8. adjust the hub tension, 9. welding cable connection, 10. feeding welding wire – Miller Electric S-21E User Manual
Page 12
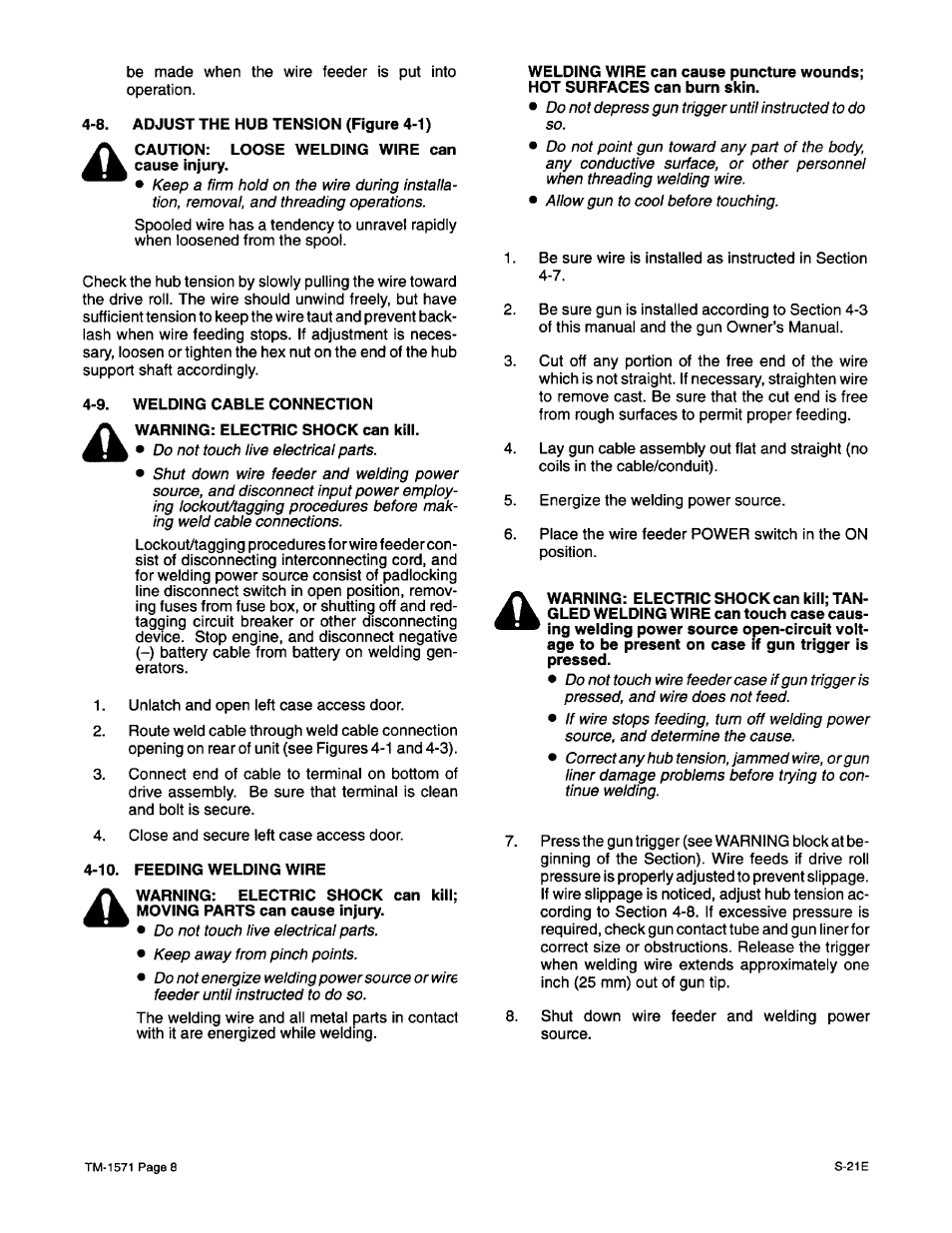
be made when the wire feeder is put into
operation.
4-8.
ADJUST THE HUB TENSION (Figure 4-1)
A
CAUTION:
LOOSE WELDING WIRE can
:ause Injury.
Keep a firm hold on the wire during installa-
tion, removal, and threading operations.
Spooled wire has a tendency to unravel rapidly
when loosened from the spool.
Check the hub tension by slowly pulling the wiretoward
the drive roll. The wire should unwind freely, but have
sufficient tension to keep the wiretaut and prevent back-
lash when wire feeding stops. If adjustment is neces-
sary, loosen or tighten the hex nut on the end of the hub
support shaft accordingly.
4-9.
WELDING CABLE CONNECTION
A
WARNING: ELECTRIC SHOCK can kill.
• Do not touch live electrical parts.
• Shut down wire feeder and welding power
source, and disconnect input power employ-
ing lockout/tagging procedures before mak-
ing weld cable connections.
Lockout/tagging procedures forwire feedercon-
sist of disconnecting interconnecting cord, and
for welding power source consist of padlocking
line disconnect switch in open position, remov-
ing fuses from fuse box, or shutting off and red-
tagging circuit breaker or other disconnecting
device. Stop engine, and disconnect negative
(—) battery cable from battery on welding gen-
erators.
1.
Unlatch and open left case access door.
2.
Route weld cable through weld cable connection
opening on rear of unit (see Figures 4-1 and 4-3).
3.
Connect end of cable to terminal on bottom of
drive assembly. Be sure that terminal is clean
and bolt is secure.
4.
Close and secure left case access door.
4-10.
FEEDING WELDING WIRE
A
WARNING:
ELECTRIC SHOCK can kill;
MOVING PARTS can cause
Injury.
• Do not touch live electrical parts.
• Keep away from pinch points.
• Do not energize welding powersource or wirE
feeder until instructed to do so.
The welding wire and all metal parts in contaci
with it are energized while welding.
WELDING WIRE can cause puncture Wounds;
HOT SURFACES can burn skin.
• Do not depress gun trigger until instructed to do
so.
• Do not point gun toward any part of the body
any conductive surface, or other personnel
when threading welding wire.
• Allow gun to cool before touching.
1.
Be sure wire is installed as instructed in Section
4-7.
2.
Be sure gun is installed according to Section 4-3
of this manual and the gun Owner’s Manual.
3.
Cut off any portion of the free end of the wire
which is not straight. If necessary, straighten wire
to remove cast. Be sure that the cut end is free
from rough surfaces to permit proper feeding.
4.
Lay gun cable assembly out flat and straight (no
coils in the cable/conduit).
5.
Energize the welding power source.
6.
Place the wire feeder POWER switch in the ON
position.
A
WARNING: ELECTRIC SHOCK can kill; TAN-
GLED WELDING WIRE can touch case caus-
ing Welding power source open-circuit volt-
age to be present on case if gun trigger is
pressed.
• Do not touch wire feeder case ifgun trigger is
pressed, and wire does not feed.
• If wire stops feeding, tum off welding power
source, and determine the cause.
• Correctanyhub tension, jammed wire, orgun
liner damage problems before trying to con-
tinue welding.
7.
Press the gun trigger (see WARNING block atbe-
ginning of the Section). Wire feeds if drive roll
pressure is properly adjusted to prevent slippage.
If wire slippage is noticed, adjust hub tension ac-
cording to Section 4-8. If excessive pressure is
required, check gun contact tube and gun liner for
correct size or obstructions. Release the trigger
when welding wire extends approximately one
inch (25 mm) out of gun tip.
8.
Shut down wire feeder and welding power
source.
TM-1571 Page 8
S-21E