Mammoth V-Cube User Manual
Page 30
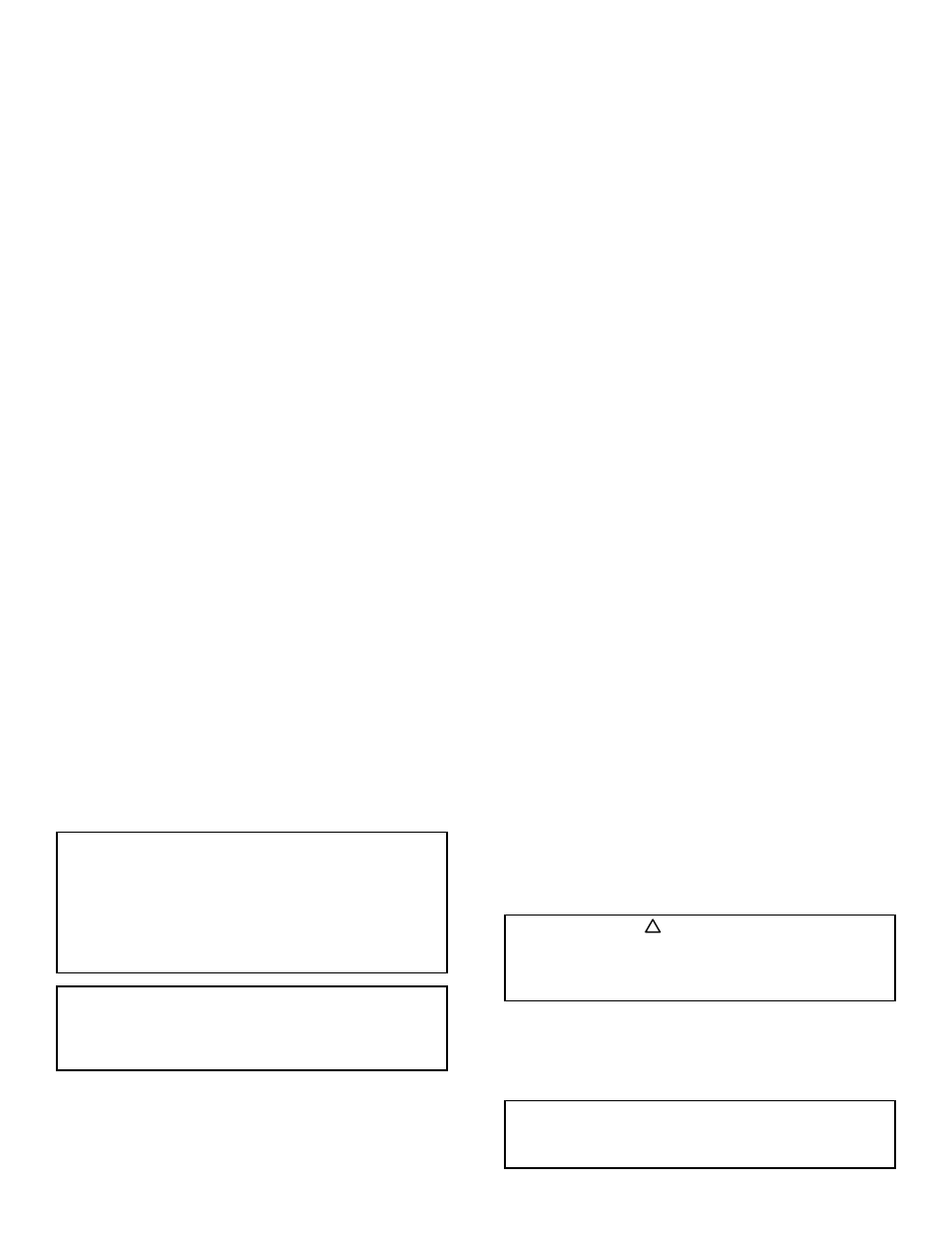
Monthly
• Check water cooled condensers for scaling and pro-
ceed with brushing and cleansing if necessary.
