Wayne-Dalton TORQUEMASTER 5500 User Manual
Installation instructions layout, 9a 11b, Start here
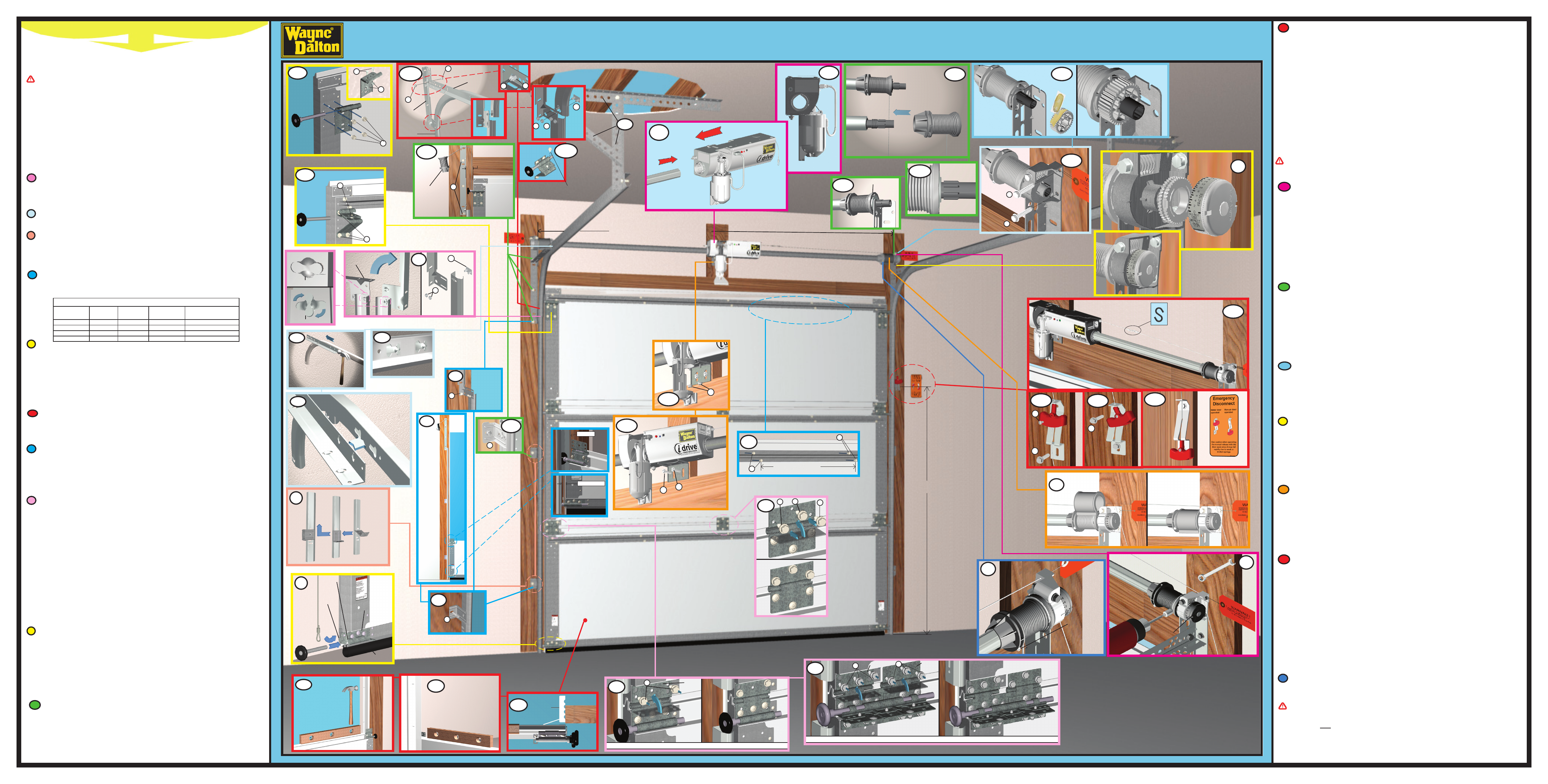
DOOR-WIDTH PLUS 3-3/8” (86 mm) TO 3-1/2”
(89 mm)
72”
(1829 mm)
13A
12A
14B
g
g
14A
20
18
SeT ScReW
19
cANOe
cLIP
3
7B
g
10B
g
16B
a
17A
17B
17c
17D
h
h
j
21
12B
13B
13c
RIGHT HAND
DRUM
11A
b
d
FULLy ADjUSTABLe
TRAck
veRTIcAL
TRAck
FLAG
ANGLe
HORIZONTAL
ANGLe
d
b
a a
k
7c
g
16A
i
i
f
c A B L e
5 / 8 ” ( 1 6 M M )
7A
5
LeFT HAND
BOTTOM
BRAckeT
MILFORD
PIN
HINGe
TUBe
ASTRAGAL
6A
6B
6c
10A
g
1-11/16” (43mm)
TO 1-3/4” (44mm)
LEFT HAND
DRUM
a
c
2c
2B
2A
Beginning with the right side, install the counter gear with the missing tooth toward the outside, away from the end
bracket. Press the counter gear onto the end bracket until snaps engage. Select the right hand counter cover assembly
and align the hex of the counter cam with the end of the winding shaft. Also, align the “0” on the counter cover with the
raised rib on the end bracket. Press the counter cover assembly against the counter gear until it locks into place. Repeat
for left hand side for double spring applications.
