Bridge resistance test, Resistance to ground test, Bridge resistance test resistance to ground test – Hardy HI LPRE05 Shear Beams User Manual
Page 32
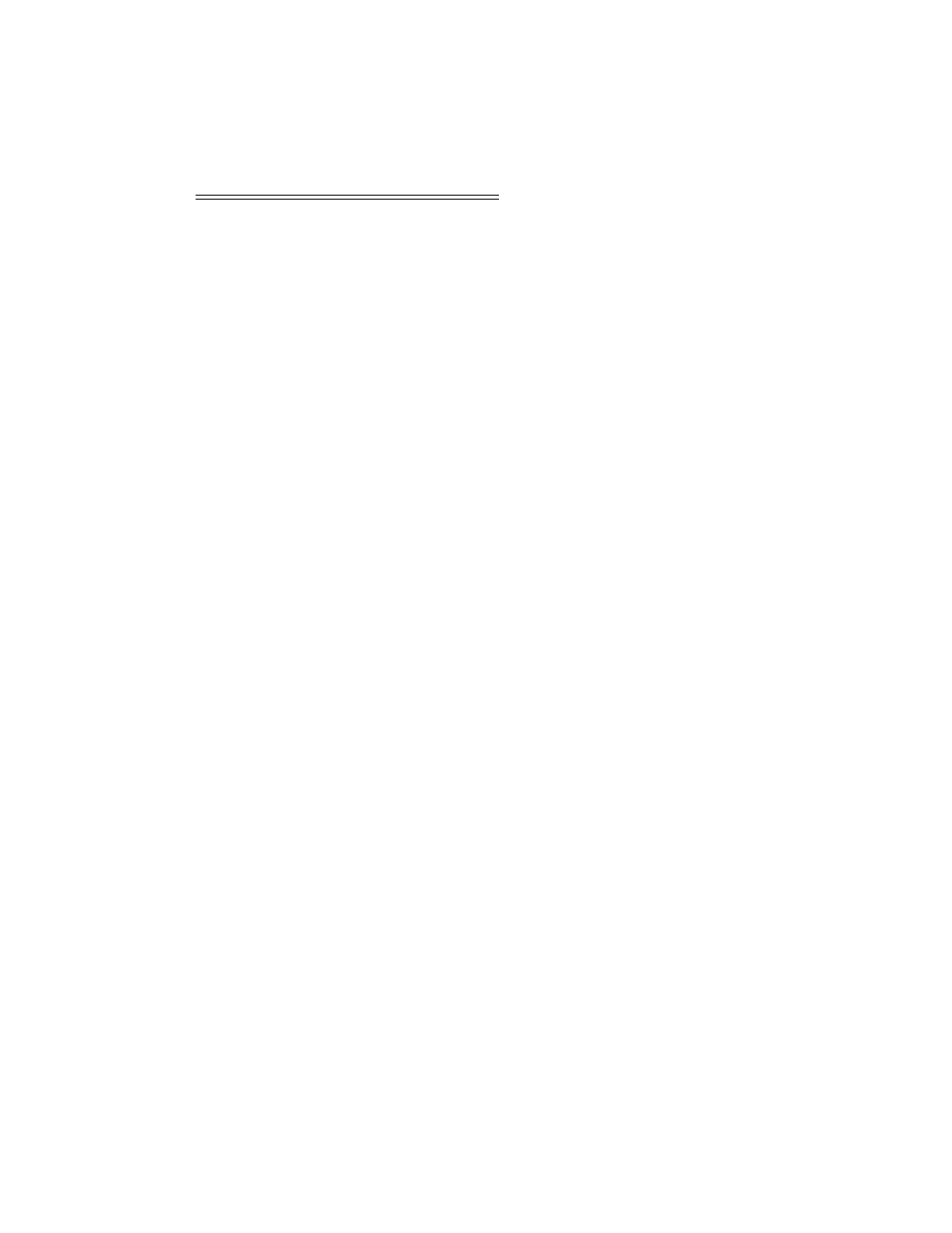
HI HLPS SERIES LOAD POINT ASSEMBLY
Page 26
and measure the LPS output under “no
load” conditions. The reading should be
less than 1% of the full scale output.
NOTE:
Sensors can shift up to about 10% of their full scale
and still function correctly.
Step 2.
If the output has shifted more than 1%,
replace the sensor.
Assumption: A 5VDC excitation on a sensor with a
3mV/V output sensitivity, a 1% shift in zero balance
will yield a 0.1 mV/V change from the specification.
Bridge
Resistance Test
Problem: Changes in Bridge Resistance
Cause: Failure of a compensating element, or by a
broken or burned bridge wire. Often cause by an elec-
trical transient such as lightning.
Remedy:
Step 1.
Use an Ohmmeter and measure the resis-
tance between the EXC + and EXC- leads.
The value for the EXC leads should be
1106 ohms + - 5 ohms.
Step 2.
Use an Ohmmeter and measure the resis-
tance between the SIG + and SIG - leads
The value for the SIG leads should be
1,000 ohms + - 1 ohm.
Step 3.
Readings that exceed the ranges indicated
suggest damage and the load cell should
be throroughly inspected or replaced.
Resistance to
Ground Test
Problem: Electrical leakage is creating an unstable
output from the instrument.
Cause:
Water contamination in the load sensors or
cables.
Remedy:
Step 1.
Tie together the load sensor excitation (2),
signal (2) and ground (1) wires.
NOTE:
Be careful NOT to include the two C2 wires.