Gorman-Rupp Pumps 81 1/2P47A-B 801848 and up User Manual
Page 26
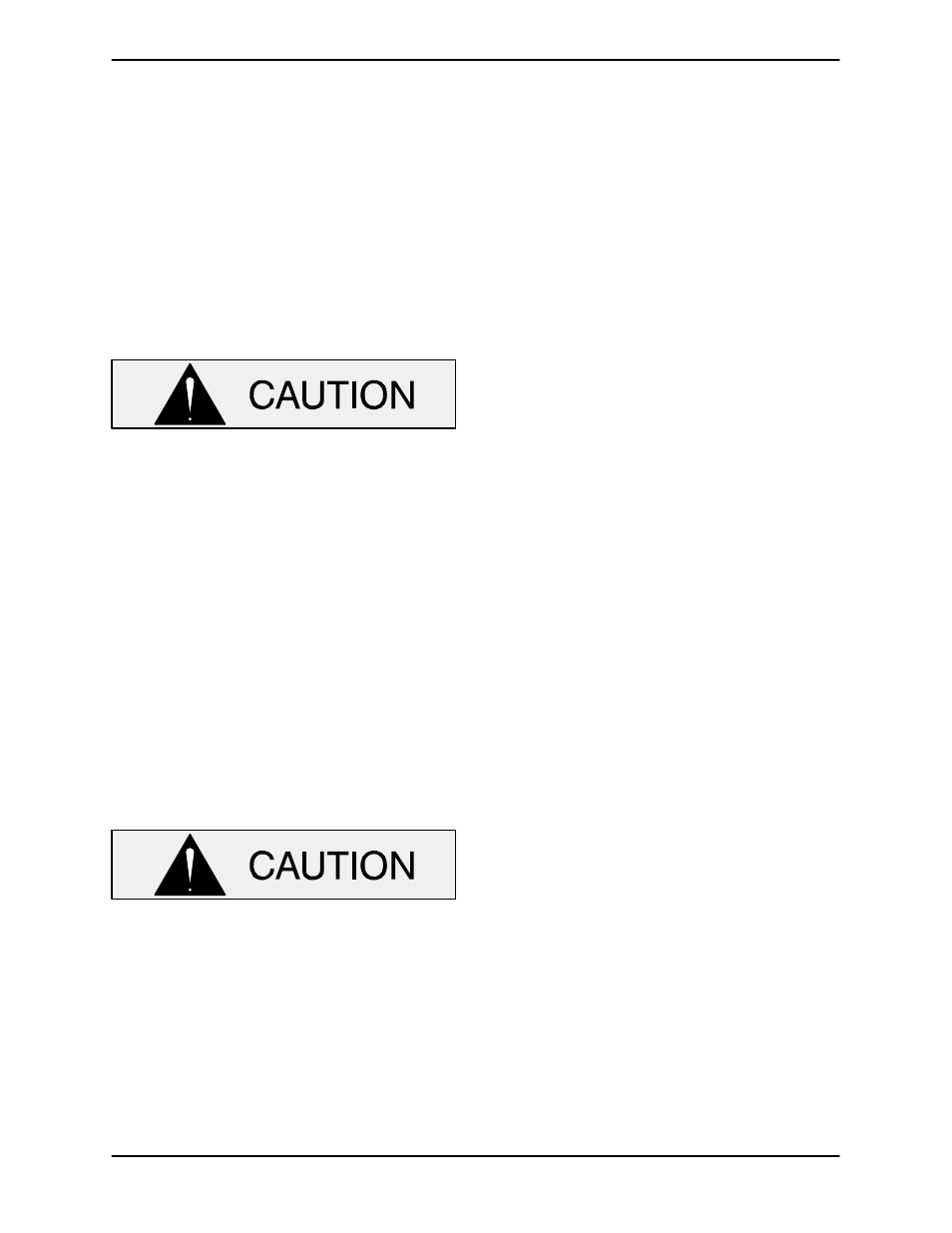
OM-02163
80 SERIES
MAINTENANCE & REPAIR
PAGE E - 7
Impeller Installation
Inspect the impeller, and replace it if cracked or
badly worn. Install the same thickness of impeller
shims (15) as previously removed. Install the im
peller key (4) and slide the impeller onto the shaft,
taking care not to damage the sealing elements.
Install a new impeller screw O‐ring (16). Immobilize
the impeller by wedging a block of wood between
the vanes to prevent shaft rotation. Install the im
peller screw (16) to 15 to 20 in. lbs. (1,7 to 2,3 m.
kg.). Remove the wood block.
The vane plate (20) will seat properly in
only one position; do not try to force the
vane plate onto the intermediate alignment
pins.
A clearance of .008 to .015 inch ( 0,30 to 0,38 mm)
between the impeller and the vane plate (20) is
necessary for maximum pump efficiency. Position
the vane plate over the impeller and the alignment
pins on the intermediate. The vane plate will seat
properly in only one position; do not try to force the
vane plate onto the intermediate alignment pins.
Use a feeler gauge to measure this clearance. Add
or remove impeller shims until the proper clear
ance is achieved.
Vane Plate and Pump Casing Installation
Follow all torque recommendations when
securing the pump hardware. Over‐tight
ening can cause pump components to
crack or threads to strip.
If the flow guide (24) was removed at disassembly,
install a new flow guide O‐ring (23) and secure the
flow guide to the pump casing (1) by torquing the
self‐tapping screws (25) in an alternating pattern to
8 to 10 ft. lbs. (0,9 to 1,1 m. kg.).
Install the vane plate O‐ring (21) and the pump cas
ing O‐ring (5). Position the vane plate over the im
peller and the alignment pins on the intermediate.
Check impeller‐to‐vane plate clearance as de
scribed in Impeller Installation.
Carefully slide the pump casing over the vane plate
and secure it to the intermediate by torquing the
self‐tapping screws (6) in an alternating pattern to
15 to 20 in. lbs. (1,7 to 2,3 m. kg.).
Install the capscrews and nuts (17 and 18) and
torque them in an alternating pattern to 20 to 25 in.
lbs. (2,3 to 2,9 m. kg.).
Final Pump Assembly
Be sure the pump and motor are securely
mounted to the base.
Install the suction and discharge lines and open all
valves. Make certain that all piping connections are
tight, properly supported and secure.
Fill the pump casing with clean liquid.
Refer to OPERATION, Section C, before putting
the pump back into service.
LUBRICATION
Seal Assembly
The seal assembly is lubricated by the medium be
ing pumped. No additional lubrication is required.
Bearings
The shaft bearings are permanently lubricated by
the manufacturer and sealed within the integral
shaft and bearing housing assembly. No routine lu
brication or maintenance of the bearings is re
quired.