NOTE:
No drive gear, counter gear or counter cover assembly is required on left hand side for single spring applica-
tions. Only an end bracket is needed.
IMPORTANT!
At this time do not wind counter balance springs!
15
CONTINUE INSTALLATION INSTRUCTIONS ON REVERSE SIDE.
18
NOTE:
For non-idrive™ operated garage doors see Alternate Installations on the reverse side of this manual.
Lay the torque tube on the floor (inside garage) in front of the door with the labeled end to the left.
NOTE:
Opener will not slide over a torque tube label.
Attempting to slide opener over the left end of the torque tube can damage the internal electronics.
NOTE:
Hold opener by the main body. Do NOT hold by the motor.
Look into the opener’s left side to ensure the left hand bearing and the internal (black) sleeve are aligned with the torque
tube profile. Once aligned, slide the opener power head onto the right hand end of the torque tube. As the right end of
the torque tube enters the internal (black) sleeve, rotate the opener back and forth slightly to help aid alignment.
NOTE:
Do not force the opener onto the torque tube if misalignment occurs.
Continue sliding the opener power head onto the torque tube. Align the right hand bearing with the torque tube and slide
the opener power head completely onto the torque tube until the torque tube exits the opener power head’s right hand
bearing. Continue sliding the opener power head to the center of the torque tube and plug the motor power cord into
the opener power head.
IMPORTANT!
Right and left hand is always determined from inside the garage looking out.
12 idrive™ Installation
13
Shake the torque tube gently to extend the winding shafts out about 5” on each side. For single spring applications,
there will be no left hand winding shaft in the torque tube. Lift the torque tube and rest it on top of flagangles. Orient
torque tube so that back of opener is flat against header/spring pad. Cable drums and torque tube are cam shaped to fit
together only one way. To install the cable drum, slide the drum over the winding shaft until the drum seats against the
torque tube. The winding shaft must extend past the drum far enough to expose the splines and the groove. Align the
winding shaft groove with the round notch in the flagangle. Repeat for opposite side for double spring applications. For
single spring applications, insert the left hand loose winding shaft into the left hand drum prior to sliding the drum over
the torque tube.
NOTE:
On single spring applications, take care in handling the loose winding shaft (left side) so that it does not slide
back into the torque tube.
Beginning with the right hand side, lubricate entire circumference of the drive gear with the oil provided in the packet.
DO NOT SUBSTITUTE OIL. Slide the drive gear onto the winding splines until it touches the flagangles.
NOTE:
No drive gear is required for the left side on single spring applications.
IMPORTANT!
Warning tags must be securely attached to both end brackets.
Slide the right hand end bracket over the drive gear. Secure end bracket and the flagangle to the jamb using
(2) 5/16” x 1-5/8” lag screws.
14
Locate the spring pad. The spring pad is a vertical running board directly above the center of the door. Remove
(2) 1/4”-20 flange nuts from bottom of opener power head.
NOTE:
Do not discard flange nuts.
