Start up, Important – Bard WA602 User Manual
Page 16
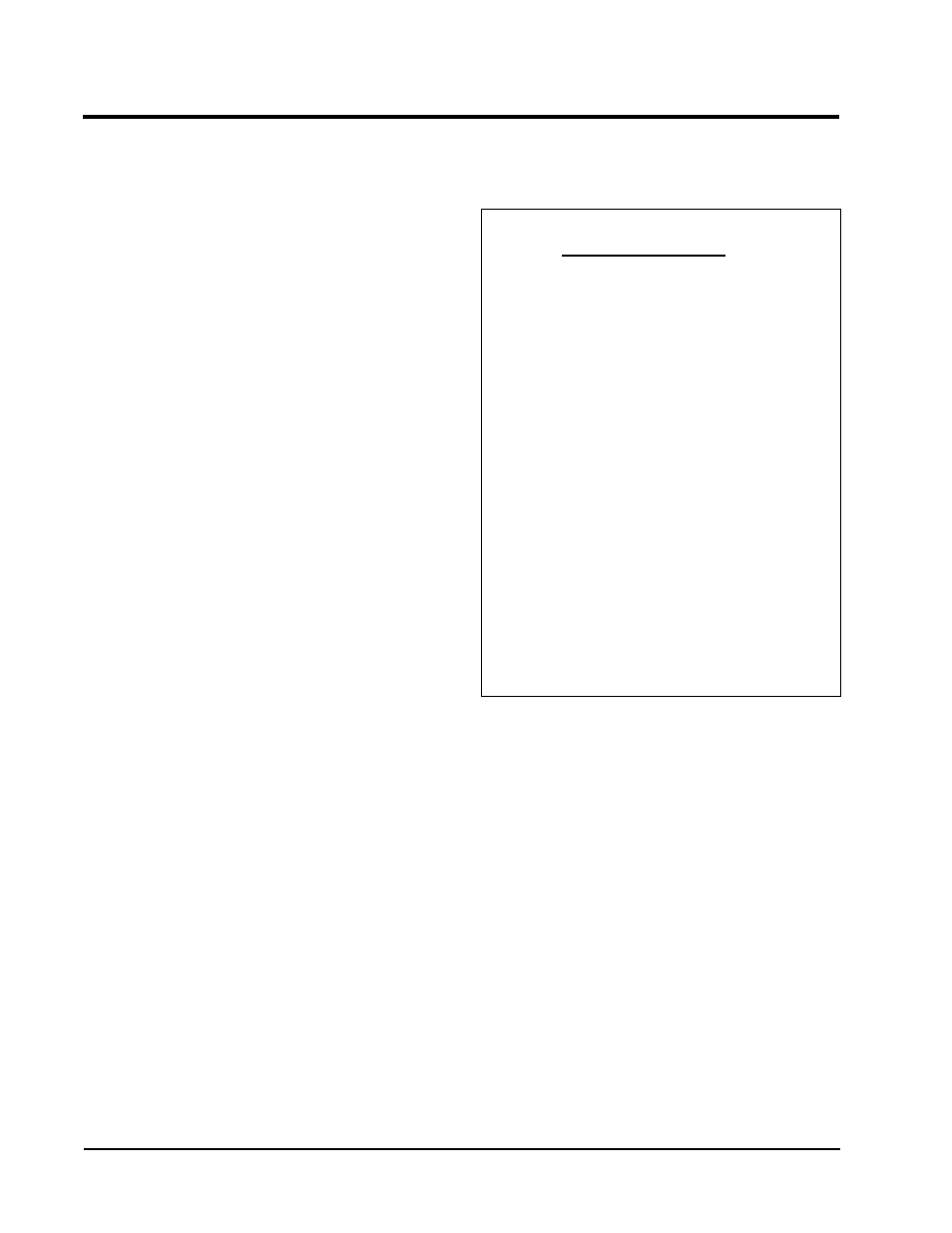
Manual 2100-218
Page 14
THREE PHASE SCROLL COMPRESSOR
START UP INFORMATION
Scroll compressors, like several other types of
compressors, will only compress in one rotational
direction. Direction of rotation is not an issue with single
phase compressors since they will always start and run in
the proper direction.
However, three phase compressors will rotate in either
direction depending upon phasing of the power. Since
there is a 50-50 chance of connecting power in such a
way as to cause rotation in the reverse direction,
verification of proper rotation must be made.
Verification of proper rotation direction is made by
observing that suction pressure drops and discharge
pressure rises when the compressor is energized. Reverse
rotation also results in an elevated sound level over that
with correct rotation, as well as, substantially reduced
current draw compared to tabulated values.
Verification of proper rotation must be made at the time
the equipment is put into service. If improper rotation is
corrected at this time there will be no negative impact on
the durability of the compressor. However, reverse
operation for over one hour may have a negative impact
on the bearing due to oil pump out.
NOTE:
If compressor is allowed to run in reverse rotation
for several minutes, the compressor’s internal
protector will trip.
All three phase ZR3 compressors are wired identically
internally. As a result, once the correct phasing is
determined for a specific system or installation,
connecting properly phased power leads to the same
Fusite terminal should maintain proper rotation direction.
The direction of rotation of the compressor may be
changed by reversing any two line connections to the
unit.
CONDENSER FAN OPERATION
The condenser fan motor on 230/208 volt, one and three
phase, 60 HZ units is a two speed motor that comes
factory wired on high speed for peak performance. If
ambient conditions permit, it can be reconnected to low
speed (red wire) for lower sound level. See wiring
diagram.
50 HZ models must have fan wired on low speed. These
models are factory wired on low speed.
START UP
IMPORTANT INSTALLER NOTE
For improved start up performance wash the indoor coil
with a dish washing detergent.
CRANKCASE HEATERS
WA421 units are provided with compressor crankcase
heat. WA602 and WA482 units are not provided with
crankcase heat. These units utilize scroll compressors
which do not require crankcase heat in this application.
The WA421 models have an insertion well-type heater
located in the lower section of the compressor housing.
This is a self-regulating type heater that draws only
enough power to maintani the compressor at a safe
termperature on these units.
Some form of crankcase heat is essential to prevent liquid
refrigerant from migating to the compressor causing oil
pump out on compressor start up and possible valve
failure due to compressing a liquid.
The decal in Figure 9 is affixed to all WA421 units
detailing start up procedure. This is very important.
Please read carefully.
HIGH PRESSURE SWITCH
The WA482 and WA602 models are supplied with a
remote reset high pressure switch. If tripped, this
pressure switch may be reset by turning the themostat off
then back on again.
FIGURE 9
STARTING PROCEDURE
IMPORTANT
THESE PROCEDURES MUST BE FOLLOWED AT
INITIAL START UP AND AT ANY TIME POWER
HAS BEEN REMOVED FOR 12 HOURS OR
LONGER.
To prevent compressor damage which may result
from the presence of liquid refrigerant in the
compressor crankcase.
1. Make certain the room thermostat is in the “off”
position (the compressor is not to operate).
2. Apply power by closing the system disconnect
switch. This energizes the compressor heater
which evaporates the liquid refrigerant in the
crankcase.
3. Allow 4 hours or 60 minutes per pound of
refrigerant in the system as noted on the unit
rating plate, which ever is greater.
4. After properly elapsed time, the thermostat
may be set to operate the compressor.
5. Except as required for safety while servicing,
Do not open system disconnect switch.
7961-061