Gorman-Rupp Pumps 12D-1B20 1483730 and up User Manual
Page 25
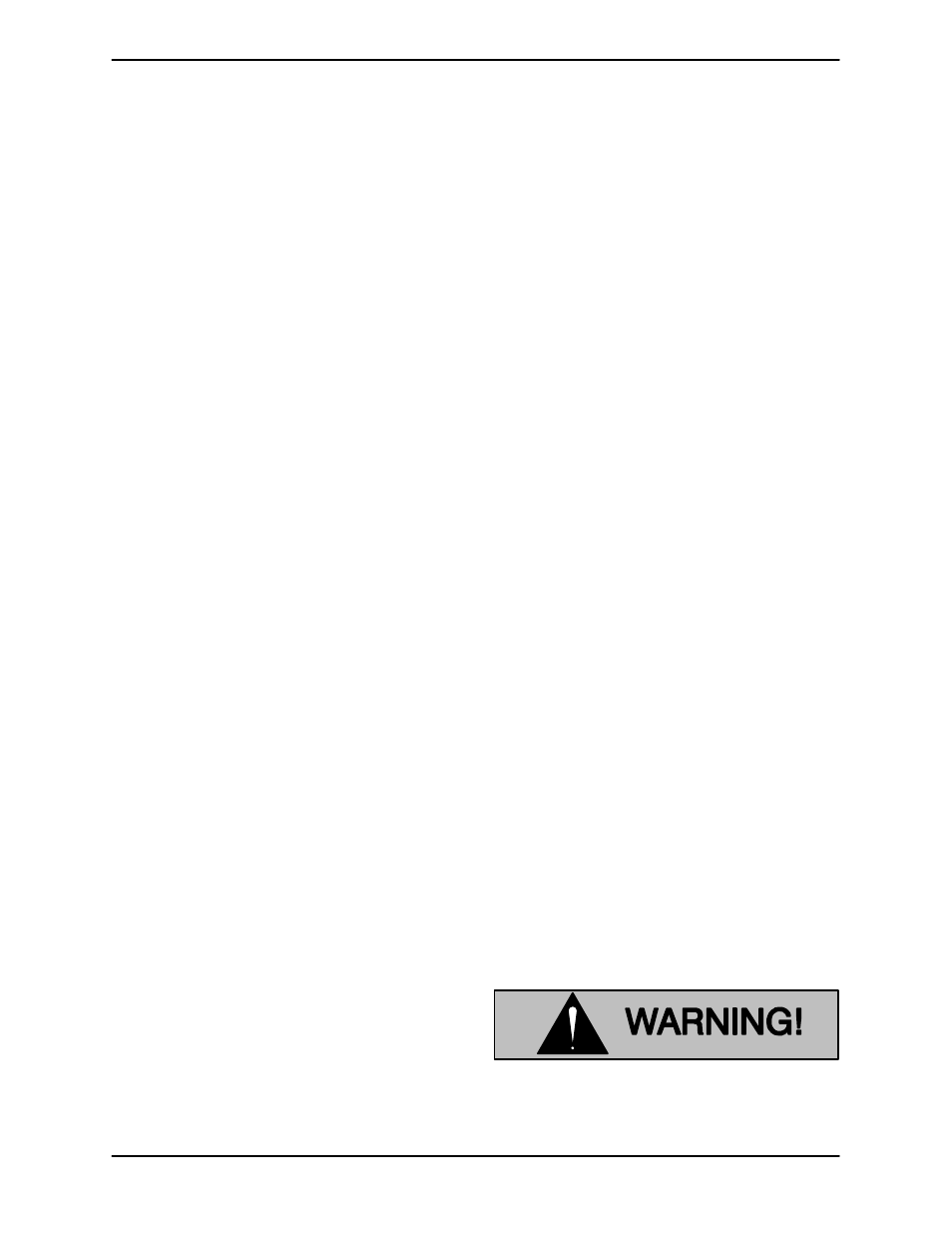
OM−06360
10 SERIES
MAINTENANCE & REPAIR
PAGE E − 7
Pump Casing Removal
(Figure 1)
To service the impeller or seal assembly, discon-
nect the discharge piping. Remove the hardware
(7, 8, 9 and 10) securing the pump casing (1) to the
rollover base (4).
(Figure 2)
Support the pump casing using a suitable hoist
and sling. Remove the nuts (9) and separate the
pump casing (1) from the intermediate (8) by pull-
ing the casing straight away. For ease of reas-
sembly, tie and tag any leveling shims used under
the casing mounting feet.
Remove the casing gaskets (13). Record the thick-
ness of the gaskets for future reference. Clean the
mating surfaces of the intermediate and pump cas-
ing.
Impeller Removal
(Figure 2)
Before removing the impeller (12), turn the cross
arm on the automatic grease cup (4) clockwise un-
til it rest against the cover (see Figure 4). This will
prevent the grease from escaping when the impel-
ler is removed.
To loosen the impeller, tap the vanes of the impeller
in a counterclockwise direction (when facing the
impeller) with a block of wood or a soft-faced mal-
let. Be careful not to damage the vane. Unscrew
the impeller and replace it if cracked or badly worn.
Use caution when removing the impeller; tension
on the seal spring will be released as the impeller is
unscrewed.
Slide the impeller adjusting shims (11) off the im-
peller shaft. Tie and tag the shims or measure and
record their thickness for ease of reassembly.
Seal Removal and Disassembly
(Figures 2 and 3)
Carefully remove the outer stationary and rotating
seal elements, packing ring, stationary washer,
seal spring, and spacer sleeve from the intermedi-
ate. Using a stiff wire with a hooked end, remove
the inboard stationary washer, packing ring and
stationary and rotating seal elements.
Inspect the seal liner (29) for wear or grooves
which could cause leakage or damage to the seal
packing rings. The seal liner is a press fit in the in-
termediate (8) and does not normally require re-
placement. If replacement is necessary, disen-
gage the hardware (6 and 7) and separate the in-
termediate from the engine. Remove the grease
cup and elbow (4 and 5) from the intermediate.
If no further disassembly is required, see Seal
Reassembly and Installation.
Seal Reassembly and Installation
(Figures 2 and 3)
Before installing the seal inspect the bore of the
seal liner (29) for wear or grooves which might
cause leakage or damage to the seal packing
rings. If the seal liner must be replaced, remove the
intermediate as described in Seal Removal And
Disassembly, and position it on the bed of an ar-
bor (or hydraulic) press. Use a new sleeve to force
the old one out. After the new liner is properly in-
stalled, a 1/4-inch diameter hole must be drilled
through it to permit the flow of lubricant to the seal
assembly. Be careful to center the drill in the
threaded grease piping hole and not damage the
threads. Deburr the hole from the inside of the seal
liner after drilling.
Inspect the engine crankshaft for damage. Small
scratches or nicks may be removed with a fine file
or emery cloth. If excessive wear exists, the shaft
will have to be replaced in the engine (refer to the
engine service manual).
Position the intermediate against the engine and
secure it in place using the attaching hardware (6
and 7).
Clean the seal cavity and shaft with a cloth soaked
in fresh cleaning solvent.
Most cleaning solvents are toxic and
flammable. Use them only in a well ven-
tilated area free from excessive heat,
sparks, and flame. Read and follow all