Place the support bracket underneath opener power head, to the right side of motor, centered on spring pad. Level the
torque tube to the top of the door section with the idrive™ resting on the support bracket. Once torque tube is level,
secure support bracket to the spring pad with (2) 1/4” x 2” lag screws. Lift and slide the opener power head over the
support bracket, aligning the mounting studs with the bracket slots. Loosely fasten to mounting studs with the (2) 1/4”-
20 flange nuts.
NOTE:
Do not tighten 1/4”-20 flange nuts to power head studs at this time.
16
17
Attach the loose disconnect cable (located in operator hardware bag) to the opener power head with “S” hook. Close
both ends of “S” hook to lock assembly together. Thread the disconnect cable through hole in right hand end bracket
and remove all slack between power head and right hand end bracket. Mark location on right door jamb, six feet above
the ground to mount disconnect handle. Thread disconnect cable through handle bracket and then handle. Align top of
handle bracket with mark on wall. Remove all cable slack between the power head and top of handle bracket. Insert
and tighten #6-20 x 1/2” screw until snug, and then tighten screw 1 to 1-1/2 additional turns to secure cable in handle.
Trim off excess cable from bottom of handle. Holding handle bracket, remove all remaining slack between power head.
With slack removed, secure bottom of handle bracket with (1) 1/4” x 1-1/2” lag screw.
CAUTION:
Pull handle just enough to remove the cable slack. Pulling the cable more could cause the opener
power head to disconnect from the torque tube.
Rotate disconnect handle to one side exposing upper mounting hole in handle bracket. Secure handle bracket with a
second 1/4” x 1-1/2” lag screw. Apply emergency disconnect label next to the mounted bracket. Use mechanical
fasteners if adhesive will not adhere. Using the emergency disconnect, pull disconnect handle downwards and place it
in the manual door operated position. Use disconnect label for reference. Motor will be rotated 90° from its packaged
position.
NOTE:
If motor does not pivot 90°, see troubleshooting section in the idrive™ main installation manual.
START HeRe
TWISTLOck HOLe
TWISTLOck TAB
FULLy ADjUSTABLe
TRAck
a
q.I. TRAck
FLAG
ANGLe
1
k
f
f
f
8c
15
TorqueMaster™ drums are marked right and left. Make sure you place the cable from the right hand drum on the
right hand milford pin, and left hand drum on the left hand milford pin. Uncoil the counterbalance cables and slip
the loop at the ends of the cables over the milford pins on the bottom section. Insert a roller in the bottom bracket of
the bottom section and insert another roller at #1 end hinge at the top of the bottom section, Fig. 5 and 8A. Repeat
for right side.
NOTE:
Bottom section can be identified by a #1 end hinge, the factory attached bottom astragal, or by the bottom
bracket warning labels on each endstile.
NOTE:
Verify that astragal does not protrude more than 1/2” past ends of the bottom section. If excess needs to be
trimmed off, be careful not to stretch astragal, or it may end up shorter than section width.
IMPORTANT!
Right and left hand is always determined from inside the building looking out.
5
8
Q.I. flagangle: Put the lower Twistlock tab on the flagangle into the Twistlock hole in the vertical track. Give the
flagangle 1/4 turn to lock in place. Repeat for other side.
Fully adjustable flagangle: Secure the vertical to the lower slot in the flagangle using (1) stud plate and (2)
1/4” -20 flange hex nuts. Repeat for other side.
1
2
3
NOTE:
The stutting schedule below is for reference only, all struts are pre-installed at the factory.
4
NOTE:
16’ - 18’ Doors will use A-shaped bracket. The rest of the doors will use the L-shaped brackets
L-shaped bracket: To install the L-shaped top brackets, align the top holes in the top bracket base with the second
set of holes in the endcap as shown in Fig. 9. Fasten using (4) 1/4”-14 x 5/8” self tapping screws. Secure the top slide
to the bracket using (2) 1/4”-20 x 5/8” carriage bolts and (2) 1/4”-20 flanged hex nuts. Repeat for other side.
A-frame bracket: To install the A-frame top brackets, place the top of bracket flush with bottom of the strut, even
with the edge of the endcap. Fasten using (4) 1/4”-14 x 5/8” self tapping screws. Secure the top slide to the bracket
using (1) 1/4”-20 x 5/8” carriage bolt and (1) 1/4”-20 flanged hex nut. Repeat for other side.