Quarterly
• Check oil level in compressor (half site glass).
Semi-annually
• Check operation of crankcase heaters.
• Check for broken or loose pipe clamps.
• Check moisture indicator of refrigerant site glass. A
“Caution” or “Wet” condition requires changing fil-
ter drier. If “Wet” condition does not improve, it will
be necessary to evacuate system.
Yearly
• Look for any sign of oil on all refrigeration compo-
nents including coils, compressors, controls, tubing,
etc. Oil would indicate a refrigerant leak.
• Check water lines for leaks.
• Check expansion valve bulb (properly attached to
suction line, properly isolated).
• Check the condensate drain pan and clean and flush
as required.
Troubleshooting
Lubrication
R410a should be used only with polyolester (POE) oil. The
HFC refrigerant components in R410a will not be compat-
ible with mineral oil or alkylbenzene lubricants. R410a
systems will be charged with the OEM recommended lu-
bricant, ready for use with R410a.
Charging
Due to the zeotropic nature of R410a, it should be
charged as a liquid. In situations where vapor is normally
charged into a system, a valve should be installed in the
charging line to flash the liquid to vapor while charging.
Compressor.Burnout
When a motor burnout occurs in a compressor, the result-
ing high temperature arc causes a portion of the refriger-
ant/oil mixture to break down into carbonaceous sludge,
corrosive acid, and water. Such contamination resulting
from a burnout can result in repeat failures if the contami-
nants are allowed to reach and remain in the crankcase
of the replacement compressor. This situation can be
prevented by following proper cleanup procedures after a
burnout.
To determine if a compressor burnout has actually oc-
curred, run the proper electrical tests. This requires an ac-
curate VOM Meter.
1. With all wires removed from the compressor termi-
nals, measure resistance from each terminal to the
compressor casing. If any terminal shows a direct
ground (zero resistance), a failure has occurred. If
not, continue.
2. With all wires removed from the compressor terminals,
measure resistance from each compressor terminal.
They should read the same. If two or more terminals
show zero resistance between them, the compressor
motor has failed (for actual resistance value, refer to
the respective compressor manual or contact the Cus-
tomer service Department at Venmar CES).
3. If steps 1 and 2 have not clearly identified a compres-
sor failure, it will be necessary to meg the compres-
sor motor (refer to the respective compressor manual
or contact the Customer service Department at Ven-
mar CES).
Compressor.Burnout.–.System.Cleanup
Any maintenance requiring refrigerant evacuation must be
performed using proper recovery procedures.
1. In order to avoid losing refrigerant to the atmo-
sphere, recover refrigerant using standard recovery
procedures and equipment. Remove the inoperative
compressor, and install the replacement.
2. Since the normal color of refrigerant oil varies from
oil to oil, take a sample of oil from the replacement
compressor and seal in a small glass bottle for com-
parison purposes after the cleaning operation is com-
plete. Suitable two ounce bottles are available at any
drug store.
3. Inspect all system controls such as expansion valves,
solenoid valves, check valves, reversing valves, con-
tactors, etc. Clean or replace if necessary, remove all
installed filter driers.
CAUTION
It is very important to make certain that the recycle or re-
covery equipment used is designed for R410a. The pres-
sure of R410a refrigerant is approximately 60% greater
than that of R22. Pressure gauges require a range up to
800 psig high side and 250 psig low side. Recovery cylin-
ders require a 400 psig rating.
IMPORTANT
Filter driers must be replaced each time a system is open
to atmosphere (ex.: for a defective component replace-
ment, refrigerant leak, etc.).
IMPORTANT
Before starting the new compressor, replace any ques-
tionable components.
!
WARNING
Acid burns to the skin can result from touching the sludge
in the burned out compressor. Rubber gloves should be
worn when handling contaminated parts.
VCES-V-CUBE-IOM-1A
30