Gorman-Rupp Pumps 86A2-F4L 1242877 thru 1322537 User Manual
Page 34
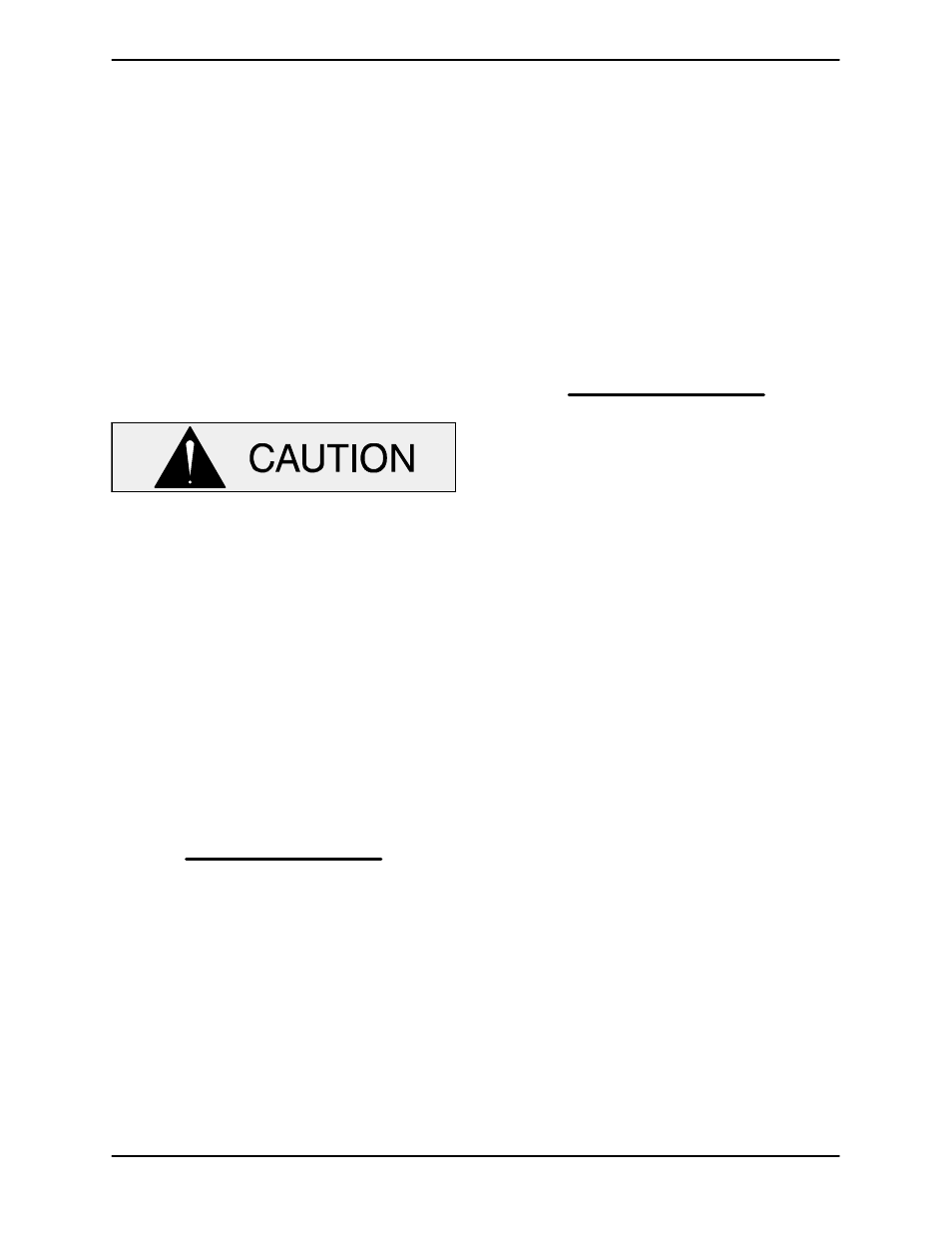
OM--00957
80 SERIES
MAINTENANCE & REPAIR
PAGE E -- 13
Slide the seal spacer washer (15) onto the shaft
with the chamfered side facing the shaft shoulder.
Reinstall the automatic grease cup and piping (16,
17 and 18) in the seal plate. After the impeller has
been installed, lubricate the seal as indicated in
LUBRICATION.
Impeller Installation
(Figure 2)
Inspect the impeller, and replace it if cracked or
badly worn. Install the same thickness of impeller
shims (13) as previously removed and screw the
impeller onto the shaft until tight.
The shaft and impeller threads
must be
completely clean before reinstalling the im-
peller. Even the slightest amount of dirt on
the threads can cause the impeller to seize
to the shaft, making future removal difficult
or impossible without damage to the im-
peller or shaft.
A clearance of .020 to .040 inch (0,5 to 1,0 mm) be-
tween the impeller and the seal plate is recom-
mended for maximum pump efficiency. Measure
this clearance and add or subtract impeller shims
until it is reached.
NOTE
The seal plate must be tight against the intermedi-
ate while setting the back impeller clearance.
Pump Casing and Wear Plate Installation
(Figure 2)
If the wear plate (38) was removed for replace-
ment, secure the replacement wear plate to the
pump casing with the hardware (40 and 41).
Remove the two capscrews temporarily securing
the seal plate, and install the same thickness of
pump casing gaskets (37) as previously removed.
Secure the pump casing to the seal plate and inter-
mediate with the nuts (35).
A clearance of .010 to .020 inch (0,3 to 0,5 mm) be-
tween the impeller and the wear plate is also rec-
ommended for maximum pump efficiency. This
clearance can be obtained by removing gaskets
from the casing gasket set until the impeller
scrapes against the wear plate when the shaft is
turned. After the impeller scrapes, add approxi-
mately .010 inch (0,3 mm) of gaskets.
NOTE
An alternate method of adjusting this clearance is to
reach through the discharge port and measure the
clearance with a feeler gauge. Add or subtract
pump casing gaskets until the proper impeller
clearance is attained.
(Figure 1)
Reinstall any leveling shims used under the pump
casing (1) mounting feet and secure the casing to
the base (49) with the previously removed hard-
ware (50, 51 and 52).
Suction Check Valve Installation
(Figure 2)
Inspect the check valve components and replace
them as required. Subassemble the check valve
weights (52 and 54) and gasket (53) using the at-
taching hardware (50 and 51).
Install the check valve assembly in the valve seat
(55). Replace the seat gasket (56) and secure the
valve seat to the suction port using the round head
machine screws (48). Replace the suction flange
gasket (43) and secure the suction flange (44) to
the seat with the nuts (46).
Check the operation of the check valve to ensure
proper seating and free movement.
Final Pump Reassembly
(Figure 1)
Be sure the pump and intermediate are secure to
the engine and the base.
Install the suction and discharge lines and open all
valves. Make certain that all piping connections are
tight, properly supported and secure.
Be sure the pump and engine have been properly
lubricated, see
LUBRICATION.