9
Position the left hand vertical track over the rollers of the bottom section.
NOTE:
Make sure the counterbalance cable is located between the rollers and the door jamb.
Secure jamb brackets and flagangles to the jamb using 5/16” x 1-5/8” lag screws. Install the right hand vertical track
the same way. Hang cables over flagangles.
IMPORTANT!
The tops of the vertical tracks must be level from side to side. If the bottom section was shimmed
to level it, then the vertical track on the shimmed side, must be raised the height of the shim.
7
Before installing the bottom section, measure and cut vinyl jamb weather-stripping (may not be included) for entire
garage door opening. Temporarily nail the weather-stripping to the door jambs and header approximately 12” to
18” apart. Center the bottom section in the door opening. Level it using wooden shims under the bottom astragal,
if necessary.
6
8A
LeFT HINGe SHOWN, RIGHT HINGe SyMMeTRIcALLy OPPOSITe
f
HINGe
LeAF
To install horizontal track, place the curved end over the top roller. Align the bottom of the horizontal track with the
top of the vertical track.
Q.I. flagangle: Align the key slot in each horizontal track with the quick install tabs on the corresponding flagangle.
Push the curved portion of the horizontal downward to lock into place.
Fully adjustable flagangle : Secure each horizontal track to the corresponding flagangle with (1) stud plate and
(2) 1/4”-20 flanged hex nuts.
NOTE:
On some adjustable flagangles, each horizontal track is secured to the corresponding flagangle with
(2) 1/4”-20 track bolts and nuts.
Level horizontal track and bolt the horizontal angle to the slot in the flagangle using (1) 3/8”-16 x 3/4” truss head bolt and
nut. Repeat for other side. Remove the nail that was temporarily holding the top section in place.
IMPORTANT!
Failure to remove nail before attempting to raise door could cause permanent damage to top sec-
tion.
With horizontal tracks installed, you can now adjust the top brackets. Vertically align the top section with the lower
sections. Once aligned, position top roller in the adjustable slide, out against the horizontal track. Maintaining the slide’s
position, tighten the nuts to secure the slide to the top bracket. Repeat for other side.
NOTE:
If you installed A-frame bracket you will need to lock the top slide into place on the bracket using a 1/4-20 x 11/16”
self-drilling screw into the slide to lock the slide in place (see 11B).
WARNING!
DO NOT RAISE DOOR UNTIL HORIZONTAL TRACKS ARE SECURED AT REAR, AS OUTLINED IN STEP 21, OR
DOOR COULD FALL FROM OVERHEAD POSITION CAUSING SEVERE OR FATAL INJURY.
11
Clamp locking pliers onto both vertical tracks just above third roller. This is to prevent garage door from rising while
winding counterbalance springs.
WARNING!
FAILURE TO CLAMP TRACK CAN ALLOW DOOR TO RAISE AND CAUSE SEVERE OR FATAL INJURY.
Adjust the counter balance cables by rotating the drum until the set screw faces directly away from the header.
IMPORTANT!
Do NOT double wrap counterbalance cables on TorqueMaster drums.
Loosen the set screw no more than 1/2 turn. Pull on the end of the cable to remove all cable slack. Check to ensure the cable
is aligned and seated in the first groove of the cable drum. Snug the set screw, then tighten an additional 1-1/2 turns.
Cut off excess cable.
STRUTTING SCHEDULE
DOOR WIDTH
QUANTITY
TOP OF TOP
SECTION
TOP OF LOCK
SECTION
TOP OF BOTTOM
SECTION
6’ 0” TO 10’ 11”
0
N/A
N/A
N/A
11’ 0” TO 14’ 2”
1
X
N/A
N/A
14’ 3” TO 16’ 2”
2
X
N/A
X
16’ 3” TO 18’ 0”
3
X
X
X
Measure the length of the vertical tracks. Using the Quick Install Jamb Bracket Schedule (shown on reverse side),
determine the placement of the jamb brackets for your door height. Align the Twistlock wings on each jamb bracket
with the correct butterfly hole in the track and turn the jamb bracket perpendicular to the track so the mounting flange
is toward the back leg of the track. Set tracks aside.
