Maintenance, Warning – RedMax EXTREME EXZ2460S-PH User Manual
Page 26
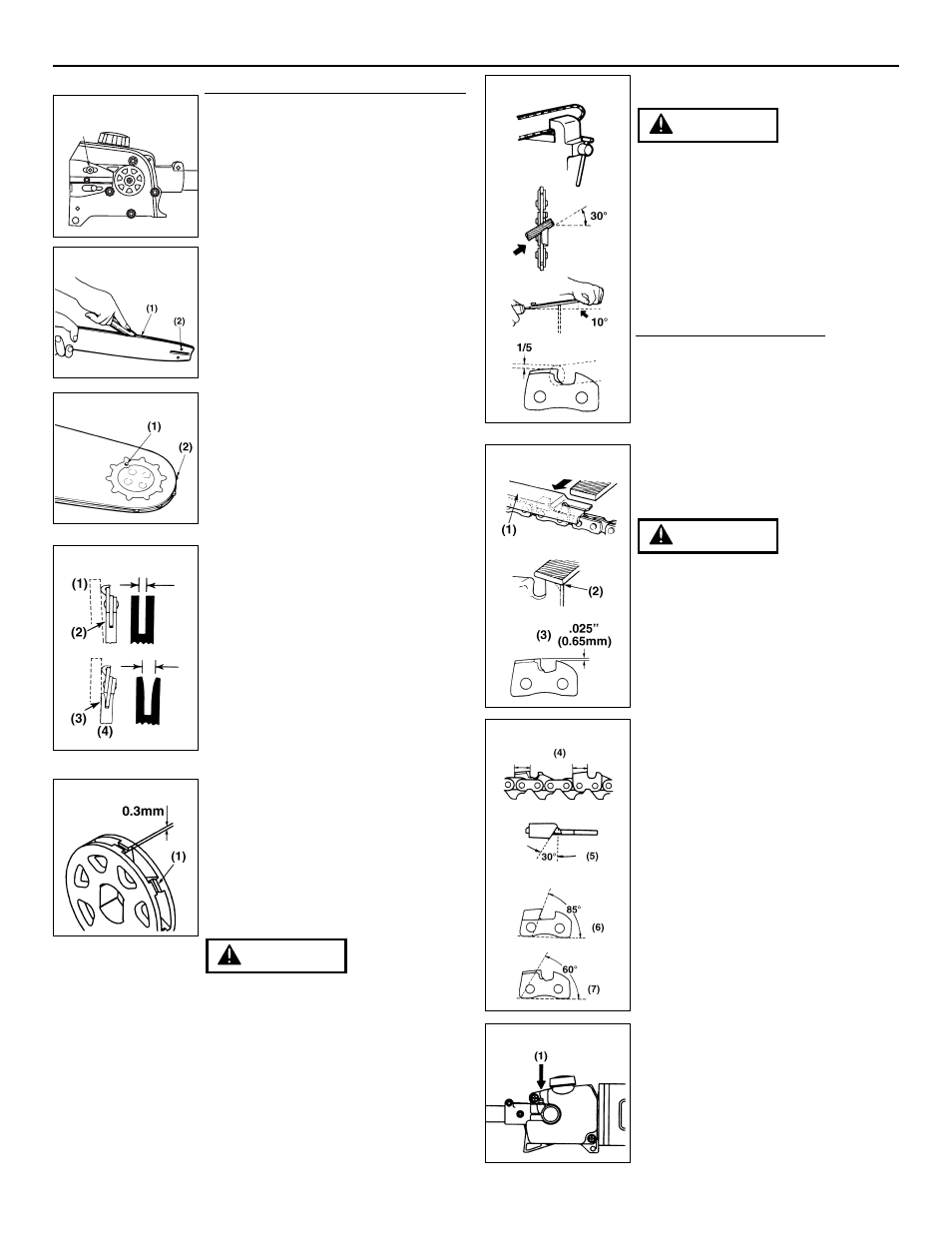
US-26
EXZ2460S-PH
9. Maintenance
(1)
PS-EX MA1
PS-EX MA2
PS-EX MA5
PS-EX MA4
PS-EX MA3
PS-EX MA6
PS-EX MA9
PS-EX MA8
PS-EX MA7
(PS-EX only)
■ OILING PORT
Dismount the guide bar and check the
oiling port for clogging. (MA1)
(1) Oiling port
■ GUIDE BAR
Remove sawdust in the bar groove and
the oiling port. (MA2)
(1) Groove
(2) Oiling port
(Type: Sprocket nose)
Grease the nose sprocket from the
feeding port on the tip of the bar. (MA3)
(1) Grease port
(2) Sprocket
The bar rail should always be a square.
Check for wear of the bar rail. Apply a
ruler to the bar and the outside of a cutter.
If a gap is observed between them, the
rail is normal. Otherwise, the bar rail is
worn. Such a bar needs to be corrected or
replaced.(MA4)
(1) Ruler
(2) Gap
(3) No gap
(4) Chain tilts
■ SPROCKET
Check for extensive wear, and replace it
when the teeth are worn over 0.3mm.
(MA5)
(1) Sprocket
■ SAW CHAIN
It is very important for smooth and
safe operation to keep the cutters
always sharp.
Your cutters need to be sharpened when:
• Sawdust becomes powder-like.
• You need extra force to saw in.
• The cut way does not go straight.
• Vibration increases.
• Fuel consumption increases.
WARNING
Cutter setting standards:
Be sure to wear safety gloves.
Before filing:
• Make sure the saw chain is held
securely.
• Make sure the engine is stopped.
• Use a round file of proper size for your
chain.
Chain type : 90SG
File size :
5/32 in (4.0mm)
Place your file on the cutter and push
straight forward. Keep the file position as
illustrated. (MA6)
After every cutter has been set, check the
depth gauge and file it to the proper level
as illustrated. (MA7)
Be sure to round off the front edge to
reduce the chance of kickback or tie-
strap breakage.
(1) Appropriate gauge checker
(2) Make the shoulder round
(3) Depth gauge standard
Make sure every cutter has the same
length and edge angles as illustrated.
(MA8)
(4) Cutter length
(5) Filing angle
(6) Side plate angle
(7) Top plate cutting angle
■ GEAR CASE
The reduction gears are lubricated by
multipurpose, lithium-based grease in the
gearcase.
Supply new grease every 25 hours of use
or more often depending on the job
condition.
When adding lubricant, use a grease gun
to insert lubricant into the three grease
nipples located on the gear case. (MA9)
(1) Grease fitting
WARNING
WARNING