of the seal liner after drilling.