Using a hammer, tap the horizontal angle towards the curved end of the track until the hole in track and angle are
aligned. Set tracks aside.
NOTE:
The lock section can be identified by a #3 end hinge for 7’ high 3 section doors, and by the yellow and
black warning label attached to the right side of the section.
Insert rollers into both end stiles of the lock section, Fig. 8A. With assistance lift section and place rollers over the
tops of the vertical tracks. Install by guiding rollers into the vertical track on both sides and gently lowering the sec-
tion onto the bottom section. Vertically align the mark near the center (on back) of the door, or vertically align the
center stiles on the face (on front) of the door. Rotate the hinge leaf upward and fasten the hinge to the above section
with (2) 1/4”-14 x 5/8” self tapping screws, Fig. 8A.
IMPORTANT!
For larger size doors, double end hinges are already pre-installed to the section(s).
Double end hinges are installed by rotating both hinge leafs upward and secure the hinges to the above section
with (6) 1/4”-14 x 5/8” self tapping screws, Fig. 8B.
The center hinges are installed by rotating the hinge leaf upward and secure the hinge to the above section with
(3) 1/4”-14 x 5/8” self tapping screws, Fig. 8C.
IMPORTANT!
Push and hold both hinge leafs up against the section while securing with 1/4”-14x 5/8”
self tapping screws.
Do not install the top section at this time.
IMPORTANT!
TITLED “REMOVING THE OLD DOOR/PREPARING THE OPENING”. IF THE
INSERT SHEET INSTRUCTIONS ARE NOT INCLUDED, CONTACT WAYNE-DALTON CORP. FOR A
FREE COPY.
If removing an existing door, carefully follow the directions given on the insert sheet instruction in the portion
titled “Removing the Old Door”.
WARNING!
REMOVAL OF AN EXISTING DOOR CAN BE DANGEROUS. FOLLOW INSERT
SHEET INSTRUCTIONS CAREFULLY, OTHERWISE SEVERE OR FATAL INJURY COULD RESULT.
Begin the installation of the door by checking the opening. It must be the same size as the door. Vertical jambs
must be plumb and the header level. Side clearance, from edge of door to wall, must be minimum of 3-1/2” (89
mm) on each side. Follow the steps below. The steps correspond to the illustrations on the garage door layout.
IMPORTANT!
Stainless steel or PT2000 Coated lag screws MUST be used when installing center bearing
brackets, end bearing brackets, jamb brackets, operator mounting/support brackets and disconnect
brackets on treated lumber (preservative-treated). Stainless steel lag screws are NOT necessary when
installing products on un-treated lumber.
NOTE:
It is recommended that 5/16” x 1-5/8” lag screws be pilot drilled using a 3/16” drill bit, and 1/4” x 2” lag
screws and 1/4” x 1-1/2” lag screws be pilot drilled using a 1/8” drill bit, prior to fastening.
For proper opening preparation refer to the portion of the insert sheet instructions titled “Preparing the Opening”.
IMPORTANT!
It is recommended that doors 12’ 0” wide and over be installed by two person, to avoid
possible injury.
5500/9700 estate - Standard Lift - TorqueMaster II™
Installation Instructions Layout
8B
HINGe LeAF
f
f
LeFT HINGe SHOWN, RIGHT HINGe SyMMeTRIcALLy OPPOSITe
HINGe
LeAF
9B
f
c
SELFDRILLING
SCREW
4
f
f
30” TO 36” SPAcING
9A
11B
Place top section in the door opening and secure it temporarily by driving a nail into the header near the center of the
door and bending it over the section. Insert rollers into top slides. Now fasten the hinges to the top section, Fig. 8A
thru 8C. When installing a door with a TorqueMaster™ counterbalance system, vertical track alignment is critical.
Position flagangle between 1-11/16” (43 mm) to 1-3/4” (44 mm) from the edge of the door. Flagangles must be par-
allel to the door section ends. Now complete the vertical track installation on both sides by securing the center jamb
brackets and tightening the other 5/16” x 1-5/8” lag screws, Fig. 10.
IMPORTANT!
The dimension between the flagangles must be door-width plus 3-3/8” (86mm) to 3-1/2” (89
mm) for smooth, safe door operation.
10